ROAD TRANSPOI EDUCES STEEL COSTS
Page 50
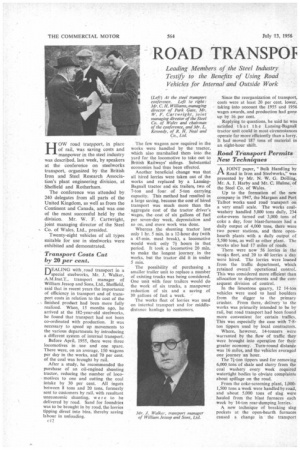
Page 51
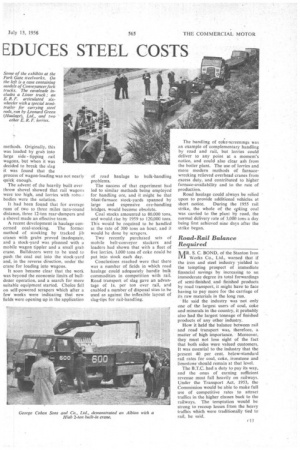
Page 52

If you've noticed an error in this article please click here to report it so we can fix it.
Leading Members of the Steel Industry Testify to the Benefits of Using Road Vehicles for Internal and Outside Work
HOW road transport, in place of rail, was saving costs and manpower in the steel industry was described, last week, by speakers at the conference on steelworks transport, organized by the British Iron and Steel Research Association's plant engineering division, at Sheffield and Rotherham.
The conference was attended by 240 delegates from all parts of the United Kingdom, as well as from the Continent and Canada, and was one of the most successful held by the division. Mr. W. F. Cartwright, joint managing director of the Steel Co. of Wales, Ltd., presided.
Twenty-eight vehicles of all types suitable for use in steelworks were exhibited and demonstrated.
Transport Costs Cut by 20 per cent.
DEALING with road transport in a I--"special steelworks, Mr. J. Walker, A.M.Inst.T., transport manager of William Jessop and Sons, Ltd., Sheffield, said that in recent years the importance of efficiency in transport and of transport costs in relation to the cost of the finished product had been more fully realized. When, 15 months ago, he arrived at the 182-year-old steelworks, he found that transport had not been co-ordinated with production. It was necessary to speed up movements to the various departments by introducing a different system of internal transport.
Before April, 1955, there were three locomotives in use and one spare. There were, on an average, 150 wagons per day in the works, and 70 per cent. of the coal was brought by rail.
After a study, he recommended the purchase of an oil-engined shunting tractor, reducing the number of locomotives to one and cutting the coal intake by 30 per cent. All ingots between 8 tons and 20 tons, formerly sent to customers by rail, with resultant uneconomic shunting, were to he delivered by road. Sand for foundries was to be brought in by road, the lorries tipping direct into bins, thereby saving labour in unloading.
The few wagons now required in the works were handled by the tractor, which also marshalled them into the yard for the locomotive to take out to British Railways' sidings. Substantial economies had thus been effected.
Another beneficial change was that all hired lorries were taken out of the works and replaced by a LansingBagnall tractor and six trailers, two of 7-ton and four of 5-ton carrying capacity. This method had resulted in a large saving, because the cost of hired transport was much more than the aggregate cost of the tractor driver's wages, the cost of six gallons of fuel per seven-day week, depreciation and so on, and more work was done.
Whereas the shunting tractor lost only 1 hr. 5 min_ in a 12-hour day (with a 45-min. meal break), a locomotive would work only 74 hours in that period. It took a locomotive 20 min. to make the longest journey in the works, but the tractor did it in under 5 min.
The possibility of purchasing a smaller trailer unit to replace a number of existing trucks was being considered. One unit with four trailers would do the work of six trucks, a manpower reduction of six and a saving of 30 gallons of fuel a week.
The works fleet of lorries was used on internal transport and for middledistance haulage to customers.
Since the reorganization of transport, costs were at least 20 per cent. lower, taking into account the 1955 and 1956 wages awards, and production had gone up by 16 per cent.
Replying to questions, he said he was satisfied that the Lansing-Bagnall tractor unit could in most circumstances operate far more efficiently than a lorry. It had moved 187 tons of material in an eight-hour shift.
Road Transport Permits New Techniques
A JOINT paper, "Bulk Handling by t-t Road in Iron and Steelworks," was presented by Mr. N. W. G. Dolling, Mr. A. J. Harby and Mr. C. Mime, of the Steel Co. of Wales.
Up to the formation of the new company in 1947, the Margam and Port Talbot works used road transport on a very small scale. The works coalwashery handled 5,000 tons daily, 234 coke-ovens turned out 3,000 tons of coke a day, four blast-furnaces had a daily output of 4,000 tons, there were two power stations, and three openhearth plants with a daily output of 3,500 tons, as well as other plant. The works also had 17 miles of roads.
