New Depot Designed for 250 Vehicles
Page 55
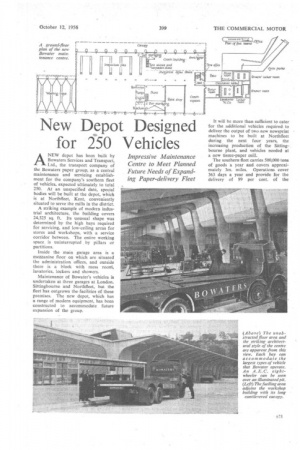
Page 56
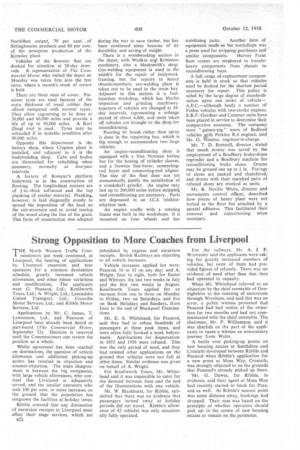
If you've noticed an error in this article please click here to report it so we can fix it.
Impressive Maintenance Centre to Meet Planned Future Needs of Expanding Paper-delivery Fleet
ANEW depot has been built by Bowaters Services and Transport, Ltd., the transport company of the Bowaters paper group,, as a central maintenance and servicing establishment for the company's southern fleet of vehicles, expected ultimately to total 250. At an unspecified date, special bodies will be built at the depot, which is at Northffeet, Kent, conveniently situated to serve the mills in the district.
A striking example of modern industrial architecture, the building covers 24,325 sq. ft. Its unusual shape was determined by the high bays required for servicing, and low-ceiling areas for stores and workshops, with a service corridor between. The entire working space is uninterrupted . by pillars or partitions.
Inside the main garage area is a mezzanine floor on which are situated the administration offices, and outside there is a block with mess roorri, lavatories, lockers and showers.
Maintenance of Bowater's vehicles is undertaken at three garages at London, Sittingbourne and Northfleet, but the fleet has outgrown the facilities of these premises. The new depot, which has a range of modern equipment, has been constructed to accommodate future expansion of the group. It will be more than sufficient to cater for the additional vehicles required to deliver the output of two new newsprint machines to be built at Northfleet during the next four years, the increasing production of the Sittingbourne plant, and vehicles needed at a new tissue-paper mill.
The southern fleet carries 500,000 tons of goods a year and covers approximately 3m. miles. Operations cover 363 days a year and provide for the delivery of 99 per cent, of the Northfleet output, 70 per cent. , of Sittingbourne products and 80 per cent. of the newsprint production of the Kemsiey plant.
Vehicles of the Bowater fleet are docked for attention at 28-day intervals. A' representative of The Commercial Motor who visited the depot on Monday was taken first into the tyre store, where a month's stock of covers is held.
There are three sizes of cover. Premium tyres are used because of the extra thickness of tread rubber they afford compared with normal types. They allow regrooving to be done at 30,000 and 60,000 miles and provide a life of up to 90,000 miles. A Karl Zangl tool is used. Tyres may be retreaded if in suitable condition after 90,000 miles.
Opposite this department is the battery shop, where Crypton plant is installed, and adjacent to it is the bodybuilding shop. Cabs and bodies are dismantled for rebuilding when necessary, normally at five-year intervals.
A feature of Bowater's platform bodywork is in the construction of flooring. The longitudinal runners are of 1-in.-thick softwood and the top planking of similar material. Planking, however, is laid diagonally evenly to spread the imposition of the load on the sub-structure and to avoid tearing of the wood along the line of the grain. This form of construction was adopted during the war to save timber, but has been continued since because of its durability and saving of weight.
There is a woodworking section in the depot, with Wadkin anjl Robinson machinery, also a blacksmith's shop. Gas-welding equipment is used in the srnith's for the repair of bodywork framing, but for repairs to heavy chassis-members, arc-welding plant is taken out to be used in the main bay. Adjacent to this section is a fuelinjection workshop, which has Merlin inspection and grinding machinery. Injectors of vehicles are changed at 56day intervals, representing a mileage period of about 4,000, and units taken off vehicles are brought to the shop for reconditioning.
Painting by brush rather than spray is done in the repainting bay, which is big enough to accommodate two large vehicles.
An engine-reconditioning shop is equipped with a Van Norman boring bar for the honing of cylinder sleeves, and a Newton line-borer, connectingrod borer and connecting-rod aligner. The size of the fleet does not yet economically justify the installation of a crankshaft grinder. An engine may last up to 200,000 miles before stripping and reconditioning are necessary, Parts are degreased in an IC!. trichlorethylene tank.
An engine cradle with a rotating frame was built in the workshops. It is mounted on four wheels and has stabilizing jacks. Another item of - equipment made-in the workshops was a press used for stripping gearboxes and
similar 'components. Harvey Frost floor cranes are employed to transfer heavy components from chassis to reconditioning bays.
A full range of=replacenaent components is held in stock so that vehicles need be docked for the shortest period necessary for repair. This policy is aided by the large degree of standardization upon one make of vehicleA.E.C.—although lately a number of Foden vehicles with two-stroke engines, E.R.F.-Gardner and Comrner units have been placed in service to determine their comparative economy. The company were " guinea-pig " users of Bedford vehicles xith Perkins R.6 engines, said Mr. G. Plimmo, engineer-in-charge.
Mr. T. D. Botterill, director, stated that much._ money was saved by the employment of a Bradbury brake-drum regrinder and a Bradbury machine for reconditioning brake shoes. Drums may be ground out up to in. Facings of shoes are packed and chamfered, and drums with their matched pairs of refaced shoes are stocked as units.
Mr. R. Neville White, director and movements control officer, described how pieces of heavy plant were not bolted to the floor but attached by a special adhesive. This facilitated their removal and repositioning when necessary.