AMPLE MECHANICS
Page 51
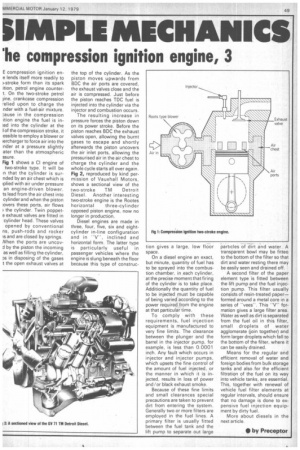
If you've noticed an error in this article please click here to report it so we can fix it.
'he compression ignition engine, 3
E compression ignition ene lends itself more readily to )-stroke form than its spark ition, petrol engine countert. On the two-stroke petrol jine, .crankcase compression -elied upon to charge the nder with a fuel-air mixture. :ause in the compression ition engine the fuel is inJed into the cylinder at the I of the compression stroke, it ossible to employ a blower or iercharger to force air into the nder at a pressure slightly ater than the atmospheric ssure.
Fig 1 shows a Cl engine of two-stroke type. It will be n that the cylinder is surnded by an air chest which is 'plied with air under pressure an engine-driven blower. ts lead from the air chest into cylinder and when the piston :overs these ports, air flows the cylinder. Twin poppete exhaust valves are fitted in cylinder head. These valves opened by conventional ns, push-rods and rocker is and are closed by springs. Nhen the ports are uncovd by the piston the incoming as well as filling the cylinder, s in disposing of the gases t the open exhaust valves at the top of the cylinder. As the piston moves upwards from BDC the air ports are covered, the exhaust valves close and the air is compressed. Just before the piston reaches TDC fuel is injected into the cylinder via the injector and combustion occurs.
The resulting increase in pressure forces the piston down on its power stroke. Before the piston reaches BDC the exhaust valves open, allowing the burnt gases to escape and shortly afterwards the piston uncovers the air inlet ports, allowing the pressurised air in the air chest to charge the cylinder and the whole cycle starts all over again. Fig 2, reproduced by kind permission of Vauxhall Motors, shows a sectional view of the two-stroke TM Detroit Diesel. Another interesting two-stroke engine is the Rootes horizontal three-cylinder opposed piston engine, now no longer in production.
Diesel engines are made in three, four, five, six and eightcylinder in-line configuration and in "V', inclined and horizontal form. The latter type is particularly useful in passenger vehicles where the engine is slung beneath the floor because this type of construc
ion gives a large, low floor space.
On a diesel engine an exact, but minute, quantity of fuel has to be sprayed into the combustion chamber, in each cylinder, at the precise moment that firing of the cylinder is to take place. Additionally the quantity of fuel to be injected must be capable of being varied according to the power required from the engine at that particular time.
To comply with these requirements, fuel injection equipment is manufactured to very fine limits. The clearance between the plunger and the barrel in the injector pump, for example, is less than 0.0001 inch. Any fault which occurs in injector and injector pumps, which upsets the fine control of the amount of fuel injected, or the manner in which it is injected, results in loss of power and/or black exhaust smoke.
Because of these fine limits and small clearances special precautions are taken to prevent dirt from entering the system. Generally two or more filters are employed in the fuel lines. A primary filter is usually fitted between the fuel tank and the lift pump to separate out large
particles of -dirt and water. A transparent bowl may be fittea to the bottom of the filter so that dirt and water resting there may be easily seen and drained off.
A second filter of the paper element type is fitted between the lift pump and the fuel injection pump. This filter usually consists of resin-treated paper— formed around a metal core in a series of -vees". This "V" formation gives a large filter area. Water as well as dirt is separated from the fuel oil in this filter, small droplets of water agglomerate (join together) and form larger droplets which fall to the bottom of the filter, where it can be easily drained.
Means for the regular and efficient removal of water and foreign bodies from bulk storage tanks and also for the efficient filtration of the fuel on its way into vehicle tanks, are essential. This, together with renewal of vehicle fuel filter elements at regular intervals, should ensure that no damage is done to expensive fuel injection equipment by dirty fuel.
More about diesels in the next article.
• by Preceptor