There were now 56 lorries in the worics fleet, and 20 to 40 lorries a day were hired. The lorries were loaned from the traffic department, which retained overall operational control. This was considered more efficient than allocation to departments and the consequent division of control.
In the limestone quarry, 12 14-ton vehicles were used to haul boulders from the digger to the primary crusher, From there, • delivery to the works was primarily intended to be by rail, but road transport had been found more convenient for certain traffics. This was especially the ease with 7-8ton tippers used by local contractors.
Where, however, I4-toriners were warranted by the flow of traffic they were brought into operation for their greater economy. Turn-round distanee was 16 miles, and the vehicles averaged one journey an hour.
The 74-ton tippers used for removing 6,000 tons of shale and slurry from the coal washery every week required watertight bodies to obviate complaints about spillage on the road.
From the coke-screening plant, 1,0001,500 tons a week were handled by road, and about 5,000 tons of slag were hauled from the blast furnaces each week by 14-ton rear-dumping lorries.
A new technique of breaking slag pockets at the open-hearth furnaces caused a change in the transport methods. Originally, this was loaded by grab into large side tipping rail wagons, but when it was decided to break the slag it was found that the process of wagon-loading was not nearly quick enough.
The advent of the heavily built over throw shovel showed that rail wagons were too high, and lorries with rota' .1 bodies were the solution.
It had been found that for average runs of two to three miles turn-round distance, three I2-ton rear-dumpers and a shovel made an effective team.
A recent development in haulage concerned coal-stocking. The formet method of stocking by tracked jib cranes with grabs proved inadequate, and a stock-yard was planned with a mobile wagon tippler and a small grab crane. Bulldozers were to be used to push the coal out into the stock-yard and, in the reverse direction, under the crane for loading into wagons.
It soon became clear that the work was beyond the economic limits of bulldozer operation, and a search for more suitable equipment started. Choice fell on self-powered scrapers which after a few weeks were indicating that new fields were opening up in the application of road haulage to bulk-handling problems.
The success of that experiment had led to similar methods being employed for handling ore, and it might be that blast-furnace stock-yards spanned by large and expensive ore-handling bridges, would become obsolete.
Coal stocks amounted to 80,000 tons, and would rise by 1959 to 120,000 tons. This would be required to be handled at the rate of 300 tons an hour, and it would he done by scrapers_ Two recently purchased sets of mobile belt-conveyor stackers and loaders had shown that with a fleet of five lorries, 1,000 tons of coke could he put into stock each day.
Conclusions reached were that there was a number of fields in which road haulage could adequately handle bulk commodities in competition with rail. Road transport of slag gave an advantage of Is. per ton over rail, and enabled a number of disposal sites to be used as against the inflexible layout of slag-tips for rail-handling. The handling of coke-screenings was an example of complementary handling by road and rail, but lorries could deliver to any point at a moment's notice, and could also clear ash from the boiler plant. The use of lorries and more modern methods of furnacewrecking relieved overhead cranes from excess duty, and contributed to higher furnace-availability and to the rate of production.
Road haulage could always be relied upon to provide additional vehicles at
short notice. During the 1955 rail strike, the whole of the cpking coat was carried to the plant by road, the normal delivery rate of 3,060 tons a day being first achieved nine days after the strike began.
Road-Rail Balance Required
MR_ S. C. BOND, of the Stanton Iron Works Co., Ltd., warned that if the iron and steel industry yielded to the tempting prospect of immediate financial savings by increasing to an immoderate degree its total forwardings of semi-finished_ and finished products by road transport, it might have to face having to pay more for the carriage of its raw materials in the long run.
He said the industry was not only one of the largest users of coal, coke and minerals in the country, it probably also had the largest tonnage of finished products of any other industry.
How it held the balance between rail and road transport was, therefore, a matter of high importance. Moreover, they must not lose sight of the fact that both sides were valued customers. It was essential to the industry that the present 40 per cent, below-standard rail rates for coal, coke, ironstone and limesioneshould remain at that level.
The B.T.C. had a duty to pay its way, and the onus of earning sufficient revenue must fall heavily on railways. Under the Transport Act, 1953, the Commission would be able to make full use of competitive rates to attract traffics in the higher classes back to the railways. The temptation would be strong to recoup losses from the heavy traffics which were traditionally tied to rail, he said. It seemed to him that the industry's interests might best be served in the long run by keeping not only the ra* materials on rail, but by giving back to the railways a large proportion of the highest class of traffic which, in recent years, had gone by road.
It was as certain as anything could be that the more of that class of traffic carried by rail, the cheaper finally would be the generality of railway rates.
