A One-make Fleet Feeds
Page 41
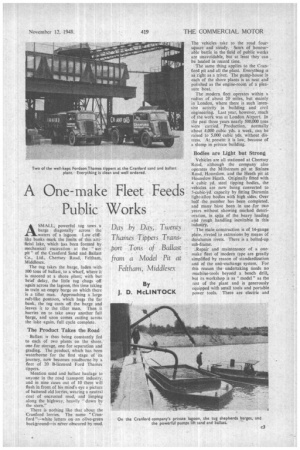
Page 42
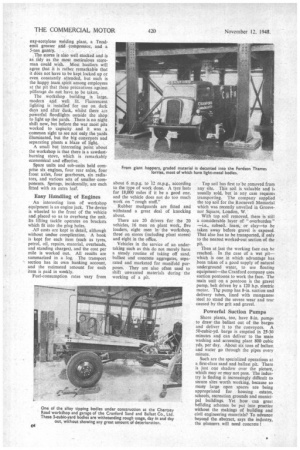
If you've noticed an error in this article please click here to report it so we can fix it.
Public Works
Day by Day,_ Twenty Thames Tippers Transport Tons of Ballast from a Model Pit at
Felthani, Middlesex
By J. D. McLINTOCK ASMALL, powerful tug tows a barge diagonally ' across the waters of a lagoon. .Low clifflike banks mark the limits of this artificial lake, which has been formed by mechanical excavation at the "wet pit" of the Cranford Sand and .Ballast Co., Ltd., Chertsey Road, Feltham. Middlesex.
The tug takes the barge, laden with 100 tons of ballast, to a wharf, where it is moored at a shore plant; with but brief delay, the little tug chugs off again across the lagoon, this time taking in train an empty barge on which there is a tiller man. Approaching a large raft-like pontoon, which hugs the far bank, the tug casts off the barge and leaves it to the tiller man. Then it hurries on to take away another full barge, and soon comes cutting across the lake again, full cycle complete.
The Product Takes the Road
Ballast is thus being constantly fed to each of two plants on the shore." one for storage, one for separation and grading. The product, which has been waterborne for the first stage of its journey, no's' becomes roadborne by a fleet of 20 B-licensed Ford Thames tippers.
Mention sand and ballast haulage to anyone in the road ttansport industry. and in nine eases out of 10 there will flash in front of his mind's eye a picture of battered old lorries, wearing a neutral coat of encrusted mud, and limping along the highway. heavily "down by the stern."
There is nothing like that about the Cranford lorries. The name "Cranford "—white letters on an olive-green background—is never obscured by mud. The vehicles take to the road foursquare and steady. Sears of honourable battle in the field of public works are unavoidable, but at least they can be healed in record time.
The same thing applies to the Cranford pit and all the plant. Everything is is right as a trivet. The pump-house in each of the shore plants is as neat and polished as the engine-room of a pleasure boat.
The modem fleet operates within a radius of about 20 miles, but mainly in London, where there is such.intensive activity in building and civil engineering. Last year, however, much of the work was at London Airport. In the past three years nearly 500.000 tons Were carried. Production, normally about 4.000 cubic yds. a week, can be raised to 5.000 cubic yds. without distress. At present it is low, because of a slump in private building.
Bodies are Light but Strong
Vehicles are all stationed at Chertsey Road, although the company also operates the Millstream pit at Staines Road. Hounslow, and the Heath pit at Hounslow Heath. Originally fitted with 4 cubic yd. steel tipping bodies, the vehicles are now being converted to 5-cubic-yd. capacity by fitting Duramin light-alloy bodies with high sides: Over half the number has been completed, and many have been in use for two years without showing marked deterioration, in spite of the heavy loading and rough handling inevitable in this industry.
The main construction is of 14-gauge plate, riveted to extrusions by means of doralumin rivets. There is a bolted-up sub-frame.
