Time to tighten up There are about 25 million wheel
Page 31
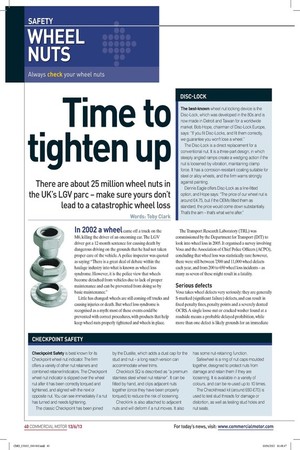
Page 32
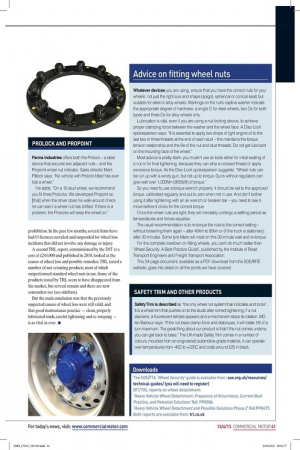
If you've noticed an error in this article please click here to report it so we can fix it.
nuts in the UK's LGV parc make sure yours don't lead to a catastrophic wheel loss Words: Toby Clark In 2002 a wheel came off a truck on the M6, killing the driver of an oncoming car. The LGV driver got a 12-month sentence for causing death by dangerous driving on the grounds that he had not taken proper care of the vehicle. A police inspector was quoted as saying: "There is a great deal of debate within the haulage industry into what is known as wheel loss syndrome. However, it is the police view that wheels become detached from vehicles due to lack of proper maintenance and can be prevented from doing so by basic maintenance."
Little has changed: wheels are still coming off trucks and causing injuries or death. But wheel loss syndrome is recognised as a myth: most of these events could be prevented with correct procedures, with products that help keep wheel nuts properly tightened and wheels in place. The Transport Research Laboratory (TRL) was commissioned by the Department for Transport (DfT) to look into wheel loss in 2005. It organised a survey involving Vosa and the Association of Chief Police Officers (ACPO), concluding that wheel loss was statistically rare: however, there were still between 7,500 and 11,000 wheel defects each year, and from 200 to 650 wheel loss incidents — as many as seven of these might result in a fatality.
Serious defects Vosa takes wheel defects very seriously: they are generally S-marked (significant failure) defects, and can result in fixed penalty fines, penalty points and a severely dented OCRS. A single loose nut or cracked washer found at a roadside means a probable delayed prohibition, while more than one defect is likely grounds for an immediate prohibition. In the past few months, several firms have had 0-licences curtailed and suspended for wheel loss incidents that did not involve any damage or injury.
A second TRL report, commissioned by the DfT at a cost of £243,000 and published in 2010, looked at the causes of wheel loss and possible remedies. TRL tested a number of nut-retaining products, most of which outperformed standard wheel nuts in use. Some of the products tested by TRL seem to have disappeared from the market, but several remain and there are new contenders too (see sidebars).
But the main conclusion was that the previously suspected causes of wheel loss were still valid, and that good maintenance practice — clean, properly lubricated studs, careful tightening and re-torquing — is as vital as ever. • DISC-LOCK The best-known wheel nut locking device is the Disc-Lock, which was developed in the 80s and is now made in Detroit and Taiwan for a worldwide market. Bob Hope, chairman of Disc-Lock Europe, says: "If you fit Disc-Locks, and fit them correctly, we guarantee you won't lose a wheel."
The Disc-Lock is a direct replacement for a conventional nut. It is a three-part design, in which steeply angled ramps create a wedging action if the nut is loosened by vibration, maintaining clamp force. It has a corrosion-resistant coating suitable for steel or alloy wheels, and the firm warns strongly against painting.
Dennis Eagleoffers Disc-Lock as a line-fitted option, and Hope says: "The price of our wheel nut is around £4.75, but if the OEMs fitted them as standard, the price would come down substantially. That's the aim —that's what we're after."
CHECKPOINT SAFETY Checkpoint Safety is best known for its Checkpoint wheel nut indicator. The firm offers a variety of other nut retainers and combined retainer/indicators. The Checkpoint wheel nut indicator is slipped over the wheel nut after it has been correctly torqued and tightened, and aligned with the next or opposite nut. You can see immediately if a nut has turned and needs tightening.
