The Cost of Changing Design
Page 46
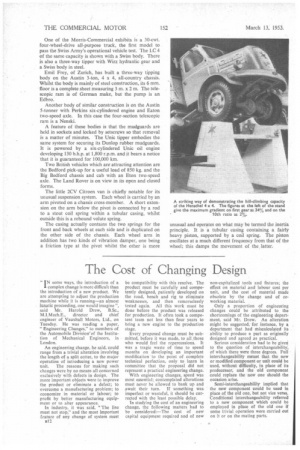
If you've noticed an error in this article please click here to report it so we can fix it.
"IN some ways, the introduction of a
I complex change is more difficult than the introduction of a new product. We are attempting to adjust the production machine while it is running—an almost lunatic proceeding, one would imagine ", said Mr. Harold Drew, B.Sc., M.I.Mech.E., director and chief engineer of Vauxhall Motors, Ltd., on Tuesday. He was reading a paper, "Engineering Changes," to members of the Automobile Division of the Institution of Mechanical Engineers, in London.
An engineering change, he said, could range from a trivial alteration involving the length of a split cotter, to the major operation of introducing a new power unit. The reasons for making such changes were by no means all concerned exclusively with defects in design. The more important objects were to improve the product or eliminate a defect; to overcome a manufacturing problem; to economize in material or labour; to profit by better manufacturing equipment or to alter appearance.
In industry, it was said, "The line must not stop," and the most important feature of any change of system must at 2
be compatibility with this resolve. The product must be carefully and competently designed, patiently developed on the road, bench and rig to eliminate weaknesses, and then remorselessly tested again. All this work must be done before the product was released for production. It often took a competent team not less than four years to bring a new engine to the production stage.
Every proposed change must be submitted, before it was made, to all those who would feel the repercussions. It was a tragic waste of time to spend months on developing an important modification to the point of complete technical perfection, only to learn in committee that the proposal did not represent a practical engineering change.
With engineering changes, speed was most essential;_ contemplated alterations must never be allowed to bank up and await their turn. If something was imperfect or wasteful, it should be corrected with the least possible delay.
In studying the cost of an engineering change, the following matters had to be considered:—The cost of new capital equipment required and of new non-capitalized tools and fixtures; the effect on material and labour cost per unit, and the cost of material made obsolete by the change and of reworking material.
Only a proportion of engineering changes could be attributed to the shortcomings of the engineering department, said Mr. Drew. An alteration might be suggested, for instance, by a . department that had miscalculated its ability to produce a part as originally designed and agreed as practical.
Serious consideration had to be given to the question of interchangeability, of which there were three degrees. Full interchangeability meant that the new or modified component or unit could be used, without difficulty, in place of its predecessor, and the old component could replace the new one should the occasion arise.
Semi-interchangeability implied that the new component could be used in place of the old one, but not vice versa. Conditional interchangeability referred to a new component which could be employed in place of the old one if some trivial operation were carried out on it or on the mating parts.