3oldering,
Page 65
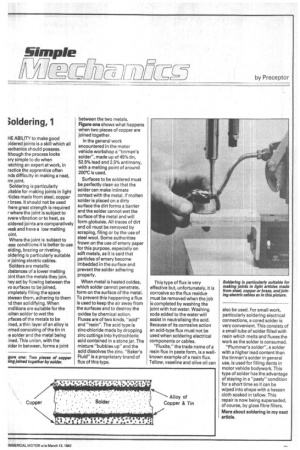
If you've noticed an error in this article please click here to report it so we can fix it.
HE ABILITY to make good 3Idered joints is a skill which all lechanics should possess. Ithough the process looks ary simple to do when fetching an expert at work, in ractice the apprentice often nds difficulty in making a neat, rm joint.
Soldering is particularly Jitable for making joints in light rticles made from steel, copper r brass. It should not be used 'here great strength is required r where the joint is subject to 3vere vibration or to heat, as oldered joints are comparatively teak and have a low melting oint.
Where the joint is subject to iese conditions it is better to use elding, brazing or riveting. oldering is particularly suitable ir joining electric cables. Solders are metallic
Jbstances of a lower melting Dint than the metals they join. hey act by flowing between the vo surfaces to be joined, )mpletely filling the space atween them, adhering to them 'id then solidifying. When )nditions are suitable for the iolten solder to wet the lrfaces of the metals to be ,ined, a thin layer of an alloy is irmed consisting of the tin in le solder and the metal being med. This union, with the )Ider in between, forms a joint
between the two metals. Figure one shows what happens when two pieces of copper are joined together.
In the general work encountered in the motor vehicle workshop a "tin man's solder", made up of 45% tin, 52.5% lead and 2.5% antimony, with a melting point of around 200°C is used.
Surfaces to be soldered must be perfectly clean so that the solder can make intimate contact with the metal. If molten solder is placed on a dirty surface the dirt forms a barrier and the solder cannot wet the surface of the metal and will form globules. All traces of dirt and oil must be removed by scraping, filing or by the use of steel wool. Some authorities frown on the use of emery paper for this purpose, especially on sat metals, as it is said that particles of emery become imbedded in the surface and prevent the solder adhering properly.
When metal is heated oxides, which solder cannot penetrate, form on the surface of the metal. To prevent this happening a flux is used to keep the air away from the surfaces and to destroy the oxides by chemical action. Fluxes are of two kinds, "acid" and "resin". The acid type is zinc-chloride made by dropping zinc cuttings into hydrochloric acid contained in a stone jar. The mixture "bubbles up" and the acid dissolves the zinc. "Baker's Fluid" is a proprietary brand of flux of this type, This type of flux is very effective but, unfortunately, it is corrosive so the flux residue must be removed when the job is completed by washing the joint with hot water. Washing soda added to the water will assist in neutralising the acid. Because of its corrosive action an acid-type flux must not be used when soldering electrical components or cables.
"Fluxite," the trade name of a resin flux in paste form, is a wellknown example of a resin flux. Tallow, vaseline and olive oil can also be used. For small work, particularly soldering electrical connections, a cored solder is very convenient. This consists of a small tube of solder filled with resin which melts and fluxes the work as the solder is consumed.
"Plummer's solder", a solder with a higher lead content than the tinman's solder in general use, is used for filling dents in motor vehicle bodywork. This type of solder has the advantage of staying in a "pasty" condition for a short time so it can be wiped into shape with a hessen cloth soaked in tallow. This repair is now being superseded, of course, by glass fibre fillers.
More about soldering in my next article.