road and workshop
Page 36
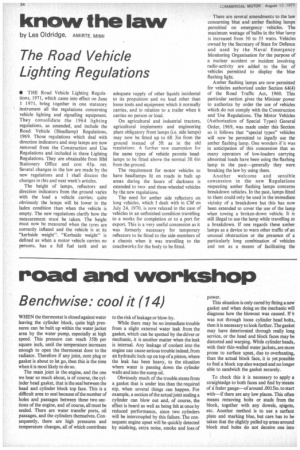
Page 37
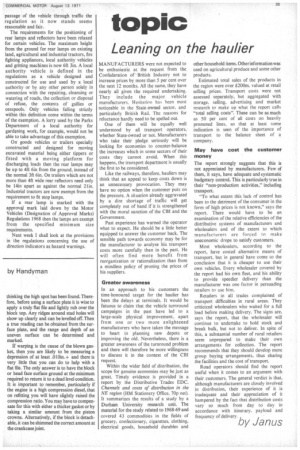
If you've noticed an error in this article please click here to report it so we can fix it.
by Handyman
Benchwise: cool it (14)
WHEN the thermostat is closed against water leaving the cylinder block, quite high pressures can be built up within the water jacket area by the water pump, especially at high speed. This pressure can reach 35Ib per square inch, until the temperature increases enough to open the thermostat door to the radiator. Therefore if any joint, core plug or gasket is about to let go, then this is the time when it is most likely to do so.
The main joint in the engine, and the one we hear so much about, is of course, the cylinder head gasket, that is the seal between the head and cylinder block top face. This is a difficult area to seal because of the number of holes and passages between these two sections of the engine, and of course, all must be sealed. There are water transfer ports, oil passages, and the cylinders themselves. Consequently, there are high pressures and temperature changes, all of which contribute to the risk of leakage or blow-by.
While there may be no immediate trouble from a slight external water leak from the gasket, which can be spotted by the driver or mechanic, it is another matter when the leak is internal. Any leakage of coolant into the engine can cause serious trouble indeed, from an hydraulic lock-up on top of a piston, where the leak has been heavy, to the situation where water is passing down the cylinder walls and into the sump oil.
Obviously much of the trouble stems from a gasket that is under less than the required nip, when several things can happen. For example, a section of the actual joint sealing a cylinder can blow out and, of course, the effect is heard as well as being felt at once by reduced performance, since two cylinders will be intercoupled by this failure. The consequent engine upset will be quickly detected by misfiring, extra noise, smoke and loss of power.
This situation is only cured by fitting a new gasket and when doing so the mechanic will diagnose how the blowout was caused. If it was not through loose cylinder head bolts, then it is necessary to look further. The gasket may have deteriorated through really long service, or the head and block faces may be distorted and warping. While cylinder heads, with their thin-walled water jackets, are more prone to surface upset, due to overheating, than the actual block face, it is yet possible to find a block top also warped and no longer able to sandwich the gasket securely.
To check this it is necessary to apply a straightedge to both faces and find by means of i feeler gauge of around .0015in. to start with—if there are any low places. This often means removing bolts or studs from the block, together with any dowels, spigots, etc. Another method is to use a surface plate and marking blue, but care has to be taken that the slightly pulled up areas around block stud holes do not deceive one into thinking the high spot has been found. Therefore, before using a surface plate it is wise to apply a truly flat file and lightly rub over the block top. Any ridges around stud holes will show up clearly and can be levelled off. Then a true reading can be obtained from the surface plate, and the range and depth of an uneven surface can be determined and marked.
If warping is the cause of the blown gasket, then you are likely to be measuring a depression of at least .010in. + and there is very little that you can do to help with a flat file. The only answer is to have the block or head face surface ground at the minimum required to return it to a dead level condition. It is important to remember, particularly if the engine is a high compression diesel, that on refitting you will have slightly raised the compression ratio. You may have to compensate for this with either a thicker gasket or by taking a similar amount from the piston crowns. Alternatively, if the block is detachable, it can be shimmed the correct amount at the crankcase joint.