Endless round
Page 32
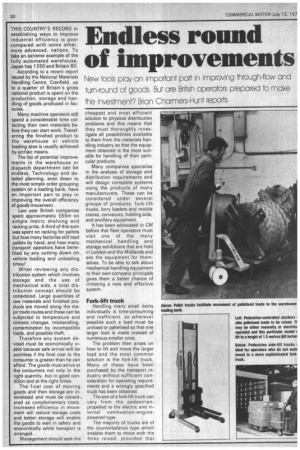
Page 33
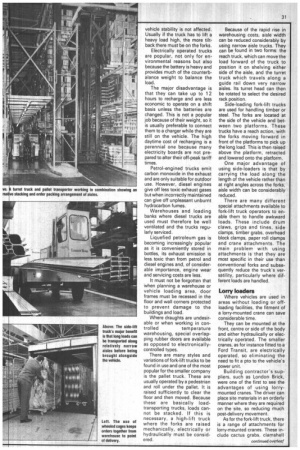
Page 34
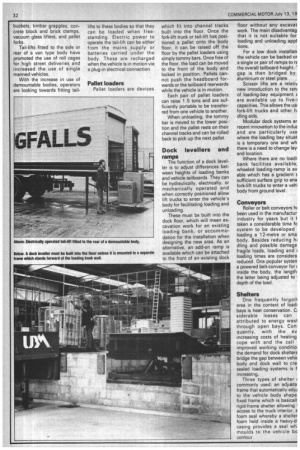
If you've noticed an error in this article please click here to report it so we can fix it.
rim of provenients New tools play an important part in improving rough-flow and turn-round of goods. But are British operators preparec to make e inves-ment? Brian Charmers-Hunt reports
THIS COUNTRY'S RECORD in establishing ways to improve industrial efficiency is poor compared with some other, more advanced, nations. To take an extreme example of the fully automated warehouse, Japan has 1350 and Britain 80.
According to a recent report issued by the National Materials Handling Centre, Cranfield, up to a quarter of Britain's gross national product is spent on the production, storage and handling of goods produced in factories.
Many machine operators still spend a considerable time collecting their own materials before they can start work. Transferring the finished product to the warehouse or vehicle loading area is usually achieved by archaic means.
The list of potential improvements in the warehouse or dispatch department can be endless. Technology and detailed planning, •even down to the most simple order grouping system on a loading bank, have an important part to play in improving the overall efficiency of goods movement.
Last year British companies spent approximately £.55m on simple metric shelving and racking units. A third of this sum was spent on racking for pallets but how many factories still load pallets by hand, and how many transport operators have benefited by any cutting down on vehicle loading and unloading times?
When reviewing any distribution system which involves storage and the use of mechanical aids, a total distribution concept should be considered. Large quantities of raw materials and finished products are moved along the major trade routes and these can be subjected to temperature and climatic changes, mishandling, contamination by incompatible loads, and possible theft.
Therefore any system devised must be economically viable because safe arrival will be pointless if the final cost to the consumer is greater than he can afford. The goods must arrive at the consumers not only in the right quantity, but in good condition and at the right times.
The final cost of moving goods and then storage are interrelated and must be consid-. ered as complementary costs. Increased efficiency in movement will reduce storage costs and better storage will enable the goods to wait in safety and economically while transport is arranged.
Management should seek the cheapest and most efficient solution to physical distribution problems and this means that they must thoroughly investigate all possibilities available to them from the materials handling industry so that the equipment obtained is the most suitable for handling of their particular products.
Many companies specialise in the analysis of storage and distribution requirements and will design complete systems using the products of many manufacturers. These can be considered under several groups of products: fork-lift. trucks, lorry loaders and mobile cranes, conveyors, holding aids, and ancillary equipment.
It has been advocated in CM before that fleet operators must visit one of the many mechanical handling and storage exhibitions that are held in London and the Midlands and see the equipment for themselves. To be able to talk about mechanical handling equipment to their own company principals gives them a better chance of initiating a new and effective system.
Fork-lift truck
Handling many small items individually is time-consuming and inefficient, so wherever possible such a load must be unitised or palletised so that one larger load is made instead of numerous smaller ones.
The problem then arises on how to lift and move the larger load and the most common solution is the fork-lift truck. Many of these have been purchased by the transport industry without sufficient consideration for operating requirements and a wrongly specified truck has been obtained.
The size of a fork-lift truck can vary from the pedestrianpropelled to the electric and internal combustion-enginepowered type.
The majority of trucks are of the counterbalance type which enables them to move with the forks raised, provided that vehicle stability is not affected. Usually if the truck has to lift a heavy load high, the more tiltback there must be on the forks.
Electrically operated trucks are popular, not only for environmental reasons but also because the battery is heavy and provides much of the counterbalance weight to balance the load.
The major disadvantage is that they can take up to 1 2 hours to recharge and are less economic to operate on a shift basis unless the batteries are changed. This is not a popular job because of their weight, so it is usually preferable to connect them to a charger while they are still on the vehicle. The high daytime cost of recharging is a perennial one because many electricity boards are not prepared to alter their off-peak tariff times.
Petrol-engined trucks emit carbon monoxide in the exhaust and are only suitable for outdoor use. However, diesel engines give off less toxic exhaust gases but when incorrectly maintained can give off unpleasant unburnt hydrocarbon fumes.
Warehouses and loading banks where diesel trucks are used must therefore be well ventilated and the trucks regularly serviced.
Liquefied petroleum gas is becoming increasingly popular as it is conveniently stored in bottles, its exhaust emission is less toxic than from petrol and diesel engines and, of considerable importance, engine wear and servicing costs are less.
