TORQUEING FITHROUGII
Page 54
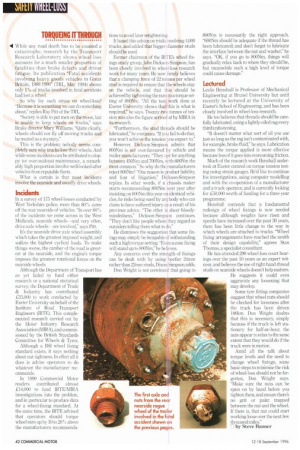
If you've noticed an error in this article please click here to report it so we can fix it.
11 While any road death has to be counted a catastrophe, research by the Transport Research Laboratory shows wheel-loss accounts for a much smaller proportion of fatalities than brake defects and driver fatigue. Its publication "Fatal accidents involving heavy goods vehicles in Great Britain, 1988-1990" (TRL, May 1994) shows only 1% of trucks involved in fatal accidents had lost a wheel.
So why lay such stress on wheel-loss? "Because it is something we can do something about," replies Ray Pitt of the TRL.
"Society is able to put men on the moon, but is unable to keep wheels on trucks," says Brake director Mary Williams. "Quite clearly. wheels should not fly off moving trucks and be treated as a mystery."
This is the problem; nobody seems completely sure why trucks lose their wheels. And while some incidents can he attributed to sloppy (or over-zealous) maintenance, a remarkably high proportion involve well-looked-after vehicles from reputable fleets.
What is certain is that most incidents involve the nearside and usually drive wheels.
Incidents
In a survey of 173 wheel-losses conducted by West Yorkshire police, more than 80% came off the rear nearside of vehicles. "In over 80% of the incidents we come across in the West Midlands. nearside wheels—and very often, drive-axle wheels—are involved," says Pitt.
It's the nearside drive axle wheel assembly which takes the greatest imposed weight, and suffers the highest cyclical loads. To make things worse, the camber of the road is greatest at the nearside, and the engine's torque imposes the greatest rotational forces on the nearside wheels.
Although the Department of Transport has as yet failed to fund either research or a national statistical survey, the Department of Trade & Industry has contributed £35,000 to work conducted by Exeter University on behalf of the Institute of Road Transport Engineers (IRTE). This complemented research carried out by the Motor Industry Research Association (MIRA), and commissioned by the British Standards Committee for Wheels & Tyres, Although a BSI wheel fixing standard exists, it says nothing about nut tightness. In effect all it does is advise operators to do whatever the manufacturer recommends.
In 1990 Commercial Motor readers contributed almost £14,000 to fund IRTE/MIRA investigations into the problem, and in particular to produce data for a wheel-fixing standard, At the same time, the IRTE advised that operators should torque wheel nuts up by 10 to 20".) above the manufacturers recommenda tions to avoid later retightening.
It based this advice on trials involving 4,000 trucks, and added that bigger-diameter studs should be used.
Former chairman of the IRTE's wheel fixings study group, John Dickson-Simpson, has been closely involved in wheel-loss research work for many years. He now firmly believes that a clamping force of 22 tonnes per wheel stud is required to ensure that the wheels stay on the vehicle, and that this should be achieved by tightening the nuts to a torque setting of 800Nm. "All the test work done at Exeter University shows thatithis is what is required," he says. Twenty-two tonnes of tension was also the figure arrived at by MIRA in its research.
"Furthermore, the stud threads should be lubricated," he continues. "lf you fail to do that, you won't achieve the tension you expect to."
However. Dickson-Simpson admits that 800Nnt is not over-favoured by vehicle and trailer manufacturers, "They opt for anything between 450Nm and 700Nm, with 600Nm the most common." So why do the manufacturers reject 800Nm? "One reason is product liability, and fear of litigation," Dickson-Simpson replies. In other words, if a chassis maker starts recommending 800Nm next year after insisting on 600Nm this year on identical vehicles, he risks being sued by anybody who can claim to have suffered injury as a result of his previous advice. "The other is sheer bloodymindedness," Dickson-Si mpsi m continues. "They don't like people whom they regard as outsiders telling them what to do."
Ile dismisses the suggestion that some fixings may simply be incapable of withstanding such a high torque setting. "Even a cone fixing will stand up to 800Nm," he believes.
Any concerns over the strength of fixings can be dealt with by using beefier 24inm rather than 22mm studs, Dixon-Simpson adds.
Don Wright is not convinced that going to 800Nm is necessarily the right approach. "600Nm should be adequate if the thread has been lubricated; and don't forget to lubricate the interface between the nut and washer," he says. "OK, if you go to 800Nm, things will gradually relax back to where they should be, but meanwhile such a high level of torque could cause damage."
Lectured
Leslie Henshall is Professor of Mechanical Engineering at Brunel University but until recently be lectured at the University of Exeter's School of Engineering, and has been closely involved in wheel-loss research.
He too believes that threads should be carefully lubricated, using a lightly-oiled rag every third unfastening.
"It doesn't matter what sort of oil you use just so long as the rag isn't contaminated with, for example, brake fluid," he says, Lubrication means the torque applied is more effective because less of it goes into overcoming friction.
Much of the research work lIenshall undertook at Exeter centred on torque tension testing using strain gauges. lied like to continue his investigations, using computer modelling and with the co-operation of a manufacturer and a truck operator, and is currently looking for £50,000 worth of funding for a three-year programme.
Henshall contends that a fundamental redesign of wheel fixings is now needed because although weights have risen and speeds have increased over the past 30 years, there has been little change to the way in which wheels are attached to trucks. "Wheel fixing arrangements have reached the zenith of their design capability," agrees Stan Thomas, a specialist consultant He has attended 290 wheel-loss court hearings over the past 10 years as an expert witness, and believes the use of right-hand-thread studs on nearside wheels doesn't help matters. He suggests it could even aggravate any loosening that may develop.
Some tyre fitting companies suggest that wheel nuts should be checked for looseness after the truck has been driven 100km. Don Wright doubts that this is necessary, simply because if the truck is left stationary for half-an-hour, the nuts appear to relax to the same extent that they would do if the truck were in motion.
Amid all the talk about torque levels and the need to change wheel fixings, some basic steps to minimise the risk of wheel-loss should not be forgotten, Don Wright says. "Make sure the nuts can be spun on by hand before you tighten them, and ensure there's no grit or paint trapped between the nut and the wheel. If there is, that nut could start working loose over the next few thousand miles."
fl by Steve Banner