INDEPENDENT HEATING
Page 62
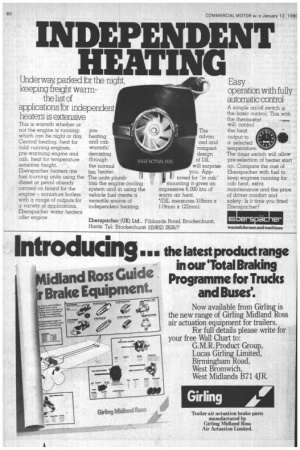
Page 63
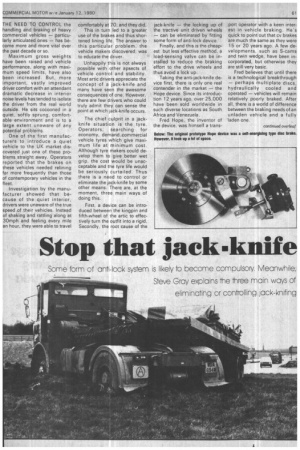
Page 64
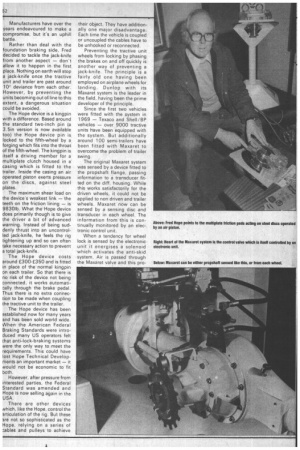
Page 65
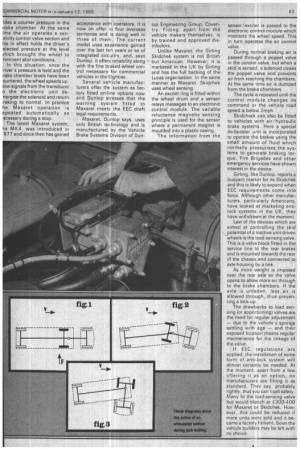
If you've noticed an error in this article please click here to report it so we can fix it.
This is warmth whether or not the engine is running: which can be night or day. Central heating, heat for cold running engines, pre-warming engine and cab, heat for temperature sensitive freight. Eberspacher heaters are fuel burning units using the diesel or petrol already carried on board for the engine miniature boilers with a range of outputs for a variety of applications. Eberspacher water heaters offer engine preheating and cab warmth/ demisting through the normal fan heater. The units plumb into the engine cooling system and in using the vehicle fuel create a versatile source of independent heating. The advan ced and compact design of DIL will surprise you. Approved for "in cab" mounting it gives an impressive 6,000 btu of warm air heat.
*(DIL measures 318mm x 119mm x 122mm).
Easy operation with fully automatic control
A simple on/off switch is the basic control. This with the thermostat will control the heat output to a selected temperature. The timer switch will allow pre-selection of heater start up. Compare the cost of Eberspacher with fuel to keep engines running for cab heat, extra maintenance and the price of driver comfort and safety. Is it time you fitted Eberspacher?
o
THE NEED TO CONTROL the handling and braking of heavy commercial vehicles — particularly articulated ones — has become more and more vital over the past decade or so.
Maximum gross weights have been raised and vehicle performance, along with maximum speed limits, have also been increased. But, more important, vastly improved driver comfort with an attendant dramatic decrease in interior noise levels has tended to isolate the driver from the real World outside. He sits cocooned in a quiet, softly sprung, comfortable environment and is to a large extent unaware of any potential problems One of the first manufacturers to introduce a quiet vehicle to the UK market discovered just one of these problems straight away. Operators reported that the brakes on these vehicles needed relining far more frequently than those of contemporary vehicles in the fleet.
Investigation by the manufacturer showed that because of the quiet interior, drivers were unaware of the true speed of their vehicles. Instead of shaking and rattling along at 30mph and feeling every mile an hour, they were able to travel comfortably at 70, and they did.
This in turn led to a greater use of the brakes and thus shortened lining life. The answer to this particular problem, the vehicle makers discovered, was to educate the driver.
