Your tyres are on the panel
Page 38
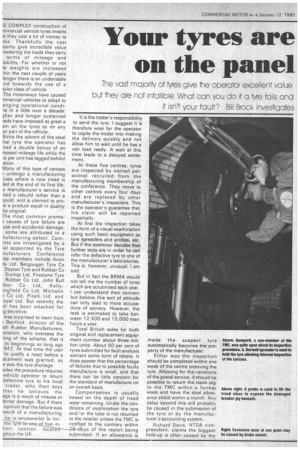
Page 39
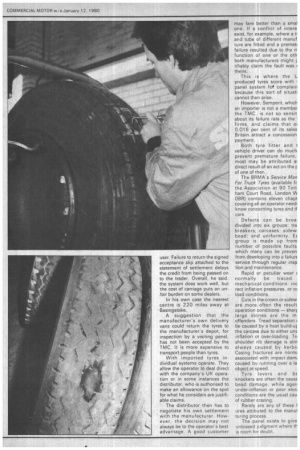
If you've noticed an error in this article please click here to report it so we can fix it.
The vast majority of yes give e operator excellent value out ey are not infallible. What can you do if a ye fails and it isn't your fault? Bill Brock investigates
It is the trader's responsibility to send the tyre. I suggest it is therefore wise for the operator to cajole the trader into making the delivery quickly and not allow him to wait until he has a van load ready. A wait at this time leads to a delayed settlement.
At these five centres, tyres are inspected by trained personnel recruited from the manufacturing membership of the conference. They move to other centres every four days and are replaced by other manufacturer's inspectors. This is the operator's guarantee that his claim will be reported impartially..
At first the inspection takes the form of a visual examination using such basic equipment as tyre spreaders and probes, etc. But if the examiner decides that further tests are in order he can refer the defective tyre to one of the manufacturer's laboratories. This is, however, unusual, I am told.
But in fact the BRMA would not tell me the number of tyres which are scrutinised each year. i can understand their concern but believe this sort of attitude can only lead to more accusations of secrecy. However, the task is estimated to take between 12,500 and 15,000 man hours a year.
Total British sales for both original and replacement equipment number about three million units. About 60 per cent of tyres submitted for fault analysis warrant some form of rebate. It does appear that the percentage of failures due to possible faulty manufacture is small, and that there can be little concern for the standard of manufacture on an overall basis.
Compensation is usually based on the depth of tread wear remaining. Urder the conditions of examination the tyre and/or the tube is not returned to the retailer unless the TMC is the contrary within report being allowance is made the suspect tyre automatically becomes the property of the manufacturer. •
Either way the inspection should be completed within one week of the centre receiving the tyre. Allowing for the variations of the postal service, i should be possible to return thei claim slip to the TMC within la further week and have the tbtal allowance sttled within a.month. Any delay beyond this will probably be caused in the submission of the tyre or by the manufacturer's accounting system..
Richard Davis, NTDA vicepresident, claims the biggest hold-up is often caused by the user. Failure to return the signed acceptance slip attached to the statement of settlement delays the credit from being passed on to the trader. Overall, he said, the system does work well, but the cost of carriage puts an un
:fair burden on some dealers. , In his own case the nearest centre is 220 miles away at Basingstoke.
A suggestion that the manufacturer's own delivery vans could return the tyres to the manufacturer's depot, for inspection by a visiting panel, has not been accepted by the TMC. It is more expensive to transport people than tyres.
With imported tyres individual systems operate. They allow the operator to deal direct with the company's UK operation or in some instances the distributor, who is authorised to make an allowance on the spot for what he considers are justifiable claims.
The distributor then has to negotiate his own settlement with the manufacturer. However, the decision may not always be to the operator's best advantage. A good customer
may fare better than a smal one. If a conflict of intere exist, for example, where a t, and tube of different manuf ture are fitted and a premati failure resulted due to the rr function of one or the oth both manufacturers might j tifiably claim the fault was theirs.
This is where the L produced tyres score with 1 panel system fol. complain because this sort of situati cannot then arise.
However, Semperit, which an importer is not a member the TMC, is not so sensit about its failure rate as the I firms, and claims that oi 0.016 per cent of its sales Britain attract a concession. payment.
Both tyre fitter and 1 vehicle driver can do much prevent premature failure, most may be attributed a; direct result of an act on the r of one of then .
The BRMA's Service Man For Truck Tyres (available fr the Association at 90 Tott, ham Court Road, London VV OBR) contains eleven chapt covering all an operator need: know concerning tyres and tt care.
Defects can be broa, divided into six groups: tre breakers; carcases; sidewi bead; and uniformity. EE group is made up from number of possible faults which many can be preven. from developing into a failurE service through regular insp tion and maintenance..
Rapid or peculiar wear ( normally be traced mechanical conditions: inc rect inflation pressures, or o■ load conditions.
Cuts in the crown or sidew, are more often the result operation conditions — sharr large stones are the m. offenders. Tread separation ( be caused by a heat build-ur the carcass due to either unc inflation or over-loading. To shoulder rib damage is alm always caused by kerbii Casing fractures are norm associated with impact dami caused by running over a la object at speed.
Tyre levers and bE knockers are often the causE bead damage, while ageii under-inflation or poor ston conditions are the usual cau of rubber crazing.
Rarely are any of these 1 ures attibuted to the rnanui turing process.
The panel exists to give unbiased judgment where tiis room for doubt