RUNNING THE SITE
Page 43
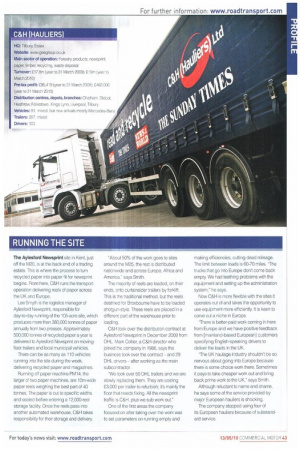
If you've noticed an error in this article please click here to report it so we can fix it.
The Aylesford Newsprint site in Kent, just off the M20, is at the back end of a trading estate. This is where the process to turn recycled paper into paper fit for newsprint begins. From here, C&H runs the transport operation delivering reels of paper across the UK and Europe.
Lee Srnyth is the logistics manager of Aylesford Newsprint, responsible for day-to-day running of the 105-acre site, which produces more than 380,000 tonnes of paper annually from two presses. Approximately 500,000 tonnes of recycled paper a year is delivered to Aylesford Newsprint on movingfloor trailers and local municipal vehicles.
There can be as many as 110 vehicles running into the site during the week, delivering recycled paper and magazines.
Running off paper machine PM14, the larger of two paper machines, are 10m-wide paper reels weighing the best part of 40 tonnes. The paper is cut to specific widths and sealed before entering a 12,000-reel storage facility. Once the reels pass into another automated warehouse, C&H takes responsibility for their storage and delivery. "About 50% of the work goes to sites around the M25, the rest is distributed nationwide and across Europe, Africa and America," says Smith.
The majority of reels are loaded, on their ends, onto curtainsider trailers by forklift. This is the traditional method, but the reels destined for Broxbourne have to be loaded shotgun-style. These reels are placed in a different part of the warehouse prior to loading.
C&H took over the distribution contract at Aylesford Newsprint in December 2009 from DHL. Mark Collier, a C&H director who joined the company in 1986, says the business took over the contract and 29 DHL drivers after working as the main subcontractor, "We took over 50 DHL trailers and we are slowly replacing them. They are costing 23,000 per trailer to refurbish; it's mainly the floor that needs fixing. All the newsprint traffic is C&H, plus we sub work out."
One of the first areas the company focused on after taking over the work was to set parameters on running empty and making efficiencies, cutting dead mileage. The limit between loads is 60-70 miles. "The trucks that go into Europe don't come back empty. We had teething problems with the equipment and setting up the administration system," he says.
Now C&H is more flexible with the sites it operates out of and takes the opportunity to use equipment more efficiently. It is keen to carve out a niche in Europe.
'There is better-paid work coming in here from Europe and we have positive feedback from [mainland-based European] customers specifying English-speaking drivers to deliver the loads In the UK.
The UK haulage industry shouldn't be so nervous about going into Europe because there is some choice work there. Sometimes it pays to take cheaper work out and bring back prime work to the UK," says Smith.
Although reluctant to name and shame, he says some of the service provided by major European hauliers is shocking.
The company stopped using four of its European hauliers because of substandard service.