Custom building aids US transport economy
Page 42
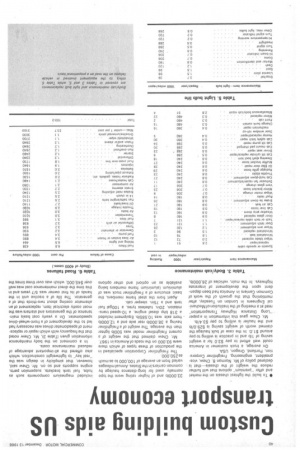
Page 43
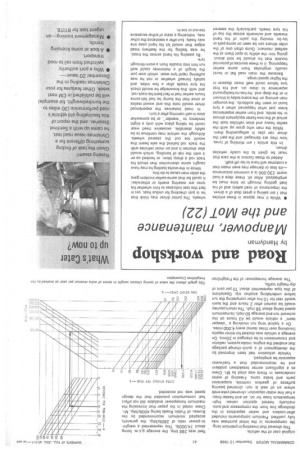
If you've noticed an error in this article please click here to report it so we can fix it.
• To build the lightest chassis on the market and offer "premium" options that will further reduce the weight of the chassis-that is declared policy of Mr. Norman B. Chew, vicepresident, engineering, Freightliner Corporation, Portland, Oregon, USA.
On average, a truck customer in America could well afford to pay $3.0 for a weight saving of llb and in practice is willing to pay around $1.0. In the case of bulk haulage the claimed worth of weight saving is $29.0/1b and the haulier is willing to pay $3.4/lb.
Mr. Chew gave this information in a paper "Long Distance Highway Transportation" read at a meeting of the Institution of Mechanical Engineers in Landon an Tuesday, after mentioning that the growth of the work of Common Carriers in America had been dependent upon the development of interstate highways. In the main, vehicles of 26,0001b, 33,000lb and of higher rating were the type normally used for long-distance haulage by common carriers in the States. Annual mileages varied from an average of 100.000 to as much as 250,000.
The Freightliner Corporation specialized in the production of these types of which there were 93,000 on the roads of America in 1967.
Mr. Chew claimed that the weight of a current Freightliner model was 5001b lighter than the average. The weight of a Freightliner having a 38,000lb rear axle and a 12,000lb front axle was 10,5851b. Equipment included a 318 bhp diesel engine, a 10-speed transmission, 20in. tubeless tyres, a 100gal fuel tank and a 75in. sleeper cab.
Apart from the steel frame members, the basic structure of a Freightliner truck was of aluminium (aluminium frame members being available as an option) and other options included magnesium components such as hubs, fuel tank brackets, suspension parts, engine supports and so on. Mr. Chew said, however, that simplicity in design was the "real key" to lightweight construction, which also offered the all-important advantage of reduced maintenance costs.
In a comment on the body maintenance information given (Table 3), Mr. Chew noted that the frequency with which repair or replacement of speedometer drives was necessary had led to the development of a front-wheel-drive speedometer. On a yearly cost basis maintenance of the generators and starters was the most costly electrical item, replacement of an alternator costing about two-thirds that of a generator. The life of a tractive unit in the hands of its first owner was 5/7 years and in this time the direct maintenance cost was well over $45,000, which was over three times the original cost of the vehicle.
This showed that investing in premium longlife components in the initial purchase was fully justified. Premium components included after-coolers and water separators in the discharge line from the compressor and automatically heated ejection valves; hightemperature hose for oil, air and heater lines: a fuel line water separator; chromed yoke ends where an oil seal is run; chromed bearing surfaces of gearbox controls, suspension parts and brake cams. Freezing of water condensate in filters was cited by Mr. Chew as a significant winter breakdown problem and he recommended that a fuel/water separator be employed.
Vehicle utilization had been improved by the development of a quick-change package that enabled the engine, intake system, radiator and transmission to be changed in 20min. On average a vehicle was docked for minor repairs (involving over three items) every 4,000 miles.
On a typical long run involving a "sleeper team" a vehicle would be 43 hours on the outward run and average 50 mph, its maximum speed being about 58 mph. The return journey would be started after 2 hours and the team would rest for 10 hrs after completing the run before undertaking another trip. Operations of this type represented about 70 per cent of dry-freight traffic.
The average horsepower of the Freightliner fleet was 288 bhp, the average g.c.w. being about 74,000lb. This represented a weightto-power ratio of 280lb/bhp, the generally accepted minimum recommended by the Bureau of Public Roads being 4001b/bhp. Mr. Chew noted in his paper that increasing the maximum horsepower available did not affect fuel consumption provided that the design speed was not exceeded.