LOW FLOOR LOW-DOWN
Page 28
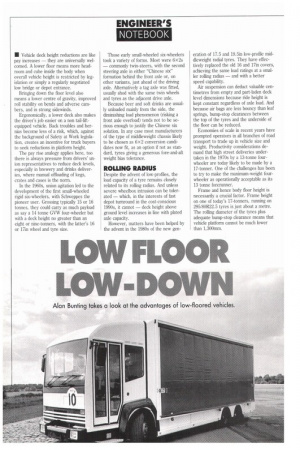
Page 29
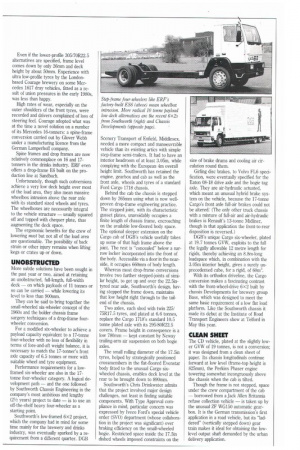
If you've noticed an error in this article please click here to report it so we can fix it.
Alan Bunting takes a look at the advantages of low-floored vehicles.
• Vehicle deck height reductions are like pay increases — they are universally welcomed. A lower floor means more headroom and cube inside the body when overall vehicle height is restricted by legislation or simply a regularly negotiated low bridge or depot entrance.
Bringing down the floor level also means a lower centre of gravity, improved roll stability on bends and adverse cambers, and in strong sidewinds.
Ergonomically, a lower deck also makes the driver's job easier on a non tail-liftequipped vehicle. Back troubles and hernias become less of a risk, which, against the background of Safety at Work legislation, creates an incentive for truck buyers to seek reductions in platform height.
The pay rise analogy applies here, too there is always pressure from drivers' union representatives to reduce deck levels, especially in brewery and drinks deliveries, where manual offloading of kegs, crates and cases is the norm.
In the 1960s, union agitation led to the development of the first small-wheeled rigid six-wheelers, with Schweppes the pioneer user. Grossing typically 15 or 16 tonnes, they could carry as much payload as say a 14 tonne GVW four-wheeler but with a deck height no greater than an eight or nine-tonners, with the latter's 16 or 17in wheel and tyre size. Those early small-wheeled six-wheelers took a variety of forms. Most were 6x 2s — commonly twin-steers, with the second steering axle in either "Chinese six" formation behind the front axle or, on other variants, just ahead of the driving axle. Alternatively a tag axle was fitted, usually shod with the same twin wheels and tyres as the adjacent drive axle.
Because beer and soft drinks are usually unloaded mainly from the side, the diminishing load phenomenon (risking a front axle overload) tends not to be serious enough to justify the Chinese six solution. In any case most manufacturers of the type of middleweight chassis likely to be chosen as 6x2 conversion candidates now fit, as an option if not as standard, tyres giving a generous fore-and-aft weight bias tolerance.
ROLLING RADIUS
Despite the advent of low-profiles, the load capacity of a tyre remains closely related to its rolling radius. And unless severe wheelbox intrusion can be tolerated — which, in the interests of fast depot tunround in the cost-conscious 1990s, it cannot — deck height above ground level increases in line with plated axle capacity.
However, matters have been helped by the advent in the 1980s of the new gen
eration of 17.5 and 19.5in low-profile middleweight radial tyres. They have effectively replaced the old 16 and 17in covers, achieving the same load ratings at a smaller rolling radius — and with a better speed capability.
Air suspension can deduct valuable centimetres from empty and part-laden deck level dimensions because ride height is kept constant regardless of axle load. And because air bags are less bouncy than leaf springs, bump-stop clearances between the top of the tyres and the underside of the floor can be reduced.
Economies of scale in recent years have prompted operators in all branches of road transport to trade up in vehicle size and weight. Productivity considerations demand that high street deliveries undertaken in the 1970s by a 13-tonne fourwheeler are today likely to be made by a 17-tonner. One of the challenges has been to try to make the maximum-weight fourwheeler as operationally acceptable as its 13 tonne forerunner.
Frame and hence body floor height is necessarily a crucial factor. Frame height on one of today's 17-tonners, running on 295/801(22.5 tyres is just about a metre. The rolling diameter of the tyres plus adequate bump-stop clearance means that vehicle platform cannot be much lower than 1,300mm. Even if the lower-profile 305/70R22.5 alternatives are specified, frame level comes down by only 26nun and deck height by about 50nun. Experience with ultra low-profile tyres by the Londonbased Courage brewery on some Mercedes 1617 dray vehicles, fitted as a result of union pressures in the early 1980s, was less than happy.
High rates of wear, especially on the outer shoulders of the front tyres, were recorded and drivers complained of loss of steering feel. Courage adopted what was at the time a novel solution on a number of its Mercedes 16-tonners: a spine-frame conversion carried out by Glover Webb under a manufacturing licence from the German Lamperhoff company.
Spine frames and drop frames are now relatively commonplace on 16 and 17tonners in the drinks industry. ERF even offers a drop-frame E6 built on the production line at Sandbach.
