. and It's Cheaper Not to Smoke
Page 57
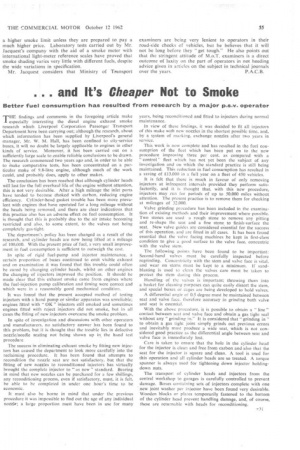
If you've noticed an error in this article please click here to report it so we can fix it.
Better fuel consumption has resulted from research by a major p.s.v. operator THE findings and comments in the foregoing article make especially interesting the diesel engine exhaust smoke research which Liverpool Corporation Passenger Transport Department have been carrying out; although the research, about which information has been supplied by -Liverpool's general manager, Mr. W. M. Hall, has been confined to city-service buses, it will no doubt be largely applicable to engines in other kinds of service. Moreover, it has been carried out on a sufficiently large scale to enable reliable conclusions to be drawn. The research commenced two years ago and, in order to be able to inake comparative tests, has been concentrated on a particular make of 9.8-litre engine, although much of the work could, and probably does, apply to other makes.
The conclusion has been reached that although cylinder heads will last for the full overhaul life of the engine without attention, this is not very desirable. After a high mileage the inlet ports have tended to become choked with carbon, reducing engine efficiency. Cylinder-head gasket trouble has been more prevalent with engines that have operated for a long mileage without the heads being removed, and there are clear indications that this practice also has an adverse effect on fuel consumption. It is thought that this is probably due to the air intake becoming restricted and also, to some extent, to the valves not being completely gas-tight.
The department's policy has been changed as a result of the research, and cylinder heads are now being lifted at a mileage of 100,000. With the present price of fuel, a very small improvement in fuel consumption is sufficient to outweigh the cost.
In spite of rigid fuel-pump and injector maintenance, a certain proportion of buses continued to emit visible exhaust and on examination it was found that this trouble could often be cured by changing cylinder heads, whilst on other engines the changing of injectors improved thc position. It should be made clear that this exhaust smoke came from engines where the fuel-injection pump calibration and timing were correct and which were in a reasonably good mechanical condition.
• It was found that the present accepted method of testing injectors with a hand pump or similar apparatus was unreliable; engines fitted with " OK " injectors still smoked and sometimes engines fitted with reject injectors did not smoke, but in all cases the fitting of new injectors overcame the smoke problem.
In spite of investigation and discussions with other operators and manufacturers, no satisfactory answer has been found to this problem, but it is thought that the trouble lies in defective nozzle/needle seating not being shown up in the hand test procedure.
The success in eliminating exhaust smoke by fitting new injectors has caused the department to look more carefully into the reclaiming procedure. It has been found that attempts to recondition the nozzle seat are not satisfactory, but that the fitting of new nozzles to reconditioned injectors has virtually brought the complete injector to "as new" standard. Bearing in mind that new nozzles can be purchased for a few shillings, any reconditioning process, even if satisfactory, must, it is felt, be able to be completed in under one hour's time to be economic.
It must also be borne in mind that under the previous procedure it was impossible to find out the age of any individual nozzlr; a large proportion must have been in use for many
years, being reconditioned and fitted to injectors during normal maintenance.
In view of these findings, it was decided to fit all injectors of this make with new nozzles in the shortest possible time, and, by a system of marking, exchange nozzles after two years in service.
This work is now complete and has resulted in the fuel consumption of the fleet which has been put on to the new procedure improving three per cent. as compared with a "control" fleet which has not yet been the subject of any investigation and on which the standard practice is still being maintained. This reduction in fuel consumption has resulted in a saving of £13,000 in a full year on a fleet of 450 vehicles.
It is felt that there is much in favour of only removing injectors at infrequent intervals provided they perform satisfactorily, and it is thought that, with this new procedure, injectors may run for periods of up to 50,000 miles without attention. The present practice is to remove them for checking at mileages of 32.000.
Valve grinding procedure has been included in the examination of existing methods and their improvement where possible. Two stones are used a rough stone to remove any pitting and re-shape the seat and a fine stone. to finish-surface the seat. New valve guides are considered essential for the success of this operation, and are fitted in all cases. It has been found essential that the valve facing machines be kept in first-class condition to give a good surface to the valve face, concentric with the valve stem.
The following points have been found to be importmt: Second-hand valves must be carefully inspected before regrinding. Concentricity with the stem and valve face is vital, and wear on stems must be kept to a minimum. If sandblasting is used to clean the valves care must be taken to protect the stem during this process.
Handling of the valves is important; throwing them into a basket for cleaning purposes can quite easily distort the stem, and special boxes or cages are being developed to hold valves.
A differential angle of 0,5 degree must be maintained between seat and valve face. therefore accuracy in grinding both valve and seat is essential.
With the above procedure, it is possible to obtain a " line " contact between scat and valve face and obtain a gas tight seal without any " grinding in." It is considered that " grinding in " to obtain a gas tight joint simply grinds out previous errors and inevitably must produce a wide seat, which is not considered good practice as the differential angle between seat and valve face is immediately lost.
Care is taken to ensure that the hole in the cylinder head for the injector is clean and free from carbon and also that the seat for the injector is square and clean. A tool is used for this operation and all cylinder heads are so treated. A torque spanner is always used for tightening down injector holdingdown nuts.
The transport of cylinder heads and injectors from the central workshop to garages is carefully controlled to prevent damage. Boxes containing sets of injectors .complete with one new joint washer per injector have been found very desirable. Wooden blocks or plates temporarily fastened to the bottom of the cylinder head prevent handling damage, and, of course, these are returnable with heads for reconditioning.