Remoulds are back in favour
Page 29
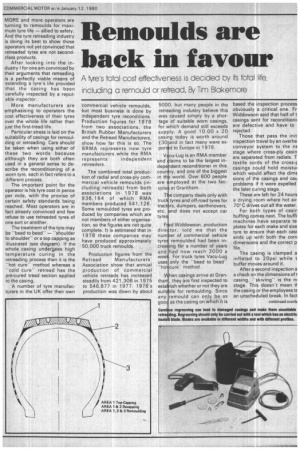
Page 30
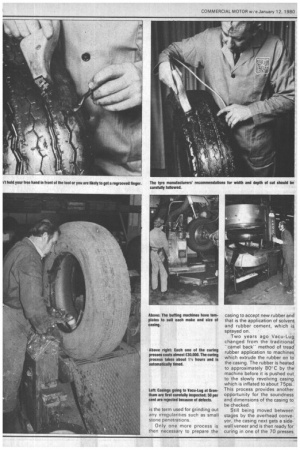
Page 31
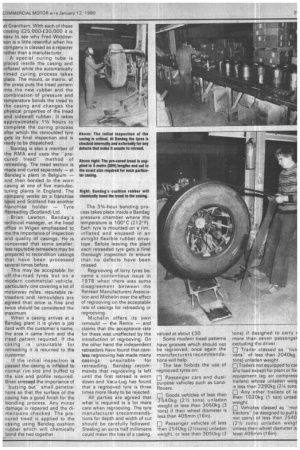
If you've noticed an error in this article please click here to report it so we can fix it.
MORE and more operators are turning to remoulds for maximum tyre life — allied to safety. And the tyre retreading industry is doing its best to show those operators not yet convinced that retreaded tyres are not secondclass products.
After looking into the industry I for one am convinced by their arguments that retreading is a perfectly viable means of extending a tyre's life provided that the casing has been carefully inspected by a reputable inspector.
More manufacturers are emphasising to operators the cost effectiveness of their tyres over the whole life rather than just the first-tread life.
Particular stress is laid on the suitability of casings for remoulding or retreading. Care should be taken when using either of these two words because although they are both often used in a general sense to describe the reconditioning of a worn tyre, each in fact refers to a different process.
The important point for the operator is his tyre cost in pence per mile, with the proviso of certain safety standards being reached. Most operators are in fact already convinced and few refuse to use retreaded tyres of one sort or another.
The treatment of the tyre may be "bead to bead" — "shoulder to shoulder" or a top capping as illustrated (see diagram). If the whole casing undergoes high temperature curing in the retreading process then it is the "hot cure" method whereas a "cold cure" retread has the pre-cured tread section applied to the casing.
A number of tyre manufacturers in the UK offer their own commercial vehicle remoulds, but most business is done by independent tyre reconditions. Production figures for 1978 from two associations, the British Rubber Manufacturers and the Retread Manufacturers, show how far this is so. The BRMA represents new tyre manufacturers while the RMA represents independent retreaders.
The combined total production of radial and cross-ply commercial vehicle remoulds (including retreads) from both associations in 1978 was 936,164 of which RMA members produced 541,126. Some remoulded tyres are produced by companies which are not members of either organisation, so the figures are not quite complete. It is estimated that in 1978 these companies may have produced approximately 50,000 truck remoulds.
Production figures from the Retread Manufacturers' Association show that annual production of commercial vehicle retreads has increased steadily from 421,306 in 1975 to 546,877 in 1977. 1978's production was down by about 5000, but many people in the retreading industry believe this was caused simply by a shortage of suitable worn casings, for which demand still exceeds supply. A good 10.00 x 20 casing today is worth around E30 and in fact many were export d to Europe in 1978.
V cu-Lug is an RMA member and laims to be the largest indope dent reconditioner in this coun ry, and one of the biggest in th world. Over 600 people are mployed at the two feetone at Grantham.
true tract etc, tyre
e company deals only with tyres and off-road tyres for rs, dumpers, earthrnovers, nd does not accept car
dire num tyre crea and wee uses "hot d Wirldowson, production tor, told me that the er of commercial vehicle remoulded had been ining for a number of years had now reach 3000 a . For truck tyres Vacu-Lug only the "bead to bead" cure method.
tha esta suit any goo hen casings arrive at G ranthey are first inspected to Fish whether or not they are ble for remoulding. Since remould can only be as as the casing on which it is based the inspection process obviously a critical one, Fr Widdowson said that half of t casings sent for reconditionii are defective and have to rejected.
Those that pass the init inspection travel by an overhe conveyor system to the nE stage where cross-ply casin are separated from radials. T textile cords of the crosscasings could hold moistut which would affect the dime sions of the casings and cau problems if it were expelled the later curing stage.
These are left for 24 hours a drying room where hot air 70°C drives out all the water.