Unfortunately, though such conversions achieve a very low deck height over most of the load area, they also mean massive wheelbox intrusion above the rear axle with its standard sized wheels and tyres. The wheelboxes are necessarily integral to the vehicle structure — usually squared off and topped with chequer plate, thus augmenting the deck space.
The ergonomic benefits for the crew of lowering most but not all of the load area are questionable. The possibility of back strain or other injury remains when lifting kegs or crates up or down.
UNOBSTRUCTED
More subtle solutions have been sought in the past year or two, aimed at retaining an unobstructed, full-length, full-width deck — on which payloads of 11 tonnes or so can be carried — while lowering its level to less than 900mm.
They can be said to bring together the small-wheeled six-wheeler concept of the 1960s and the bolder chassis frame surgery techniques of a drop-frame fourwheeler conversion.
For a modified six-wheeler to achieve a payload capacity equivalent to a 17-tonne four-wheeler with no loss of flexibility in terms of fore-and-aft weight balance, it is necessary to match the 17-tonner's front axle capacity of 6.5 tonnes or more with suitable wheel and tyre equipment.
Performance requirements for a lowframed six-wheeler are also in the 17tonne four-wheeler category. A logical development path — and the one followed by Southworth Chassis Engineering in the company's most ambitious and lengthy (21/2 years) project to date — is to use an off-the-shelf heavy four-wheeler as a starting point.
Southworth's low-framed 6x2 project, which the company had in mind for some time mainly for the brewery and drinks industry, was eventually sparked by a requirement from a different quarter. DGB Scenery Transport of Enfield, Middlesex, needed a more compact and manoeuvrable vehicle than its existing artics with simple step-frame semi-trailers. It had to have an interior headroom of at least 3.05m, while complying with the European 4m overall height limit. Southworth has retained the engine, gearbox and cab as well as the front axle, wheels and tyres of a standard Ford Cargo 1718 chassis.
Behind the cab the chassis is stepped down by 265mm using what is now wellproven drop-frame engineering practice. The stepped joint, with its characteristic gusset plates, unavoidably occupies a finite length of chassis frame, encroaching on the available low-floored body space. The optional sleeper extension on the Cargo cab of DGB's vehicle usefully takes up some of that high frame above the joint. The rest is "concealed" below a narrow locker incorporated into the front of the body. Accessible via a door in the nearside, it occupies 660mm of body length.
Whereas most drop-frame conversions involve two further stepped-joints of similar height, to get up and over the 22.5intyred rear axle, Southworth's design, having stepped the frame down, maintains that low height right through to the tailend of the chassis.
Two axles, each shod with twin 225/ 75R17.5 tyres, and plated at 6.6 tonnes, replace the Cargo 1718's standard 10.5 tonne plated axle with its 295/80R22.5 covers. Frame height in consequence is a low 780mm — kept constant by Neway trailing-arm air suspension on both bogie axles.
The small rolling diameter of the 17.5in tyres, helped by strategically positioned crossmembers in the flat-floored Evenstar body fitted to the unusual Cargo sixwheeled chassis, enables deck level at the rear to be brought down to 890mm.
Southworth's Chris Drinkwater admits that the project involved major design challenges, not least in finding suitable components. With Type Approval compliance in mind, particular concern was expressed by Iveco Ford's special vehicle order (SVO) department (whose collaboration in the project was significant) over braking efficiency on the small-wheeled bogie. Restricted space inside the 17.5in dished wheels imposed constraints on the size of brake drums and cooling air circulation round them.
Girling disc brakes, to Volvo FL6 specification, were eventually specified for the Eaton 08-18 drive axle and the bogie tag axle. They are air-hydraulic actuated, which meant an unusual hybrid brake system on the vehicle, because the 17-tonne Cargo's front axle full-air brakes could not be altered: (The only other truck chassis with a mixture of full-air and air-hydraulic brakes is Renault's 13-tonne Midliner, though in that application the front-to-rear disposition is reversed.)
DGB's unique Cargo six-wheeler, plated at 19.7 tonnes GVW, exploits to the full the legally allowable 12 metre length for rigids, thereby achieving an 8.8m-long loadspace which, in combination with the 3.05m interior height, gives a surely unprecedented cube, for a rigid, of 60m3.
With its orthodox driveline, the Cargo conversion makes a fascinating contrast with the front-wheel-drive 6x2 built by chassis Developments for brewery group Bass, which was designed to meet the same basic requirement of a low flat load platform. Like the Southworth chassis it made its debut at the Institute of Road Transport Engineers show at Telford in May this year.
CLEAN SHEET
The CD vehicle, plated at the slightly lower GVW of 19 tonnes, is not a conversion; it was designed from a clean sheet of paper. Its chassis longitudinals continue forward at low level (frame-top height is 825inm), the Perkins Phaser engine towering somewhat incongruously above the chassis when the cab is tilted.
Though the frame is not stepped, space under the crew compartment of the cab — borrowed from a Jack Allen Britannia refuse collection vehicle — is taken up by the unusual ZF WG150 automatic gearbox. It is the German transmission's first application in a road vehicle, but its "laddered" (vertically stepped down) gear train makes it ideal for obtaining the lowlevel output shaft demanded by the urban delivery application.