TIPPING THE BALANCE
Page 54
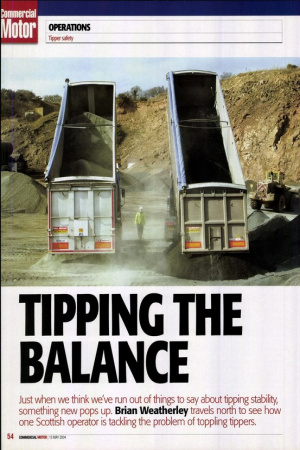
Page 55
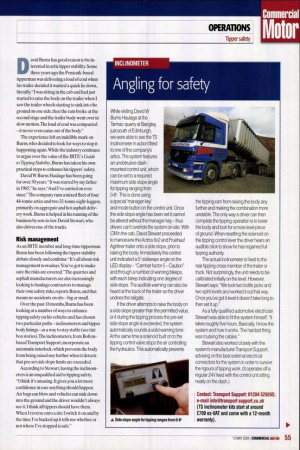
Page 57
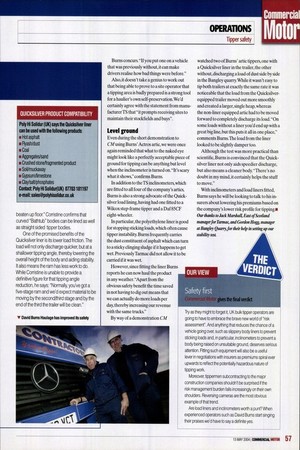
Page 56

If you've noticed an error in this article please click here to report it so we can fix it.
Just when we think we've run out of things to say about tipping stability, something new pops up. Brian Weatherley travels north to see how
one Scottish operator is tackling the problem of toppling tippers.
David Burns has good reason to be interested in artic tipper stability. Some three years ago the Penicuik-based tipperman was delivering a load of coal when his trailer decided it wanted a quick lie down, literally."I was sitting in the cab and had just started to raise the body on the trailer when I saw the trailer wheels starting to sink into the ground on one side, then the ram broke at the second stage and the trailer body went over in slow motion. The load of coal was compacted — it never even came out of the body."
The experience left an indelible mark on Burns, who decided to look for ways to stop it happening again. While the industry continues to argue over the value of the IRTE's Guide to Tipping Stability, Burns has taken his own practical steps to enhance his tippers' safety.
David W Burns Haulage has been going for over 30 years. "It was started by my father in 1965," he says. "And I've carried on ever since."The company runs a mixed fleet of four 44-tonne artics and two 32-tonne eight-leggers, primarily on aggregate and hot asphalt delivery work. Burns is helped in his running of the business by son-in-law David Stewart, who also drives one of the trucks. Risk management
As an IRTE member and long-time tipperman Burns has been following the tipper stability debate closely and confirms:"It's all about risk management nowadays.You've got to make sure the risks are covered."The quarries and asphalt manufacturers are also increasingly looking to haulage contractors to manage their own safety risks, reports Burns, and that means no accidents on site — big or small.
Over the past 18 months, Burns has been looking at a number of ways to enhance tipping safety on his vehicles and has chosen two particular paths —inclinometers and tipper body linings — as a way to stay stable (see tint box stories).The inclinometers, from Boltonbased Transport Support, incorporate an automatic interlock, which prevents the body from being raised any further when it detects that pre-set side slope limits are exceeded.
According to Stewart, having the inclinometers is an unqualified aid to tipping safety. "I think it's amazing. It gives you a lot more confidence in case anything should happen. Air bags can blow and vehicles can sink down into the ground and the driver wouldn't always see it. I think all tippers should have them. When I reverse onto a site I switch it on and by the time I've backed up it tells me whether or not where I've stopped is safe."
Burns concurs. "If you put one on a vehicle that was previously without, it can make drivers realise how bad things were before."
Also, it doesn't take a genius to work out that being able to prove to a site operator that a tipping area is badly prepared is a strong tool for a haulier's own self-preservation. We'd certainly agree with the statement from manufacturer TS that "it prompts receiving sites to maintain their stockfields and bays". Level ground
Even during the short demonstration to CM using Bums' Actros artic, we were once again reminded that what to the naked eye might look like a perfectly acceptable piece of ground for tipping can be anything but level when the inclinometer is turned on. "It's scary what it shows," confirms Burns.