Big Movement from Rail to Road
IN his paper, Mr. W. D. Allen, of 11 the Park Gate Iron and Steel Co., Ltd., Rotherham, dealt with works producing 163,000 tons of pig iron and 355,000 tons .of ingots a year, where the production of ingots alone had increased by 60 per cent. in 10 years, with a corresponding increase in load on the transport department.
After reorganizing the rail system in the works, 15 road vehicles were purchased in 1947. By 1955, 24 lorries and two Scammell tractors hauling seven Dyson 20-ton trailers were in service. They hauled steel to customers and materials to outside concerns, did inter-departmental work and took rubbish to tips.
Eighty-seven per cent. of the company's products were delivered by road to customers within a radius of 80 miles, and during 1955 40 per cent, of the total steel delivered went by road. Customers had benefited greatly.
In the works, shunting operations were eliminated, and by using road transport, materials were taken from the works quicker.
Haulage between the departments meant dealing with 44 per cent. of the material rolled in the mill, carrying 68,000 tons of sections annually, tipping 21,000 tons of graded blast-furnace slag every year, and the general carriage of materials between departments. In addition, there was the disposal of 147,000 tons of works rubbish a year, a problem which had been eased by road transport because there was a ready market for the material.
A special dust-proofed body had been designed and fitted to a 74--ton tipper, and this saved time and air pollution, as well as cutting handling costs. The lorry was in operation 24 hours a day, and dealt with 400-500 tons of material a week.
Closer Co-operation Needed
pLEASURE that the road haulage
industry would no longer be bedevilled by political changes, at least for the time being, was expressed by Mr. Harold Elliott, of British Road Services.
He said that if it was important for the transport manager to understand the structure of his company's production methods, it was equally important that the carrier should be in the same position, He suggested they should c14
visit each other's premises. A closer exchange of views would result in better understanding of production and transport methods and problems.
British Road Services would welcome suggestions on any matter, and traders or manufacturers could, in turn, benefit by hearing some of their ideas, particularly when planning dispatch and reception facilities.
Whilst it was necessary for trade and industry to have its own transport, it could not, as a whole, expect the best and most economic service from the' haulier if it carried the best traffic in its own vehicles and left him with the bits and pieces, particularly to destinations where it was difficult to secure a return load.
They did not yet know what would be the effects on rates of the new railway charges scheme, if and when it was approved and implemented. What was certain was that there would be a closer relationship than hitherto between road and rail levels of charging. Whether or not it would make more difficult the task of exercising a choice between road and rail he did not know.
The expanding production of the steel industry was good in the national interest, but it was going to change the whole emphasis of traffic flow between certain points, and would cause steel manufacturers, the railways and hauliers to think seriously in the ye: to come.
On loading and unloading, he B.R.S. had done much to increase ava able carrying capacity, but more cot be done if trade and industry cot load or receive goods later.in the d; The five-day week was also restricti his organization's productivity, and would suggest that overtime payme in many circumstances could be 01 weighed by the earlier dispatch a more prompt delivery that would secured.
Road Transport Saves Manpower
I N a ..paper read in his absence, I Gresier described the great benel that had accrued to the French Creut works by transferring from rail to ro transport.
Since 1951, the management h decided to abandon rail transport favour of road haulage, because lorri gave a door-to-door service, often wi automatic discharge, and results we he said, amazing.
In 1951 the monthly tonnage earni was 123,000-42,000 by French Ra ways wagons, 66,000 in the compan! own rail wagons and 15,1300 tons internal lorry. In 1955, tonnage rc to 127,000 a month-18,000 by Fren Railways wagons, 39,000 in the co; pany's own wagons, and 70,000 lorries.
In that period, the locomotive flu had been reduced from 39 to 17, five which were in reserve. The numb of wagons had been reduced from 1,2 to 350, with a reduction from 80 to 5 men in the repair shop. The manpow now required was 198, against 337 1951. It was necessary to hire ea day three to IO lorries for interr transport.
The fleet of 32 lorries and trade including a 32-ton semi-trailer, whi was hired, handled more than 80 p cent. of the traffic. The transpt department was responsible for t handling equipment, as well as t lorries, including 100 10-ton " mul skip" lorries which removed ash al debris.
The works had two 10-ton lorr, capable of hoisting and tipping hydraulic control, enabling the 'd charge of coal into bunkers abc 2 metres above ground level. Strad( carriers, cranes on pneumatic tyri fork trucks, pallets, containers ai tractors were also used. The tractc were capable of shunting or pulli trailers of 10-ton capacity.
A wall chart was employed to Ice track of how the vehicles were bei employed. This showed the next, well as the current, day's comrnitmen and it enabled a job card to be pi pared for each lorry and a force: to be made of hiring requirements the 24 hours ahead.
Lorry drivers received a bonus relat to the number and nature of t journeys made.