Unhappily this is not always possible with other apsects of vehicle control and stability. Most artic drivers appreciate the concept of a jack-knife and many have seen the awesome consequences of one. However, there are few drivers who could truly admit they can sense the point at which jack-knife occurs.
The chief culprit in a jackknife situation is the tyre. Operators, searching for economy, demand commercial vehicle tyres which give maximum life at minimum cost. Although tyre makers could develop them to give better wet grip, the cost would be unacceptable and the tyre life would be seriously curtailed. Thus there is a need to control or eliminate the jack-knife by some other means. There are, at the moment, three main ways of doing this.
First, a device can be introduced between the kingpin and fifth-wheel of the artic to effectively turn the outfit into a rigid. Secondly, the root cause of the jack-knife — the locking up of the tractive unit driven wheels — can be eliminated by fitting some form of anti-lock device.
Finally, and this is the cheapest but less effective method, a load-sensing valve can be installed to reduce the braking effort to the drive wheels and thus avoid a lock up.
Taking the anti-jack-knife device first, there is only one real contender in the market — the Hope device. Since its introduction 12 years ago, over 25,000 have been sold worldwide in such diverse locations as South Africa and Venezuela.
Fred Hope,. the inventor of the device, was himself a trans
port operator with a keen interest in vehicle braking. He's quick to point out that cv brakes aremuch the same as they were 15 or 20 years ago. A few developments, such as S-cams and twin wedge, have been incorporated, but otherwise they are still very basic.
Fred believes that until there is a technological breakthrough — perhaps multi plate discs, hydraulically cooled and operated — vehicles will remain relatively poorly braked. After all, there is a world of difference between the braking needs of an unladen vehicle and a fully 'laden one. Manufacturers have over the years endeavoured to make a compromise, but its an uphill battle.
Rather than deal with the foundation braking side, Fred decided to tackle the jack-knife from another aspect — don't allow it to happen in the first place. Nothing on earth will stop a jack-knife once the tractive unit and trailer are past around 1 deviance from each other. However, by preventing the units becoming out of line to this extent, a dangerous situation could be avoided.
The Hope device is a kingpin with a difference. Based around the standard two-inch pin (a 3.5in version is now available too) the Hope device pin is locked to the fifth-wheel by a forging which fits into the throat of the fifth-wheel. The kingpin is itself a driving member for a multiplate clutch housed in a casing which is fitted to the trailer. Inside the casing an air operated piston exerts pressure on the discs, against steel plates.
The maximum shear load on the device's weakest link — the teeth on the friction lining — is 9830Ib. What the Hope device does primarily though is to give the driver a bit of advanced warning. Instead of being suddenly thrust into an uncontrolled jack-knife, he feels the rig tightening up and so can often take necessary action to prevent a total jack-knife.
The Hope device costs around £300-£350 and is fitted in place of the normal kingpin on each trailer. So that there is no risk of the device not being connected, it works automatically through the brake pedal. Thus there is no extra connection to be made when coupling the tractive unit to the trailer.
The Hope device has been established now for many years and has been sold world wide. VVhen the American Federal Braking Standards were introduced many US operators felt that anti-lock-braking systems were the only way to meet the requirements. This could have lost Hope Technical Developments an important market — it would not be economic to fit both.
However, after pressure from interested parties, the Federal Standard was amended and Hope iS now selling again in the USA.
There are other devices which, like the Hope, control the articulation of the rig. But these re not so sophisticated as the Hope, relying on a series of cables and pulleys to achieve their object. They have additionally one major disadvantage. Each time the vehicle is coupled or uncoupled the cables have to be unhooked or reconnected.
Preventing the tractive unit wheels from locking by phasing the brakes on and off quickly is another way of preventing a lack-knife. The principle is a fairly old one having been employed on airplane wheels for landing. Dunlop with its Maxaret system is the leader in the field, having been the prime developer of the principle.
Since the first two vehicles were fitted with the system in 1 969 — Texaco and Shell / BP vehicles — over 9000 tractive units have been equipped with the system. But additionally around 100 semi-trailers have been fitted with Maxaret to overcome the problem of trailer SW ing.