In addition to the TS inclinometers, which are fitted to all four of the company's artics, Burns is also a strong advocate of the Quicksilver load lining, having had one fitted to a Wilcox step-frame tipper and a Daf 85CF eight-wheeler.
In particular, the polyethylene liner is good for stopping sticking loads, which often cause tipper instability. Bums frequently carries the dust constituent of asphalt which can turn to a sticky clinging sludge if it happens to get wet. Previously Tarmac did not allow it to be carried if it was wet.
However, since fitting the liner Bums reports he can now haul the product in any weather. "Apart from the obvious safety benefit the time saved in not having to dig out means that we can actually do more loads per day, thereby increasing our revenue with the same trucks." By way of a demonstration CM
watched two of Burns' artic tippers, one with a Quicksilver liner in the trailer, the other without, discharging a load of dust side by side in the Bangley quarry. While it wasn't easy to tip both trailers at exactly the same rate it was noticeable that the load from the Quicksilverequipped trailer moved out more smoothly and created a larger, single heap, whereas the non-liner equipped artic had to be moved forward to completely discharge its load. "On some loads without a liner you'd end up with a great big line, but this puts it all in one place," comments Bums.The load from the liner looked to be slightly damper too.
Although the test was more practical than scientific, Burns is convinced that the Quicksilver liner not only aids speedier discharge, but also means a cleaner body. "There's no doubt in my mind, it certainly helps the stuff to move." With inclinometers and load liners fitted, Burns says he will be looking to talk to his insurers about lowering his premiums based on the company's lower risk profile for tipping.• Our thanks to Jack Marshal East of Scotland manager for Tarmac, and Gordon Hogg manager at Bangley Quarty, for their help in setting up our stability teL Angling for safety
While visiting David W Burns Haulage at the Tarmac quarry at Bangley, just south of Edinburgh, we were able to see the TS Inclinometer in action fitted to one of the company's artics. The system features an unobtrusive dashmounted control unit, which can be set to a required maximum side slope angle for tipping ranging from 0-8°. This is done using a special 'manager key' and mode button on the control unit. Once the side slope angle has been set it cannot be altered without the manager key — thus drivers can't override the system on-site. With CMin the cab, David Stewart proceeded to manoeuvre the Actros 6x2 and Fruehauf Agriliner trailer onto a side slope, prior to raising the body. Immediately the control unit indicated a 5° sideways angle on the LED display — "Camber factor 5 —Caution" and through a number of warning bleeps, with each bleep indicating one degree of side slope. The audible warning can also be heard at the back of the trailer as the driver undoes the tailgate. If the driver attempts to raise the body on a side slope greater than the permitted value, or if during the tipping process the pre-set side slope angle is exceeded, the system automatically sounds a solid warning tone. At the same time a solenoid built on to the tipping control valve stops the air controlling the hydraulics. This automatically prevents
the tipping ram from raising the body any further and making the combination more unstable. The only way a driver can then complete the tipping operation is to lower the body and look for a more level piece of ground. When resetting the solenoid on the tipping control lever the driver hears an audible click to show he has regained full tipping authority.
The actual inclinometer is fixed to the rear tipping cross member of the trailer or truck. Not surprisingly, the unit needs to be calibrated initially on the level. However, Stewart says: "We took two bottle jacks and two spirit levels and worked it out that way. Once you've got it level it doesn't take long to then set it up."
As a fully qualified automotive electrician Stewart was able to fit the system himself. "It takes roughly five hours. Basically, I know the system and how it works. The hardest thing was routeing the cables." Stewart also worked closely with the system's manufacturer Transport Support, advising on the best external electrical connectors for the system in order to survive the rigours of tipping work. (It operates off a regular 24V feed with the control unit sitting neatly on the dash.)
