Tread carefully on tyre choice
Page 43
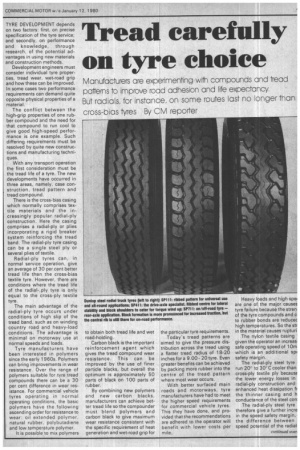
Page 44
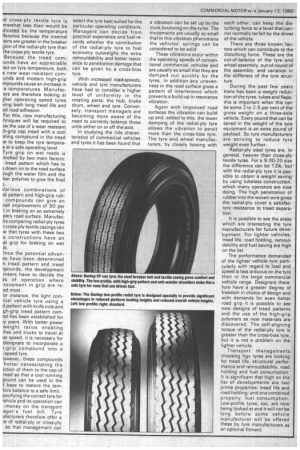
Page 45
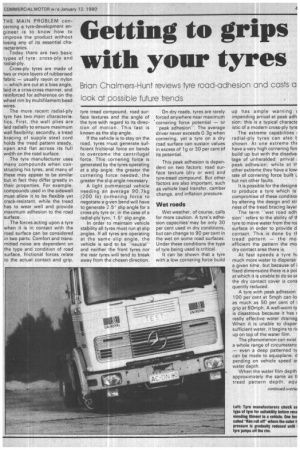
If you've noticed an error in this article please click here to report it so we can fix it.
TYRE DEVELOPMENT depends on two factors: first, on precise specification of the tyre service; and secondly, on performance and knowledge, through research, of the potential advantages in using new materials and construction methods.
Development engineers must consider individual tyre properties, tread wear, wet-road grip and how these can be improved. In some cases two performance requirements can demand quite opposite physical properties of a material.
The conflict between the high-grip properties of one rubber compound and the need for that compound to run cool to give good highspeed performance is one example. Such differing requirements must be resolved by quite new constructions and manufacturing techniques.
With any transport operation the first consideration must be the tread life of a tyre. The new developments have occurred in three areas, namely, case construction, tread pattern and tread compound.
There is the cross-bias casing which normally comprises textile materials and the increasingly popular radial-ply construction. Here the casing comprises a radial-ply or plies incorporating a rigid breaker system reinforcing the tread band. The radial-ply tyre casing can be a single steel ply or several plies of textile.
Radial-ply tyres can, in normal service operation, give an average of 30 per cent better tread life than the cross-bias textile tyre. However, there are conditions where the tread life of the radial-, ply tyre is only equal to the cross-ply textile tyre.
The main advantage of the radial-ply tyre occurs under conditions of high slip of the tread band, such as on winding country road and heavy-load . conditions. The advantage is minimal on motorway use at normal speeds and loads.
Tyre manufacturers have been interested in polymers since the early 1960s. Polymers can bring improvements in wear resistance. Over the range of polymers suitable for tyre tread compounds there can be a 30 per cent difference in wear resistance. For commercial vehicle tyres operating in normal operating conditions, the basic polymers have the following ascending order for resistance to wear: oil extended polymer, natural rubber, polybutadiene and low temperature polymer.
It is possible to mix polymers
to obtain both tread life and wet road-holding.
Carbon black is the important reinforcement agent which gives the tread compound wear resistance. This can be improved by the use of finer particle blacks, but overall the optimum is approximately 50 parts of black on 100 parts of rubber.
By combining new polymers and new carbon blacks, manufacturers can achieve better tread life so the compounder must bland polymers and carbon black to give maximum wear resistance consistent with the specific requirement of heat generation and wet-road grip for the particular tyre requirements.
Today's tread patterns are aimed to give the pressure distribution across the tread using a flatter tread radius of 18-20 inches for a 9.00-20 tyre. Even greater benefits can be achieved by packing more rubber into the centre of the tread pattern where most wear occurs.
With better surfaced main roads and motorways, tyre manufacturers have had to meet the higher speed requirements for commercial vehicle tyres. This they have done, and provided that the recommendations are adhered to the operator will benefit with lower costs per mile. Heavy loads and high sped are one of the major causes tyre failure because the stren, of the tyre compounds and c. to rubber bonds are reducec high temperatures. So the str in the material causes rupturi The nylon textile casing ' given the operator an increas, safe operating speed of lOrn which is an additional spd safety margin.
The radial-ply steel tyre run 20 to 30'C cooler than cross-ply textile ply becaus€ the lower energy losses in radial-ply construction and enhanced heat dissipation fr the thinner casing and h conductance of the steel con The radial-ply steel tyre therefore give a further incre in the speed safety margin, the difference between speed potential of the radial
id cross-ply textile tyre is mewhat less than would be dicated by the temperature fference because the internal -ains are greater in the breaker gion of the radial-ply tyre than the cross-ply textile tyre.
Because the tread corniunds have an appreciable ect on tyre temperature, both e new wear-resistant cornunds and modern high-grip mpounds cause an increase in -e temperatures. Manufac.ers are therefore looking at 3her operating speed tyres ving both long tread life and od road adhesion.
