The conservative approach of manufacturers — 'We've always done it
Page 30
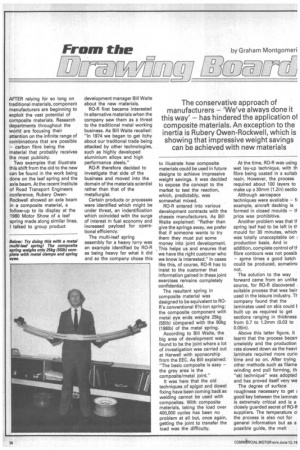
Page 31
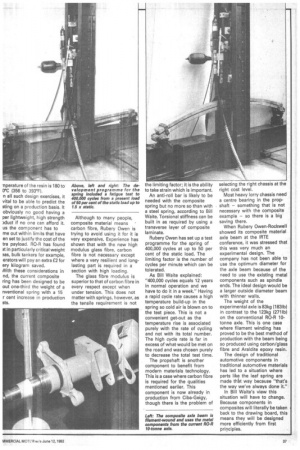
If you've noticed an error in this article please click here to report it so we can fix it.
this way' — has hindered the application oi composite materials. An exception to the inertia is Rubery Owen-Rockwell, which is showing that impressive weight savings can be achieved with new materials
AFTER relying for so long on traditional materials, component manufacturers are beginning to exploit the vast potential of composite materials. Research departments throughout the world are focusing their attention on the infinite range of combinations that are possible — carbon fibre being the material that probably receives the most publicity.
Two examples that illustrate this shift from the old to the new can be found in the work being done on the leaf spring and the axle beam. At the recent Institute of Road Transport Engineers conference, Rubery OwenRockwell showed an axle beam in a composite material, a follow-up to its display at the 1980 Motor Show of a leaf spring made along similar lines. I talked to group product development manager Bill Waite about the new materials.
RO-R first became interested in alternative materials when the company saw them as a threat to the traditional metal working business. As Bill Waite recalled: "In 1974 we began to get itchy about our traditonal trade being attacked by other technologies, such as highly developed aluminium alloys and high performance steels."
RO-R therefore decided to investigate that side of the business and moved into the domain of the materials scientist rather than that of the metallurgist.
Certain products or processes were identified which might be under threat, an indentification which coincided with the surge of interest in fuel economy and increased payload for operational efficiency.
The multi-leaf spring assembly for a heavy lorry was an example identified by RO-R as being heavy for what it did and so the company chose this to illustrate how composite materials could be used in future designs to achieve impressive weight savings. It was decided to expose the concept to the market to test the reaction, which, predictably, was somewhat mixed.
RO-R entered into various development contracts with the chassis manufacturers. As Bill Waite explained: "Rather than give the springs away, we prefer that if someone wants to try them they must put some money into joint development. This helps us and ensures that we have the right customer who we know is interested." In cases like this, of course, RO-R has to insist to the customer that information gained in these joint exercises remains completely confidential.
The resultant spring in composite material was designed to be equivalent to ROR's conventional 61/2-ton spring: the composite component with metal eye ends weighs 25kg (551b) compared with the 90kg (1981b) of the metal spring.
According to Bill Waite, the big area of development was found to be the joint where a lot of investigation was carried out at Harwell with sponsorship from the EEC. As Bill explained: "The basic composite is easy — the grey area is the composite/metal joint."
It was here that the old techniques of spigot and dowel fixing have been coming back as welding cannot be used with composites. With composite materials, taking the load over 400,000 cycles has been no problem at all but, once again, getting the joint to transfer the load was the difficulty. At the time, RO-R was using wet lay-up technique, with th fibre being coated in a suitab resin. However, the process required about 100 layers to make up a 30mm (1.21n) sectio Although aerospace techniques were available — fc example, aircraft decking is formed in closed moulds — tt price was prohibitive.
Another problem was that th spring leaf had to be left in if mould for 30 minutes, which was totally unacceptable on production basis. And in addition, complete control of th fibre contours was not possib — some times a good batch could be produced, sometirm not.
The solution to the way forward came from an unlike source, for RO-R discovered suitable process that was beir used in the leisure industry. Tt. company found that the laminates used on skis could t built up as required to get sections ranging in thickness from 0.7 to 1.2mm (0.03 to 0.051n).
Above this latter figure, it learnt that the process becarr unwieldy and the production rate slowed down as the heavi laminate required more curin time and so on. After trying other methods such as filame winding and pull forming, th "ski technique" was adopted and has proved itself very we The degree of surface roughness necessary to get good key between the laminati is extremely critical and is a closely guarded secret of RO-R suppliers. The temperature a the process is also not for general information but as a possible guide, the melt
nperature of the resin is 180 to 0°C (356 to 393°F).
n all such design exercises, it vital to be able to predict the sting on a production basis. It obviously no good having a per lightweight, high strength 3duct if no one can afford it. us the component has to me out within limits that have en set to justify the cost of the tra payload. RO-R has found A in particularly critical weight ?.as, bulk tankers for example, erators will pay an extra £2 for ery kilogram saved.
Nith these considerations in nd, the current composite ring has been designed to be out one-third the weight of a nventional spring with a 15 r cent increase in production sts.
Although to many people, composite material means • carbon fibre, Rubery Owen is trying to avoid using it for it is very expensive. Experience has shown that with the new high modulus glass fibre, carbon fibre is not necessary except where a very resilient and longlasting part is required in a section with high loading.
The glass fibre modulus is superior to that of carbon fibre in every respect except when under tension. This does not matter with springs, however, as the tensile requirement is not the limiting factor; it is the ability to take strain which is important.
An anti-roll bar is likely to be needed with the composite spring but no more so than with a steel spring, according to Bill Waite. Torsional stiffness can be built in as required by using a transverse layer of composite laminate.
Rubery Owen has set up a test programme for the spring of 400,000 cycles at up to 50 per cent of the static load. The limiting factor is the number of cycles per minute which can be tolerated.
As Bill Waite explained: "400,000 cycles equals 12 years in normal operation and we have to do it in a week." Having a rapid cycle rate causes a high temperature build-up in the spring so cold air is blown on to the test piece. This is not a convenient get-out as the temperature rise is associated purely with the rate of cycling and not with its total number. The high cycle rate is far in excess of what-would be met on the road and was chosen purely to decrease the total test time.
The propshaft is another component to benefit from modern materials technology. This is a case where carbon fibre is required for the qualities mentioned earlier. This component is now already in production from Ciba-Geigy, though there is the problem of selecting the right chassis at the right cost level.
Most heavy lorry chassis need a centre bearing in the propshaft — something that is not necessary with the composite example — so there is a big saving there.
When Rubery Owen-Rockwell showed its composite material axle beam at the 1RTE conference, it was stressed that this was very much an experimental design. The company has not been able to use the optimum diameter for the axle beam because of the need to use the existing metal components such as spindle ends. The ideal design would be a larger outside diameter beam with thinner walls.
The weight of the experimental axle is 83kg (1831b) in contrast to the 123kg (2711b) on the conventional RO-R 10tonne axle. This is one case where filament winding has proved to be the best method of production with the beam being so produced using carbon/glass fibre and Araldite epoxy resin. The design of traditional automotive components in traditional automotive materials has led to a situation where parts like the leaf spring are made thbt way because "that's the way we've always done it." In Bill Waite's view this situation will have to change. Because components in composites will literally be taken back to the drawing board, this means they will be designed more efficiently from first principles.