The original Maxaret system was sensed by a device fitted to the propshaft flange, passing information to a transducer fitted on the diff. housing. While this works satisfactorily for the driven wheels, it could not be applied to non driven and trailer wheels. Maxaret now can be sensed by a sensing disc and transducer in each wheel. The information from this is continually monitored by an electronic control unit.
When a tendency for wheel lock is sensed by the electronic unit it energises a solenoid which activates the anti-skid system. Air is passed through the Maxaret valve and this pro
'ides a counter pressure in the 'rake chamber. At the same ime the air operates a senitivity control valve section and his in effect holds the driver's elected pressure at the level vhich brought the wheel to -nminent skid conditions.
In this situation, once the Iriver's pressure is held and the ,rake chamber levels have been ountered, the wheel speeds up. Jaw signals from the transducer o the electronic unit denergise the solenoid and return ,raking to normal. In practice he Maxaret operation is epeated automatically as ecessary during a stop.
The latest Maxaret system, he MK 4, was introduced in 977 and since then has gained acceptance with operators. It is now on offer in four overseas territories and is doing well in three of them. The current model uses experience gained over the last ten years or so of .integrated circuitry, and, says Dunlop, it offers reliability along with the fine braked wheel control necessary for commercial vehicles in the Eighties.
Several vehicle manufacturers offer the system as factory fitted on-line options now and Dunlop stresses that the warning system fitted to Maxaret meets the EEC draft legal requirements.
Maxaret, Dunlop says, uses only British technology and is manufactured by the Vehicle Brake Systems Division of Dun
lop Engineering Group, Coventry. Fitting, apart from the vehicle makers themselves, is by trained and approved distributors.
Unlike Maxaret, the Girling Skidchek system is not British but American. However, it is marketed in the UK by Girling and has the full backing of the Lucas organisation. In the same manner as Maxaret, Skidchek uses wheel sensing.
An exciter ring is fitted within the wheel drum and a sensor relays messages to an electronic control module. The variable reluctance magnetic sensing principle is used for the sensor where a permanent magnet is moulded into a plastic casing.
The information from the sensor/exciter is passed to the electronic control module which monitors the wheel speed. This in turn operates the air control valve.
During normal braking air is passed through a poppet valve in the corttrol valve, but when a skid is sensed, a solenoid closes the poppet valve and prevents air from reaching the chambers. At the same time air is dumped from the brake chambers.
The cycle is repeated until the control module changes its command or the vehicle road speed is below 2mph.
Skidcheck can also be fitted to vehicles with air/hydraulic brake systems. Here a special de-booster unit is incorporated to operate the brakes using the small amount of fluid which normally pressurises the systems to generate braking torque. Fire Brigades and other emergency services have shown interest in the device.
Girling, like Dunlop, reports a buoyant market for its Skidchek and this is likely to expand when EEC requirements come into force. Although other manufacturers, particularly Americans, have looked at marketing antilock systems in the UK, they have withdrawn at the moment.
Last of the devices which are aimed at controlling the skid \ potential of a tractive unit driven
-wheels is the load-sensing valve.
This is a valve block fitted in the service line to the rear brakes and is mounted towards the rear of the chassis and connected to axle housing by a link.
As more weight is imposed over the rear axle so the valve opens to allow more air through to the brake chambers, if the axle is unladen, less air is allowed through, thus preventing a lock-up.
The drawbacks to load sensing (or apportioning) valves are the need for regular adjustment -due to the vehicle's springs settling with age — and their exposed location means regular maintenance for the linkage of the valve.
If EEC regulations are applied, the installation of some form. of anti-lock system will almost certainly be needed. At the moment, apart from a few offering it as an option, no manufacturers are fitting it as standard. They say, probably rightly, that you can't sell safety. Many fit the load-sensing valve but would blanch at £300-400 for Maxaret or Skidchek. However, this could be reduced if more units were sold and it became a factory fitment. Soon the vehicle builders may be left with no choice