Icing the cake
Page 46
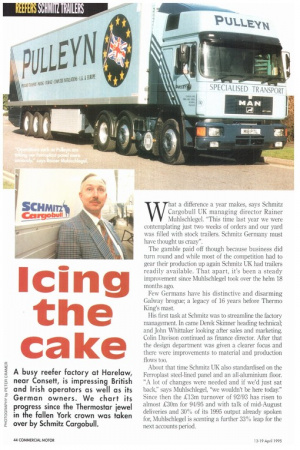
Page 47
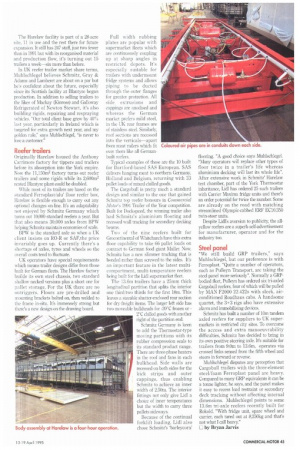
If you've noticed an error in this article please click here to report it so we can fix it.
A busy reefer factory at Harelaw, near Consett, is impressing British and Irish operators as well as its German owners. We chart its progress since the Thermostar jewel in the fallen York crown was taken over by Schmitz Cargobull.
hat a difference a year makes, says Schmitz Cargobull UK managing director Rainer Muhlschlegel. "This time last year we were contemplating just two weeks of orders and our yard was filled with stock trailers. Schmitz Germany must have thought us crazy".
The gamble paid off though because business did turn round and while most of the competition had to gear their production up again Schmitz UK had trailers readily available. That apart, it's been a steady improvement since Muhlschlegel took over the helm 18 months ago.
Few Germans have his distinctive and disarming Galway brogue; a legacy of 16 years before Thermo King's mast.
His first task at Schmitz was to streamline the factory management. In came Derek Skinner heading technical; and John Whittaker looking after sales and marketing. Colin Davison continued as finance director. After that the design department was given a clearer focus and there were improvements to material and production flows too.
About that time Schmitz UK also standardised on the Ferroplast steel-lined panel and an all-aluminium floor. "A lot of changes were needed and if we'd just sat back," says Muhlschlegel, "we wouldn't be here today" Since then the £13m turnover of 92/93 has risen to almost 30m for 94/95 and with talk of mid-August deliveries and 30% of its 1995 output already spoken for, Muhlschlegel is scenting a further 33% leap for the next accounts period.
The Harelaw facility is part of a 28-acre site, 11 in use and the rest there for future expansion. It still has 247 staff, just two fewer than in 1991 but with its reorganised material and production flow, it's turning out 15 trailers a week—six more than before.
In UK reefer trailer market share terms, Muhlschlegel believes Schmitz, Gray & Adams and Lamberet are about on a par but he's confident about the future, especially since its Scottish facility at Blantyre began production. In addition to selling trailers to the likes of Mackay (Kinross) and Galloway Refrigerated of Newton Stewart. it's also building rigids, repairing and respraying vehicles. ''Our total client base grew by 40% last year, particularly in Ireland which is targeted for extra growth next year, and my golden rule," says Muhlschlegel, "is never to lose a customer."
Reefer trailers Originally Harelaw housed the Anthony Carrimore factory for tippers and trailers before its absorption into the York empire. Now the 11,150m2 factory turns out reefer trailers and some rigids while its 2,600m2 rented Blantyre plant could be doubled.
While most of its trailers are based on the standard Ferroplastialu' floor reefer box. Harelaw is flexible enough to carry out any optional changes on-line. It's an adaptability not enjoyed by Schmitz Germany which turns out 10,000 standard reefers a year. But that also means 30,000 axles from BFW helping Schmitz maintain economies of scale.
BPW is the standard axle so when a UK client insists on RO-R or SAF,the price invariably goes up. Currently there's a shortage of axles, tyres and wheels so the overall costs tend to fluctuate.