Contact: Transport Support: 01204 529265; e-mail inlo@transportsupport.co.uk (TS inclinometer kits start at around £700 ex-VAT and come with a 12-month warranty). Look for the silver lining
Made by US company Poly Hi Solidur, the Quicksilver "non-stick" tipper body liner is made from ultra high molecular weight (UHMW) polyethylene. Its high silicon content allows loads to be discharged with minimum friction. "You can tell you're standing on something that's more slippery the minute you walk on it," says Poly Hi Solidor (UK)'s sales manager Graham Corristine. "It has high abrasion resistance and is ideal for tackling compacted or sticking loads." The Quicksilver lining is supplied in sections —10 or 12ft wide — which are fusion
welded together and rolled into a single reel. Operators can choose between 10 or 12mm thicknesses, with the former being recommended for aggregate work while the latter is the choice for hot asphalt, not least as it offers extra insulation for the product. According to Corristine, the wear
resistant capabilities of Quicksilver are such that "they will outlast an alloy body by at least 2:1". The fusion welded seams are also guaranteed for two years. A Quicksilver liner costs £385 per linear metre for the 12mm thickness and £360 for the lOmm thickness. Those figures include the one-piece liner, leading edge protectors (LEPs), tailgate plate and fastenings, although the actual installation of the product is treated separately, says Corristine. "Here, we are just recovering our costs at around £350, dependant on the location of the truck. However, if an operator
has more than one body fitted at a time, then obviously prices will vary."
A sufficient length to fit either a rigid or trailer body is first taken from the reel. "It's a single piece that's used," confirms Corristine. Longitudinal scores corresponding to the interior width of the body are then made in the material so the liner edges can be folded upwards by 90° and attached to the sidewalls. The depth of the liner wall varies between 300-400mm, depending on whether it's fitted to a rigid or trailer. Absolute must
Up to 24 flush fasteners hold the liner in place and the top edges of the side walls are covered by the aluminium leading edge protector capping strip, which is screwed into place but left for the operator to finally weld along its length to stop any material dropping between the liner and the body. "That's an absolute must," says Corristine. The total fitting time is one day, if you include LEP welding at the time of fitment. However, ultimately Corristine is looking to provide pre-scored liner kits for individual operators to install themselves. "We want to sell it directly to hauliers. They tell us how it is. You can also retrofit it, as long as you haven't got a really
beaten up floor." Corristine confirms that curved "Bathtub" bodies can be lined as well as straight sided tipper bodies.
One of the promised benefits of the Quicksilver liner is its lower load friction. The load will not only discharge quicker, but at a shallower tipping angle, thereby lowering the overall height of the body and aiding stability. It also means the ram has less work to do. While Corristine is unable to provide a definitive figure for that tipping angle reduction, he says: "Normally, you've got a five-stage ram and we'd expect material to be moving by the second/third stage and by the end of the third the trailer will be clean." QUICKSILVER CASE STUDIES
Miles Fox Haulage has two Quicksilver liners fitted in eight-wheelers and another on order for a Fruehauf tipping trailer. The Clitheroe-based operator hauls wet and dry aggregate products and director Richard Fox reports: "On aggregates everything is out of the truck by the third stage. Asphalt takes a little longer and we may get a small residue left in occasionally. However, it's easy to clean out and the overall performance is much better than when the truck was unlined. We're expecting to get a much longer wear life than we would have had from an aluminium replacement floor — and there appears to be a significant improvement in thermal properties as well."
David Bums also appreciates the nonsticking capability of Quicksilver. "When you're carrying the 'Masterf lex' special round stone top dressing for a road surface it has special polymer mixed in with it to keep the bitumen on the stone," he says. "Once you've taken the cover off it only needs to get a cold wind on it and it can quickly solidify. If you let it stick in a body you need a jack hammer to get it out! The Quicksilver liner not only helps it to keep the temperature up but it keeps it moving." Tarmac Central has been looking at the Quicksilver liner and has been conducting thermal imaging tests on a section of UHMW polyethylene liner.
gives the final verdict
Try as they might to forget it, UK bulk tipper operators are going to have to embrace the brave new world of "risk assessment". And anything that reduces the chance of a vehicle going over, such as slippery body liners to prevent sticking loads and, in particular, inclinometers to prevent a body being raised on unsuitable ground, deserves serious attention. Fitting such equipment will also be a useful lever in negotiations with insurers as premiums spiral ever upwards to reflect the potentially hazardous nature of tipping work.
Moreover, tippermen subcontracting to the major construction companies shouldn't be surprised if the risk management burden falls increasingly on their own shoulders. Reversing cameras are the most obvious example of that trend.
Are load liners and inclinometers worth a punt? When experienced operators such as David Burns start singing their praises we'd have to say a definite yes.