For both types of casin buffing comes next. The buffi machines have separate te plates for each make and size tyre to ensure that each casi ends up with both the corn dimensions and the correct p file.
The casing is clamped a inflated to 20psi while t buffer moves around it.
After a second inspection a a check on the dimensions of t casing, –skiving" is the ni stage. This doesn't mean ti the casing or the employees ta an unscheduled break. In fact
continued overle is the term used for grinding out any irregularities such as small stone penetrations.
Only one more process is then necessary to prepare the casing to accept new rubber and that is the application of solvent and rubber cement, which is sprayed on.
Two years ago Vacu-Lug changed from the traditional "camel back" method of tread rubber application to machines which extrude the rubber on to the casing. The rubber is heated to approximately 80'C by the machine before it is pushed out to the slowly revolving casing which is inflated to about 75psi. This process provides another opportunity for the soundness and dimensions of the casing to be checked.
Still being moved between stages by the overhead conveyor, the casing next gets a sidewall veneer and is then ready for curing in one of the 70 presses at Grantham. With each of these costing £25,000-£30,000 it is easy to see why Fred Widdowson is a little resentful when his corn pany is classed as a repairer rather than a manufacturer.
A special curing tube is placed inside the casing and inflated while the automatically timed curing process takes place. The mould, or matrix, of
the press puts the tread pattern into the new rubber and the combination of pressure and temperature bonds the tread to the casing and changes the physical properties of the tread and, sidewatl rubber. It takes .approximately 11/2 hours to complete the curing process after which the remoulded tyre gets its final inspection and is .ready to be dispatched.
Bandag is also a member of the RMA and uses the "precured tread" method of retreading. The tread section is made and cured separately — at Bandag's plant in Belgium — and then bonded to the worn casing at one of five manufacturing plants in England. The company works on a franchise basis and Scotland has another franchise holder — Tyre Retreading (Scotland) Ltd.
Brian Lawton, Bandag's technical manager, at the head office in Wigan emphasised to me the importance of inspection and quality of casings. He is concerned that some smaller, less reputable retreaders may be prepared to recondition casings that have been processed several times before.
This may be acceptable for off-the-road tyres but on a modern commercial vehicle, particularly one covering a lot of motorway miles, reputable retreaders and remoulders are agreedthat once is fine and twice should be considered the maximum.
When a casing arrives at a Bandag plant it is given a job card with the customer's name, the area it came from and the tread pattern required. If the casing is unsuitable for retreading it is returned to the customer.
If the initial inspection is passed the casing is inflated to normal rim size and buffed to the size and profile required. Brian stressed the importance of -buzzing out'' small penetrations so that the surface of the casing has a good finish for the bonding process. Any minor damage is repaired and the dimensions checked. The precured tread is applied to the casing using Bandag cushion rubber which will chemically bond the two together. The 334-hour bonding process takes place inside a Bandag pressure chamber where the
temperature is 100C (212'F). Each tyre is mounted on a rim, inflated and encased in an airtight flexible rubber envelope. Before leaving the plant each retreaded tyre gets a final thorough inspection to ensure that no defects have been missed.
Regrooving of lorry tyres became a contentious issue in 1978 when there was some disagreement between the Retread Manufacturers Association and Michelin over the effect of regrooving on the acceptable rate of casings for retreading or regrooving.
Michelin offers its own remould — the Rernix — and claims that the acceptance rate for these was unaffected by the introduction of regrooving. On the other hand the independent retreaders have found that careless regrooving has made many casings unsuitable for retreading. Bandag recommends that regrooving is left until the first retread is worn down and Vacu-Lug has found that a regrooved tyre is three times more likely to be rejected.
All parties are agreed that what is required is a lot more care when regrooving. The tyre manufacturer'srecommendations for depth and width of cut should be carefully followed. Stealing an extra half millimetre could mean the lass of a casing, valued at about £30.
Some modern tread patterns have grooves which should not be regrooved; once again the manufacturers recommendations will help.
The law forbids the use of regrooved tyres on.
El Passenger cars and dualpurpose vehicles such as LandRovers.
E Goods vehicles of less than 2540kg (21/2 tons) unladen weight or less than 3050kg (3 tons) if their wheel diameter is less than 405mm (16in).
El Passenger vehicles of less than 2540kg (21/2tens) unladen weight, or less than 3050kg (3
tons) if designed to carry r more than seven passenger excluding the driver.
Trailer classed as vans" of less than 2040kg tons) unladen weight.
El Trailers not equipped to car any load except for plant or fix' equipment (eg air compress trailers) whose unladen weig is less than 2290kg (21/4 tons E Any other trailers of le than 1020kg (1 ton) unlacf weight.
El Vehicles classed as "mot tractors" (ie designed to pull b not carry) of less than 2540 (21/2 tons) unladen weigh unless their wheel diameter is least 405rnm (16in).