Cost tables and the small haulier
Page 33
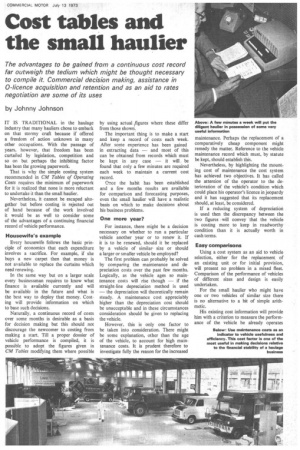
Page 34
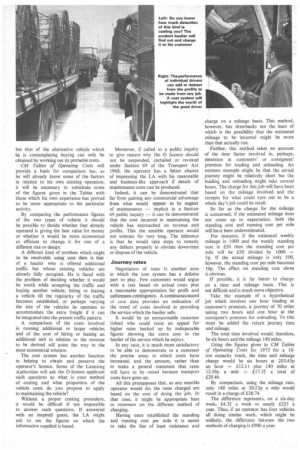
If you've noticed an error in this article please click here to report it so we can fix it.
The advantages to be gained from a continuous cost record far outweigh the tedium which might be thought necessary to compile it. Commercial decision making, assistance in 0-licence acquisition and retention and as an aid to rates negotiation are some of its uses by Johnny Johnson
IT IS TRADITIONAL in the haulage industry that many hauliers chose to embark on that stormy craft because if offered a freedom of action unknown in many other occupations. With the passage of years, however, that freedom has been curtailed by legislation, competition and so on but perhaps the inhibiting factor has been the growing paperwork.
That is why the simple costing system recommended in CM Tables of Operating Costs requires the minimum of paperwork for it is realized that none is more reluctant to undertake it than the small haulier.
Nevertheless, it cannot be escaped altogether but before costing is rejected out of hand because of the work involved it would be as well to consider some of the advantages of a continuing financial record of vehicle performance.
Housewife's example Every housewife follows the basic principle of economics that each expenditure involves a sacrifice. For example, if she buys a new carpet then that money is not available to replace the curtains which need renewing.
In the same way but on a larger scale every businessman requires to know what finance is available currently and will be available in the future and what is the best way to deploy that money. Costing will provide information on which to base such decisions.
Naturally, a continuous record of costs over some months is desirable as a basis for decision making but this should not discourage the newcomer to costing from making a start. Till a proper dossier of vehicle performance is compiled, it is possible to adopt the figures given in CM Tables modifying them where possible
by using actual ifigures where these differ from those shown.
The important thing is to make a start and keep a record of costs each week. After some experience has been gained in extracting data — and most of this can be obtained from records which must be kept in any case — it will . be found that only a few minutes are required each week to maintain a current cost record.
Once the habit has been established and a few months results are available for comparison and forecasting purposes, even the small haulier will have a realistic basis on which to make decisions about his business problems.
One more year?
For instance, there might be a decision necessary on whether to run a particular vehicle another year or to renew it. If it is to be renewed, should it be replaced by a vehicle of similar, size or should a larger or smaller vehicle be employed?
The first problem can probably be solved by comparing the maintenance and depreciation costs over the past few months. Logically, as the vehicle ages so maintenance costs will rise though — if the straight-line depreciation method is used — the depreciation will theoretically remain steady. A maintenance cost appreciably higher than the depreciation cost should be unacceptable and in these circumstances consideration should be given to replacing the vehicle.
However, this is only one factor to be taken into consideration. There might be some explanation, other than the age of the vehicle, to account for high maintenance costs. It is prudent therefore to investigate fully the reason for the increased
maintenance. Perhaps the replacement of a comparatively cheap component might remedy the matter,. Reference to the vehicle maintenance record which must, by statute be kept, should establish this.
Nevertheless, by highlighting the mounting cost of maintenance the cost system has achieved two objectives. It has called the attention of the operator to the deterioration of the vehicle's condition which could place his operator's licence in jeopardy and it has suggested that its replacement should, at least, be considered.
If a reducing system of depreciation is used then the discrepancy between the two figures will convey that the vehicle is costing more to keep in roadworthy condition than it is actually worth in cash terms.
Easy comparisons Using a cost system as an aid to vehicle selection, either for the replacement of an existing unit or for initial provision, will present no problem in a mixed fleet. Comparison of the performance of vehicles of different sizes and design is easily undertaken.
For the small haulier who might have one or two vehicles of similar size there is no alternative to a bit of simple arithmetic.
His existing cost information will provide him with a criterion to measure the performance of the vehicle he already operates but that of the alternative vehicle which he is contemplating buying can only be obtained by working out its probable costs.