For this, new manufacturing :hniques will be required to )w the use of a wear resistant ih-grip cap tread with a cool ming compound in the tread le to keep the tyre temperae at a safe operating level. Tyre grip on wet roads is trolled by two main factors: tread pattern which has to down on to the road surface Dugh the water film and the .ber polymer to give the final ).
Various combinations of ]d pattern and high-grip rub. compounds can give an Tall improvement of 50 per t in braking on an extremely pery road surface. Manufac.irs comparing radial-ply tyres 1 cross-ply textile casings can w that tyres with these two e constructions have an al grip for braking on wet Js.
Dnce the potential advanes have been determined n tread pattern and tread tpounds, the .development ineers have to decide the as of operation where irovement in grip are reed most.
or instance, the light corncial vehicle tyre using a d pattern with knife cuts and gh-grip tread pattern comnd has been established for ly years. With better power weight ratios enabling ;hes and trucks to travel at ier speed, it is necessary for designers to incorporate a 1-grip compound into a -speed tyre.
owever, these compounds hotter necessitating the iction of them to the cap of :read so that a cool running pound can be used in the I base to restore the ternture balance to a safe limit. pecifying the correct tyre for 'chicle and its operation can money on the transport ager's fuel bill. Tyre ufacturers therefore offer a of radial-ply or cross-ply so that management can select the tyre best suited for the particular operating conditions. Managers can decide from practical experience and fuel records whether the contribution of the radial-ply tyre to fuel economy outweighs the extra remouldability and better resistance to penetration damage that can be given by a cross-bias tyre.
With increased road-speeds, vehicle and tyre manufacturers have had to consider a higher level of uniformity in the rotating parts: the hub, brake drum, wheel and tyre. Conversely, transport managers are becoming more aware of the need to correctly balance those units either on or off the axle.
In studying the ride characteristics of commercial vehicles and tyres it has been found that a vibration can be set up by the truck bouncing on the tyres. The movements are usually so small that in this vibration phenomena the vehicles springs can be considered to be solid.
These vibrations occur within the operating speeds of conventional commercial vehicles and are usually so small that they are damped out quickly by the tyres. In addition any unevenness in the road surface gives a pattern of interference which prevents a build-up in resonance vibration.
Again with improved road surfaces the vibration can build up and, added to this, the lower damping of the radial-ply tyre allows the vibration to persit more than the cross-bias tyre. The tyre and wheel manufacturers, by closely liaising with each other, can keep the disturbing force to a level that cannot normally be felt by the driver of the vehicle.
There are three known factors which can contribute to the disturbing force. These are the out-of-balance of the tyre and wheel assembly, out-of-round of the assembly; and variation in.. the stiffeners of the tyre structure.
During the past few years there has been a weight reduction of the tyres, tubes and flaps; this is important when this can be some 2 to 2.5 per cent of the gross weight on a three-axle vehicle. Every pound that can be saved in the weight of the tyre equipment is an extra pound of payload. So tyre manufacturers are striving to reduce tyre weight even further.
Radial-ply steel tyres are, in general, heavier than cross-ply textile tyres. For a 9.00-20 size the difference can be 1 21b, but with the radial-ply tyre it is possible to obtain a weight saving by using tubeless construction, which many operators are now doing. The high penetration of rubber into the woven wire gives the radial-ply cover a satisfactory resistance to tread separation.
It is possible to see the areas which are interesting the tyre manufacturers for future development. For lighter vehicles, tread life, road holding, remouldability and fuel saving are high on the list.
The performance demanded of the lighter vehicle tyre particularly with regard to load and speed is less arduous on the tyre than in the large commercial vehicle range. Designers therefore have a greater degree of freedom in choice of design and with demands for even better road grip it is possible to see new designs of tread patterns and the use of the high-grip polymers as new materials are discovered. The self-aligning torque of the radial-ply tyre is greater than the cross-bias tyre, but it is not a problem on the lighter vehicle.
Transport managements choosing hgv tyres are looking for tread life, structural performance and remouldability, road holding and fuel consumption. It is significant that high on the list of developments are two prime properties: tread life and road holding; and one combined property, fuel consumption. Low-profile tyres, too, are now being looked at and it will not be long before some vehicle manufacturer will be offered these by tyre manufacturers as an optional fitment. THE MAIN PROBLEM concerning a tyre-development engineer is to know how to improve the product without losing any of its essential characteristics.
Today there are two basic types of tyre: cross-ply and radial-ply.
Cross-ply tyres are made of two or more layers of rubberised fabric — usually rayon or nylon — which are cut at a bias angle, laid in a criss-cross manner, and reinforced for adherence on the wheel rim by multifilament bead wires.
The more recent radial-ply tyre has two main characteristics. First, the wall plies are laid radially to ensure maximum wail flexibility; secondly, a tread bracing of supple steel cord holds the tread pattern steady, open and flat across its full width on the road surface.
The tyre manufacturer uses many compounds when constructing his tyres, and many of these may appear to be similar but in fact they differ greatly in their properties. For example, compounds used in the sidewall must allow it to be flexible yet crack-resistant, while the tread has to wear well and provide maximum adhesion to the road surface.
The forces acting upon a tyre when it is in contact with the road surface can be considered in two parts. Comfort and transmitted noise are dependent on the type and condition of road surface, frictional forces relate to the actual contact and grip,