They'll pack up your troubles
Page 30
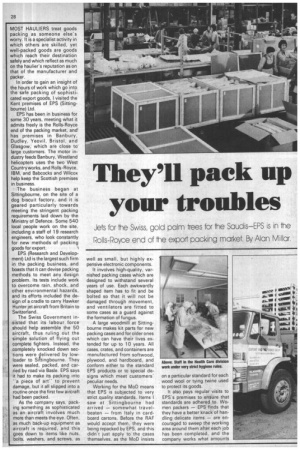
Page 31
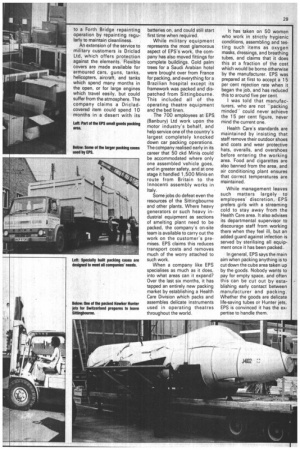
If you've noticed an error in this article please click here to report it so we can fix it.
Jets for he Swiss, gold palm trees for the Saudis—EPS is in the Rolls-Royce end of ne export packing market. By Alan Millar.
MOST HAULIERS treat goods packing as someone else's worry. It is a specialist activity in which others are skilled, yet well-packed goods are goods which reach their destination safely and which reflect as much on the haulier's reputation as on that of the manufacturer and packer.
In order to gain an insight of the hours of work which go into the safe packing of sophisticated export goods, I visited the Kent premises of EPS (Sittingbourne) Ltd.
EPS has been in business for some 30 years, meeting what it admits freely is the Rolls-Royce end of the packing market, and has premises in Banbury, Dudley, Yeovil, Bristol, and Glasgow, which are close to large customers. The motor industry feeds Banbury, Westland helicopters uses the two West Country works, and Rolls-Royce, IBM, and Babcocks and Wilcox help keep the Scottish premises in business.
The business began at Sittingbourne, on the site of a dog biscuit factory, and it is geared particularly towards meeting the stringent packing requirements laid down by the Ministry of Defence, Some 540 local people work on the site, including a staff of 19 research engineers, who look constantly for new methods of packing goods for export.
EPS (Research and Development) Ltd is the largest such firm in the packing business, and boasts that it can devise packing methods to meet any design problem. Its tests include work to overcome rain, shock, and other environmental hazards, and its efforts included the design of a cradle to carry Hawker Hunter jet aircraft from Britain to Switzerland.
The Swiss Government insisted that its labour force should help assemble the 50 aircraft, thus ruling out the simple solution of flying out complete fighters. Instead, the completely knocked down sec tions were delivered by low loader to Siitingbourne. They were sealed, packed, and car ried by road via Basle. EPS says
it had to make its packing into -a piece of art" to prevent damage, but it all slipped into a routine once the first few aircraft
had been packed.
As the company says, packing something as sophisticated as an aircraft involves much more than meets the eye. Often, as much back-up equipment as aircraft is required, and this goes down to items like nuts, bolts, washers, and screws, as well as small, but highly expensive electronic components.
It involves high-quality, varnished packing cases which are designed to withstand several years of use. Each awkwardly shaped item has to fit and be bolted so that it will not be damaged through movement, and ventilators are fitted to some cases as a guard against the formation of fungus.
A large woodmill at Sittingbourne makes kit parts for new packing cases and for older ones which can have their lives extended for up to 10 years. All cases, crates, and containers are manufactured from softwood, plywood, and hardboard, and conform either to the standard EPS products or to special designs which meet customers' peculiar needs.
Working for the MoD means that EPS is subjected to very strict quality standards. Items saw at Sittingbourne had arrived — somewhat travelbeaten — from Italy in cardboard cartons, Before the RAF would accept them, they were being repacked by EPS, and this didn't just apply to the cases themselves, as the MoD insists on a particular standard for each wood wool or tying twine used to protect its goods.
It also pays regular visits to EPS's premises to ensure that standards are adhered to. Women packers — EPS finds that they have a better knack of handling delicate items — are encouraged to sweep the working area around them after each job has been completed, and the company works what amounts to a Forth Bridge repainting operation by repainting regularly to maintain cleanliness.
An extension of the service to military customers is Driclad Ltd, which offers protection against the elements. Flexible covers are made available for armoured cars, guns, tanks, helicopters, aircraft, and tanks which spend many months in the open, or for large engines which travel easily, but could suffer from the atmosphere. The company claims a Dricladcovered item could spend 10 months in a desert with its batteries on, and could still start first time when required.
While military equipment represents the most glamorous aspect of EPS's work, the company has also moved fittings for complete buildings. Gold palm trees for a Saudi Arabian hotel were brought over from France for packing, and everything for a Brazilian hospital except its framework was packed and dispatched from Sittingbourne. This included all of the operating theatre equipment and the bed linen.
The 700 employees at EPS (Banbury) Ltd work upon the motor industry's behalf, and help service one of the country's largest completely knocked down car packing operations. The company realised early in its career that 50 ckd Minis could be accommodated where only one assembled vehicle goes, and in greater safety, and at one stage it handled 1,500 Minis en route from Britain to the Innocenti assembly works in Italy.
Some jobs do defeat even the resources of the Sittingbourne and other plants. Where heavy generators or such heavy industrial equipment as sections of smelting plant need to be packed, the company's on-site team is available to carry out the work on the customer's premises. EPS claims this reduces transport costs and removes much of the worry attached to such work.
When a company like EPS specialises as much as it does, into what areas can it expand? Over the last six months, it has tapped an entirely new packing market by establishing a Health Care Division which packs and assembles delicate instruments used in operating theatres throughout the world. It has taken on 50 women who work in strictly hygienic conditions, assembling and testing such items as oxygen masks, dressings, and breathing tubes, and claims that it does this at a fraction of the cost which would be borne otherwise by the manufacturer. EPS was prepared at first to accept a 15 per cent rejection rate when it began the job, and has reduced this to around five per cent.
I was told that manufacturers, who are not —packing minded— could never achieve the 15 per cent figure, never mind the current one.
Health Care's standards are maintained by insisting that staff remove their outdoor shoes and coats and wear protective hats, overalls, and overshoes before entering the working area. Food and cigarettes are also banned from the area, and air conditioning plant ensures that correct temperatures are maintained.
While management leaves such matters largely to employees' discretion, EPS prefers girls with a streaming cold to stay away from the Health Care area. It also advises its departmental supervisor to discourage staff from working there when they feel ill, but an added guard against infection is served by sterilising all equipment once it has been packed.
In general, EPS says the main aim when packing anything is to cut down the cube area taken up by the goods. Nobody wants to pay for empty space, and often this can be cut out by establishing early contact between manufacturer and packing. Whether the goods are delicate life-saving tubes or Hunter jets, EPS is convinced it has the expertise to handle them.