Follow the system for trouble-free running
Page 24
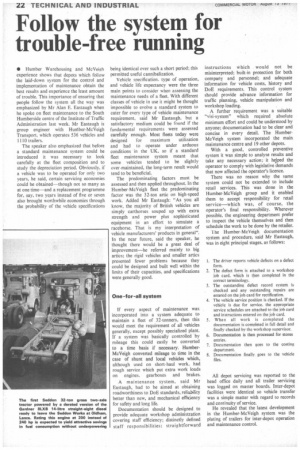
If you've noticed an error in this article please click here to report it so we can fix it.
• Humber Warehousing and McVeigh experience shows that depots which follow the laid-down system for the control and implementation of maintenance obtain the best results and experience the least amount of trouble. This importance of ensuring that people follow the system all the way was emphasized by Mr Alan E. Eastaugh when he spoke on fleet maintenance to the South Humberside centre of the Institute of Traffic Administration last week. Mr Eastaugh is group engineer with Huraber-McVeigh Transport. which operates 536 vehicles and 1110 trailers.
The speaker also emphasized that before a standard maintenance system could be introduced it was necessary to look carefully at the fleet composition and to study the depreciation period. Obviously, if a vehicle was to be operated for only two years, he said, certain servicing economies could be obtained—though not so many as at one time—and a replacement programme for, say, two years instead of five or seven also brought worthwhile economies through the probability of the vehicle specifications being identical over such a short period; this permitted useful cannibalization.
Vehicle specification, type of operation, and vehicle life expectancy were the three main points to consider when assessing the maintenance needs of a fleet. With different classes of vehicle in use it might be thought impossible CO evolve a standard system to cater for every type of vehicle maintenance requirement, said Mr Eastaugh. but a satisfactory medium could be found if the fundamental requirements were assessed carefully enough. Most fleets today were designed for maximum utilization and had to operate under arduous conditions in the UK, so if a standard fleet maintenance system meant that some vehicles tended to be slightly over-maintained, the long-term result would tend to be beneficial.
The predominating factors must be assessed and then applied throughout. In the Humber-McVeigh fleet the predominating factor was the 32-ton artic on high-speed work. Added Mr Eastaugh: "As you all know, the majority of British vehicles are simply carthorses souped up with extra strength and power plus sophisticated equipment in an effort to simulate a racehorse. That is my interpretation of vehicle manufacturers' products in general". In the near future, said the speaker. he thought there would be a great deal of improvement—he referred mainly to big artics; the rigid vehicles and smaller attics presented fewer problems because they could be designed and built well within the limits of their capacities, and specifications were generally good.
One-for-all system
If every aspect of maintenance was incorporated into a system adequate to maintain a fleet of 32-tonners, then this would meet the requirement of all vehicles generally, except possibly specialized plant. If a system was basically controlled by mileage this could easily be converted to a time basis if necessary. HumberMcVeigh converted mileage to time in the case of shunt and local vehicles which, although used on short-haul work, had rough service which put extra work loads on engines, gearboxes and brakes.
A maintenance system, said Mr Eastaugh, had to be aimed at obtaining roadworthiness to DoE standards, reliability better than new, and mechanical efficiency for safety and long life.
Documentation should be designed to provide adequate workshop administration covering staff efficiency: distinctly defined staff responsibilities: straightforward instructions which would not be misinterpreted; built-in protection for both company and personnel; and adequate information for vehicle costs, history and DoE requirements. This control system should provide advance information for traffic planning, vehicle manipulation and workshop loading.
A further requirement was a suitable "visi-system" which required absolute minimum effort and could be understood by anyone; documentation had to be clear and concise in every detail. The HumberMcVeigh system incorporated the main maintenance centre and 19 other depots.
With a good, controlled preventive system it was simple to analyse results and take any necessary action; it helped the operator to comply with legislative demands that now affected the operator's licence.
There was no reason why the same system could not be extended to include retail services. This was done in the Humber-McVeigh group and it enabled them to accept responsibility for retail service—which was, of course, the operator's final responsibility. Wherever possible, the engineering department prefer to inspect the vehicle themselves and then schedule the work to be done by the retailer.
"1 he Humber-McVeigh documentation system and procedure. said Mr Eastaugh, was in eight principal stages, as follows: 1. The driver reports vehicle defects on a defect form.
2. The defect form is attached to a workshop job card. which is then completed in the correct terminology.
3. The outstanding defect record system is checked and any outstanding repairs are entered on the job card for rectification.
4. The vehicle service position is checked. If the vehicle is due for service, the appropriate service schedules are attached to the job card and instructions entered on the job card.
5. When all work is completed the documentation is completed in full detail and finally checked by the workshop supervisor.
6. Documentation is then processed for stores entries.
7. Documentation then goes to the costing department.
8. Documentation finally, goes to the vehicle files.
All depot servicing was reported to the head office daily and all trailer servicing was logged on master boards. Inter-depot facilities were identical so vehicle transfer was a simple matter with regard to records and continuity of service.
He revealed that the latest development in the Humber-McVeigh system was the plating of trailers for inter-depot operation and maintenance control.