CM Tables of Operating Costs will provide a basis for comparison but, as he will already know some of the factors in relation to his own existing operation, it will be necessary to substitute some of the figures given in the Tables with those which his own experience has proved to be more appropriate to his particular activity.
By comparing the performance figures of the two types of vehicle it should be possible to decide whether that already operated is giving the best value for money or whether it would be more economical or efficient to change it for one of a different size or design.
A different kind of problem which ought to be resolvable using cost data is that of a haulier who is offered additional traffic but whose existing vehicles are already fully occupied. He is faced with the problem of deciding whether it would be worth while accepting the traffic and buying another vehicle, hiring or leasing a vehicle till the regularity of the traffic becomes established, or perhaps varying the size of the vehicles he operates to accommodate the extra freight if it can be integrated into the present traffic pattern.
A comparison of the costs involved in running additional or larger vehicles and of the cost of hiring or leasing an additional unit in relation to the revenue to be derived will point the way to the most economical solution.
The cost system has another function in helping to obtain and preserve the operator's licence. Some of the Licensing Authorities will ask the 0-licence applicant such questions as what is your method of costing and what proportion of the vehicle costs do you propose to apply to maintaining the vehicle?
Without a proper costing procedure, it would be difficult if not impossible to answer such questions. If answered with an inspired guess, the LA might ask to see the figures on which the information supplied is based. Moreover, if called to a public inquiry to give reason why the 0 licence should not be suspended, curtailed or revoked under Section 69 of the Transport Act 1968, the operator has a better chance of impressing the LA with his reasonable and business-like approach if details of maintenance costs can be produced.
Indeed, it can be demonstrated that far from gaining any commercial advantage from what would appear to be neglect of maintenance — implicit in a Section 69 public inquiry — it can be demonstrated that the cost incurred in maintaining the vehicle has encroached on revenue and profits. This the sensible operator would not tolerate for very long. The inference is that he would take steps to remedy any defects properly to obviate down-time or dispose of the vehicle.
Journey rates
Negotiation of rates is another area in which the cost system has a definite part to play. Few customers would argue with a rate based on actual costs plus a reasonable appropriation for profit and unforeseen contingency. A continuous record of cost data provides an indication of the trend of costs involved in providing the service which the haulier sells.
It would be an unreasonable customer indeed who could resist an appeal for higher rates backed up by indisputable figures showing the extra cost to the haulier of the service which he enjoys.
In any case, it is much more satisfactory to be able to demonstrate to a customer the precise areas in which costs have increased, and the amount, rather than to make a general statement that rates will have to. be raised because transport costs have gone up.
All this presupposes that, as any sensible operator would do, the rates charged are based on the cost of doing the job. In that case, it might be appropriate here to comment on the different method of charging.
Having once established the standing and running cost per mile it is easier to take the line of least resistance and charge on a mileage basis. This method, however, has drawbacks not the least of which is the possibility that the estimated mileage to be incurred might be more than that actually run.
Further, this method takes no account of the time factor involved in, perhaps, detention at customers' or consignees' premises for loading and unloading. An extreme example might be that the actual journey might be relatively short but the loading and unloading might take several hours. The charge for this job will have been based on the mileage involved and the receipts for what could turn out to be a whole day's job could be small.
So far as the charge for the mileage is concerned, if the estimated mileage does not come up to expectation, both the standing cost and running cost per mile will have been underestimated.
For instance, if the estimated weekly mileage is 1000 and the weekly standing cost is £50 then the standing cost per mile will be £50 divided by 1000 = 5p. If the actual mileage is only 500, however, the standing cost per mile becomes 10p. The effect on standing cost alone is obvious.
If possible, it is far better to charge on a time and mileage basis. This is not difficult and is much more objective.
Take the example of a hypothetical job which involves one hour loading at customer's premises, a journey of 70 miles taking two hours and one hour at the consignee's premises for unloading. To this must be added the return journey time and mileage.
The total time involved would, therefore, be six hours and the mileage 140 miles.
Using the figures given in CM Tables of Operating Costs for 1973 for a 10 ton capacity truck, the time and mileage charge would be six hours at 203.45p an hour = £12.11 plus 140 miles at 12.39p a mile = £17.35 a total of £29.46.
By comparison, using the mileage rate, only 140 miles at 20.53p a mile would result in a charge of £28.74.
The difference represents, on a six-day week, £4.32 a week or nearly £225 a year. Thus, if an operator has four vehicles all doing similar work, which might be unlikely, the difference between the two methods of charging is £900 a year.