.Repair and maintenance of a onemake fleet of modern type are greatly simplified by reason of standardization and of the unit-exchange system. For this reason the undertaking needs no machine-tools beyond a bench drill, but its workshop is as " model" as the rest of the plant and is generously equipped with small tools and portable power tools. There are electric and oxy-acetylene welding plant, a Tecalemit greaser and compressor, and a 5-ton gantry. .
The stores is also well stocked and is as tidy as the most meticulous storeman could wish. Most hauliers will agree that it is rather remarkable that it dins not have to be kept locked up or even constantly attended, but such is the happy team spirit among employees at the pit that these precautions against pilferage do not have to be taken.
The workshop building is large, modern and' well lit. Fluorescent lighting is installed for use on dark days and after dusk, whilst there are powerful floodlights outside the shop to light up the yards. There is no night shift now, but before the war most pits worked to 'capacity and it was a common sight to see not only the yards illuminated, but the big conveyors and separating plants a blaze of light.
A small but interesting point about the workshop is that there is a sawdustburning stove, which is remarkably economical and effective.
Spare units and sub-units held comprise six engines, four rear axles, four front axles, four gearboxes, six radiators, and various sets of smaller components. Springs, incidentally, are each fitted with an extra leaf.
Easy Handling of Engines
An interesting item of workshop equipment is an engine jack. The device is wheeled to the front of the vehicle and placed so as to overhang the unit. Its lifting tackle operates on brackets which fit into the plug holes.
All costs are kept in detail, although without undue complication. A hook is kept for each item (such as tyres, petrol, oil, repairs, material, overheads, and standing charges), and the cost per mile is worked out. All results are summarized in a log. The transport section has its own banking account, and the estimated amount for each item is paid in weekly.
Fuel-consumption rates vary from
about 6 m.p.g. to 12 m.p.g., according to the type of work done. A tyre lasts for 18,000 miles if it be a good one, and the vehicle does not do too much work on "rough stuff."
Rubber mudguards are fitted and withstand a great deal of knocking about.
There are 20 drivers for the 20 vehicles, 16 men on plant work, five loaders, eight men in the workshop, three on stores (including plant stores) and eight in the office.
Vehicles in the service of an undertaking such as this do not merely have a steady routine of taking off sand, ballast and concrete aggregates, separated and marketed for manifold purposes. They are also often used to shift unwanted materials during the working of a pit. Top soil has first to'be removed from any site. This soil is valuable and is usually sold, but in any case requires transporting. The company supplied the top soil for the Roosevelt Memorial which was recently unveiled in Grosvenor Square, London, W.
With top soil removed, there is still a considerable layer of "overburden" —i.e., subsoil. loam, or clay—to be taken away before gravel is exposed. That also has to be transported, if only to the nearest worked-out section of the pit.
Then at last the working face can be reached. In the case of a wet pit— which is one in which advantage has been taken of a good supply of natural underground water, to use floating equipment—the Cranford company uses suction pontoons to work the face. The main unit on a pontoon is the gravel pump, belt driven by a 120 h.p. electric motor. Thg pump has 8-in, suction and delivery tubes, lined with manganese steel to stand the severe wear and tear caused by the grit and gravel.
Powerful Suction Pumps
Shore plants, too, have 8-in, pumps to draw the ballast out of the barges and deliver it to the conveyors. A 50-cubic-yd. barge is emptied in 25-30 minutes and can deliver to the main washing and screening plant 800 cubic yds. per day. About six tons of ballast and water go through the pipes every minute.
Such are the specialized operations at a first-class sand and ballast pit. There is just one shadow over the picture, which may or may not pass. The industry is finding it increasingly difficult to secure sites worth working, because so many large open spaces are being appropriated for housing estates. schools, recreation grounds and municipal buildings. Yet how can great building schemes be put into practice without the makings of building and civil engineering materials? To advance beyond the abstract, says the industry, the planners will need concrete