Esso tanker loading will be fast and foolproof
Page 39
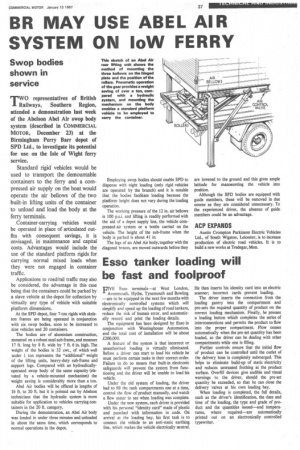
If you've noticed an error in this article please click here to report it so we can fix it.
pivE Esso terminals—at West London,
Avonmouth, Hythe, Tynemouth and Bowling —are to be equipped in the next few months with electronically controlled systems which will simplify and speed up the loading of road tankers, reduce the risk of human error, and automatically record and print the loading details.
The equipment has been designed by Esso in conjunction with Westinghouse Automation, and the total cost of installation will be about £200,000.
A feature of the system is that incorrect or unauthorized loading is virtually eliminated. Before a driver can start to load his vehicle he must perform certain tasks in their correct order. Failure to do so means that built-in electronic safeguards will prevent the system from functioning and the driver will be unable to load his vehicle.
Under the old system of loading, the driver had to fill the tank compartments one at a time, control the flow of product manually, and watch a flow meter to see when loading was complete.
Under the new system, each driver is provided with his personal "identity card" made of plastic and punched with information in code. On arrival at the loading bay, his first task is to connect the vehicle to an anti-static earthing line, which makes the vehicle electrically neutral. He then inserts his identity card into an electric scanner; incorrect cards prevent loading.
The driver inserts the connection from the loading gantry into the compartment and pre-sets the required quantity of product on the correct loading mechanism. Finally, he presses a loading button which completes the series of interconnections and permits the product to flow into the proper compartment. Flow ceases automatically when the pre-set quantity has been loaded, so the driver can be dealing with other compartments while one is filling.
Further controls ensure that the initial flow of product can be controlled until the outlet of the delivery hose is completely submerged. This helps to eliminate build-up of static electricity and reduces unwanted frothing at the product surface. Overfill devices give audible and visual warnings to the driver, should the pre-set quantity be exceeded, so that he can close the delivery valves at his own loading bay.
When loading is completed, the full details, such as the driver's identification, the date and time of the loading, the type and grade of product and the quantities issued—and temperatures, where required—are automatically printed out on an electronically controlled typewriter.