UK operators have special requirements which means trailer designs differ from those built for German fleets. The Harelaw factory builds its own steel chassis, two standard shallow necked versions plus a short one for pallet storage. For the UK there are no outriggers. Floors are pre-drilled and mounting brackets bolted on, then welded to the frame in-situ. It's immensely strong but there's a new design on the drawing board. Full width rubbing plates are popular with supermarket fleets which are continuously coupling up at sharp angles in restricted depots. It's especially suitable for trailers with undermount fridge systems and allows piping to be ducted through the outer flanges for greater protection. All side extrusions and cappings are anodised and whereas the German market prefers mild steel, in the UK rear frames are of stainless steel. Similarly, roof sections are recessed into the verticals—apart from meat milers which fit over them like all Germanbuilt reefers.
Typical examples of these are the 10 built for Dartford.based SAS European. SAS delivers hanging meat to northern Germany, Holland and Belgium, returning with 33 pallet loads of mixed chilled goods.
The Cargobull is pretty much a standard design and similar to the one that gained Schmitz top reefer honours in Commercial Motor's 1994 Trailer of the Year competition. Built for Dockspeed, the winning trailer also had Schmitz's aluminium flooring and recessed wall tracking for secondary decking beams.
Two of the nine reefers built for Grocontinental of Whitchurch have this extra floor capability to take 66 pallet loads on contract to German food giant Muller. Now. Schmitz has a new slimmer tracking that is bonded rather than screwed to the sides. It's an important feature in the latest multicompartment, multi-temperature reefers being built for the Lidl supermarket fleet.
The 13.6m trailers have a 25mm thick longitudinal partition that splits the interior one third/two thirds for the first 10m. This leaves a sizeable shutter-enclosed rear section for dry-freight items. The larger left side has two moveable bulkheads for -20°C frozen or 2"C chilled goods with another right of the partition end.
Schmitz Germany is keen to add the Thermostar-type moving partitions with its rubber compression seals to its standard product range. There are three-phase heaters in the roof and fans in each bulkhead. Side walls are recessed on both sides for the kick strips and outer cappings, thus enabling Schmitz to achieve an inner width of 2.50m, The interior fittings not only give Lidl a choice of inner temperatures but the width to carry three pallets sideways.
Because of the continual forklift loading, Lidl also chose Schmitz's 'barleycorn' flooring. "A good choice says Muhlschlegel. "Many operators will replace other types of floor twice in a trailer's life whereas aluminium decking will last its whole life". After extensive work in Schmitz' Harelaw test chamber, part of the York Thermostar inheritance, Lidl has ordered 25 such trailers with Carrier Maxima fridge units and there's an order potential for twice the number. Some are already on the road with matching streamlined Olympic-cabbed ERF EC10.350 twin-steer units.
Despite Lid's aversion to publicity, the allyellow reefers are a superb self-advertisement for manufacturer, operator and for the indusuy too.
Steel panel
"We still build GRP trailers," says Muhlschlegel, but our preference is with Ferroplast. "Quite a number of operators, such as Pulleyn Transport, are taking the steel panel more seriously". Normally a GRPbodied fleet, Pulleyn has ordered six tri-axled Cargobull reefers, four of which will be pulled by MAN F2000 22.422s with sleek, airconditioned Roadhaus cabs. A handsome quartet, the 3+3 rigs also have extensive alarm and immobilising devices.
Schmitz has built a number of 10m tandem axled reefers for suppliers to UK supermarkets in restricted city sites. To overcome the access and extra manoeuvrability difficulties, Schmitz has decided to bring in its own positive steering axle. It's suitable for trailers from 9.0m to 13.6m, operates via crossed links sensed from the fifth wheel and steers in forward or reverse.
Muhlschlegel disputes any perception that Cargobull trailers with the three-element steel/foam Ferroplast panel are heavy. Compared to many GRP equivalents it can be a tonne lighter, he says, and the panel makes it easy to recess load restraint or secondary deck tracking without affecting internal dimensions. Muhlschlegel points to some 13.6m tri-axle reefers recently built for Rokold. "With fridge unit, spare wheel and carrier, each tared out at 8.250kg and that's not what I call heavy."
11 by Bryan Jarvis