The classic Checkpoint has been joined by the Dustite,which adds a dust cap for the stud and nut— a long reach version can accommodate wheel trims.
Checklock SO is described as "a premium stainless steel wheel nut retainer". It can be fitted by hand, and clips adjacent nuts together (once they have been properly torqued) to reduce the risk of loosening.
Checklink is also attached to adjacent nuts and will deform if a nut moves. It also has some nut-retaining function.
Safewheel is a ring of nut caps moulded together, designed to protect nuts from damage and retain them if they are loosening. It is available in a variety of colours, and can be re-used up to 10 times.
The Checkthread kit (around £60-£70) is used to test stud threads for damage or distortion, as well as testing stud holes and nut seats. PROLOCK AND PROPOINT Parma Industries offers both the Prolock — a steel device that secures two adjacent nuts — and the Propoint wheel nut indicator. Sales director Mark Pittock says: "No vehicle with Prolock fitted has ever lost a wheel."
He adds: "On a 10-stud wheel, we recommend you fit three Prolocks. We developed Propoint so [that] when the driver does his walk-around check he can see if a wheel nut has shifted. If there is a problem, the Prolocks will keep the wheel on." Advice on fitting wheel nuts Whatever devices you are using, ensure that you have the correct nuts for your wheels: not just the right size and shape (spigot, spherical or conical seat) but suitable for steel or alloy wheels. Markings on the nut's captive washer indicate the appropriate degree of hardness: a single for steel wheels, two Os for both types and three Os for alloy wheels only.
Lubrication is vital, even if you are using a nut-locking device, to achieve proper clamping force between the washer and the wheel face. A Disc-Lock spokesperson says: "It is essential to apply two drops of light engine oil to the last two or three threads at the end of each stud — this maintains the torque tension relationship and the life of the nut and stud threads. Do not get lubricant on the mounting face of the wheel."
Most advice is pretty stark: you mustn't use air tools either for initial seating of a nut or for final tightening, because they can strip a crossed thread or apply excessive torque. As the Disc-Lock spokesperson suggests: "Wheel nuts can be run up with a windy gun, but not up to torque. Guns without regulators can give well over 1,200Nm (9001b/ft) of torque."
So you need to use a torque wrench properly: it should be set to the approved torque, calibrated regularly and put to zero when not in use. And don't bother using it after tightening with an air wrench or breaker bar — you need to see it move before it clicks for the correct torque.
Once the wheel nuts are tight, they will inevitably undergo a settling period as temperatures and forces equalise.
The usual recommendation is to re-torque the nuts to the correct setting — without loosening them again — after 40km to 80km or (if the truck is stationary) after 30 minutes. Some tyre fitters will insist on this 30-minute wait and re-torque.
For the complete lowdown on fitting wheels, you can't do much better than 'Wheel Security: A Best Practice Guide', published by the Institute of Road Transport Engineers and Freight Transport Association.
This 24-page document, available as a PDF download from the SOE/IRTE website, goes into detail on all the points we have covered.
SAFETY TRIM AND OTHER PRODUCTS SafetyTrim is described as "the only wheel nut system that indicates and locks". It is a wheel trim that pushes on to the studs after correct tightening; if a nut slackens, a fluorescent tell-tale appears and a mechanism stops its rotation. MD Ian Barbour says: "If the nut loses clamp force and detorques, it will rotate 1/6 of a turn maximum. The great thing about our product is that if the nut comes undone, you can get back to base." The UK-made Safety Trim comes in a number of colours; moulded from an engineered automotive-grade material, it can operate over temperatures from -400 to +2200 and costs around £25 in black.
Downloads 1 The 50E/FTA 'Wheel Security' guide is available from: soe.org.uk/resources/ technical-guides/ (you will need to register) DfT/TRL reports on wheel detachment: ' Heavy Vehicle Wheel Detachment: Frequency of Occurrence, Current Best Practice, and Potential Solutions' Ref. PPRO86 'Heavy Vehicle Wheel Detachment and Possible Solutions Phase Z Ref.PPR475 Both reports are available from: trl.co.uk