It must not be forgotten that When planning a warehouse or vehicle loading area, door frames must be recessed in the floor and wall corners protected to prevent damage to the buildings and load.
Where draughts are undesirable or when working in con trolled temperature warehousing, special overlapping rubber doors are available as opposed to electronicallycontrolled types.
There are many styles and variations of fork-lift trucks to be found in use and one of the most popular for the smaller company is the pallet truck. These are usually operated by a pedestrian and roll under the pallet. It is raised sufficiently to clear the floor and then moved. Because these are basically loadtransporting trucks, loads cannot be stacked. If this is necessary, a high-lift truck where the forks are raised mechanically, electrically or hydraulically must be considered. Because of the rapid rise in warehousing costs, aisle width can be reduced considerably by using narrow aisle trucks. They can be found in two forms: the reach tuck, which can move the load forward of the truck to position it on shelving either side of the aisle, and the turret truck which travels along a guide rail down very narrow aisles. Its turret head can then be rotated to select the desired rack position.
Side-loading fork-lift trucks are used for handling timber or steel. The forks are located at the side of the vehicle and between two platforms. These trucks have a reach action, with the forks moving forward in front of the platforms to pick up the long load. This is then raised above the platform, retracted and lowered onto the platform.
One major advantage of using side-loaders is that by carrying the load along the length of the vehicle rather than at right angles across the forks, aisle width can be considerably reduced.
There are many different special attachments available to fork-lift truck operators to enable them to handle awkward loads. These include drum claws, grips and tines, side clamps, timber grabs, overhead block clamps, paper roll clamps and crane attachments. The main problem with using attachments is that they are most specific in their use than conventional forks and subsequently reduce the truck's versatility, particularly where different loads are handled.
Lorry loaders
Where vehicles are used in areas without loading or offloading facilities, the fitment of a lorry-mounted crane can save considerable time.
They can be mounted at the front, centre or side of the body and either hydraulically or electrically operated. The smaller cranes, as for instance fitted to a Ford Transit, are electrically operated, so eliminating the need to fit a pto to the vehicle's power unit.
Building contractor's suppliers, such as London Brick, were one of the first to see the advantages of using lorrymounted cranes. The driver can place site materials in an orderly manner where they are required on the site, so reducing much post-delivery movement.
As for the fork-lift truck, there is a range of attachments for lorry-mounted cranes. These include cactus grabs, clamshell buckets, timber grapples, concrete block and brick clamps, vacuum glass lifters, and pallet forks.
Tail-lifts fitted to the side or rear of a van type body have promoted the use of roll cages for high street deliveries and increased the use of single manned vehicles.
With the increase in use of demountable bodies, operators are looking towards fitting tail lifts to these bodies so that they can be loaded when freestanding. Electric power to operate the tail-lift can be either from the mains supply or batteries carried under the body. These are recharged when the vehicle is in motion via a plug-in electrical connection.
Pallet loaders
Pallet loaders are devices which fit into channel tracks built into the floor. Once the fork-lift truck or tail-lift has positioned a pallet onto the body floor, it can be raised off the floor by the pallet loaders using simply tommy bars. Once free of the floor, the load can be moved to the front of the body and locked in position. Pallets cannot push the headboard forwards or the tai i boa rd rearwards while the vehicle is in motion.
Each pair of pallet loaders can raise 1.5 tons and are sufficiently portable to be transferred from one vehicle to another.
When unloading, the tommy bar is moved to the lower position and the pallet rests on their channel tracks and can be rolled back to pick up the next pallet.
Dock levellers and ramps
The function of a dock leveller is to adjust differences between heights of loading banks and vehicle tailboards. They can be hydraulically, electrically, or mechanically operated and when correctly positioned allow lift trucks to enter the vehicle's body for facilitating loading and unloading.
These must be built into the dock floor, which will mean excavation work for an existing loading bank, or accommodation for the installation when designing the new area. As an alternative, an add-on ramp is available which can be attached to the front of an existing dock floor without any excavat work. The main disadvantag that it is not suitable for loading and unloading appl tions.
For a low dock installati the vehicle can be backed or a single or pair of ramps to rz the overall tailboard height. gap is then bridged by aluminium or steel plate.
Scissor lifts are a relativ new introduction to the rani of loading-bay equipment E are available up to five-1 capacities. This allows the us( fork-lift trucks and other h dling aids.
Modular dock systems ar recent innovation to the induE and are particularly use where the loading bay situat is a temporary one and wh there is a need to change lay, and location.
Where there are no loadr bank facilities available, wheeled loading-ramp is av able which has a gradient E sufficient surface grip to ena fork-lift trucks to enter a vehi body from ground level.
Conveyors
Roller or belt conveyors hi been used in the manufactur industry for years but it l• taken a considerable time to system to be developed loading a 12-metre or sma body. Besides reducing hi dling and possible damage fragile loads, loading and loading times are considera reduced. One popular systerr a powered belt-conveyor for t inside the body, the length the latter being adjusted to depth of the load.
Shelters One frequently forgott area in the context of loadi bays is heat conservation. CI siderable losses can attributed to energy wast through open bays. Con: quently, with the ev increasing costs of heating cope with and the call improved working conditio, the demand for dock shelters bridge the gap between vehic body and dock wall to crei sealed loadingsystems is f increasing.
Three types of shelter ( commonly used: an adjusta frame that automatically adju to the vehicle body shape fixed frame which is basicall. rigid-frame shelter allowing I access to the truck interior, a foam seal whereby a shelter foam held inside a heavy-d, casing provides a seal wh moulds to the vehicle bo contour.