Fuel pump is the heart of the engine
Page 41
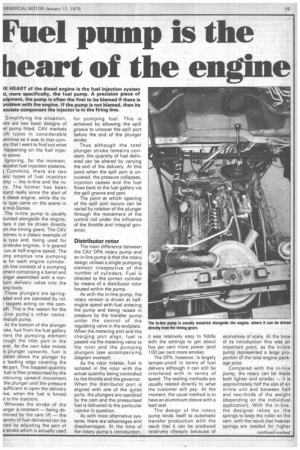
Page 42
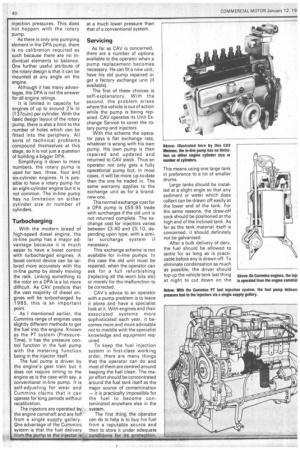
Page 43
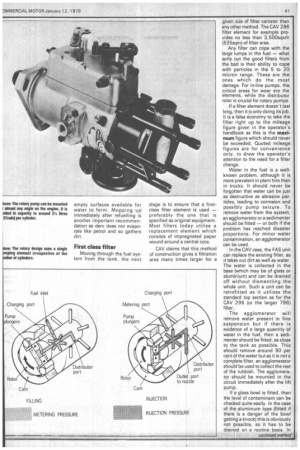
Page 44
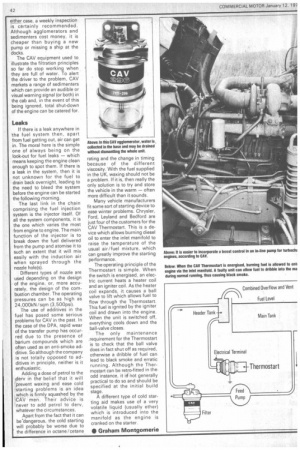
If you've noticed an error in this article please click here to report it so we can fix it.
.IE HEART of the diesel engine is the fuel injection system d, more specifically, the fuel pump. A precision piece of iuipment, the pump is often the first to be blamed if there is problem with the engine. If the pump is not blamed, then its sociate component the injector is in the firing line.
Simplifying the situation, iere are two basic designs of iel pump fitted. CAV markets Dth types in considerable iantities so it was to that cornmy that I went to find out what happening on the fuel injecm scene.
Ignoring, for the moment, lecialist fuel injection systems, 3 Cummins, there are two )sic types of fuel injection imp — the in-line and the rory. The former has been ound really since the start of e diesel engine, while the rory type came on the scene in e mid-Sixties.
The in-line pump is usually ounted alongside the engine, here it can be driven directly Dm the timing gears. The CAV inimec is a classic example of is type and, being used for ur-stroke engines, it is geared run at half-engine speed. The imp employs one pumping le for each engine cylinder. )ch line consists of a pumping ament comprising a barrel and unger assembled with a nonturn delivery valve into the imp body.
These plungers are springaded and are operated by rolr tappets acting on the cam'aft. This is the reason for the -line pump's other name: irnshaft pump.
At the bottom of the plunger roke, fuel from the fuel gallery iters the pumping element rough the inlet port in the irrel. As the cam lobe moves e plunger upwards, fuel is plated above the plunger by e leading edge covering the let port. This trapped quantity fuel is then pressurised by the sntinuing upward movement the plunger until the pressure sufficient to open the delivery dye, when the fuel is forced it to the injectors.
Whereas the stroke of the unger is constant — being dermined by the cam lift — the iantity of fuel delivered can be If-led by adjusting the part of e stroke which is actually used
for pumping fuel. This is achieved by allowing the spill groove to uncover the spill port before the end of the plunger stroke.
Thus although the total plunger stroke remains constant, the quantity of fuel delivered can be altered by varying the end of the delivery. At this point when the spill port is uncovered, the pressure collapses, injection ceases and the fuel flows back to the fuel gallery via the spill groove and port.
The point at which opening of the spill port occurs can be varied by rotation of the plunger through the movement of the control rod under the influence of the throttle and integral governor.
Distributor rotor
The main difference between the CAV DPA rotary pump and an in-line pump is that the rotary design utilises a single pumping element irrespective of the number of cylinders. Fuel is directed to the correct cylinder by means of a distributor rotor housed within the pump.
As with the in-line pump, the rotary version is driven at halfengine speed with fuel entering the pump and being raised in pressure by the transfer pump under the control of the regulating valve in the endplate. When the metering port and the charging port align, fuel is passed via the metering valve to the rotor and the pumping plungers (see accompanying diagram overleaf).
As the rotor rotates, fuel is isolated in the rotor with the actual quantity being controlled by the throttle and the governor. When the distributor port is aligned with one of the outlet ports, the plungers are operated by the cam and the pressurised fuel is delivered to the particular injector in question.
As with most alternative systems, there are advantages and disadvantages. At the time of the rotary pump's introduction, it was relatively easy to fiddle With the settings to get about five per cent more power (and 100 per cent more smoke).
The DPA, however, is largely tamper-proof in terms of fuel delivery although it can still be interfered with in terms of speed. The sealing methods are usually related directly to what the customer will pay. At the moment, the usual method is to have an aluminium sleeve with a lead seal.
The design of the rotary pump lends itself to automatic transfer production with the result that it can be produced relatively cheaply because of economies of scale. At the time of its introduction this was an important point, as the in-line pump represented a large proportion of the total engine package price.
Compared with the in-line pump, the rotary can be made both lighter and smaller — it is approximately half the size of an in-line unit and between half and two-thirds of the weight (depending on the individual application). With the in-line, the designer relies on the springs to keep the roller on the cam, with the result that heavier springs are needed for higher
injection pressures. This does. not happen with the rotary pump.
As there is only one pumping element in the DPA pump, there is no calibration required as such because there are no individual elements to balance. One further useful attribute of the rotary design is that it can be mounted at any angle on the engine.
Although it has many advantages, the DPA is not the answer for all engine ratings.
It is limited in capacity for engines of up to around 21/4 lit (137cuin) per cylinder. With the basic design layout of the rotary pump, there is also a limit to the number of holes which can be fitted into the periphery. All sorts of technical problems compound themselves at this stage, so it is not just a question of building a bigger DPA.
Simplifying it down to mere numbers, the rotary pump is used for two, three, four and six-cylinder engines. It is possible to have a rotary pump for an eight-cylinder engine but it is not common. The in-line pump has no limitation on either cylinder size or number of cylinders.
Turbocharging
With the modern breed of high-speed diesel engine, the in-line pump has a major advantage because it is much easier to have a boost control with turbocharged engines. A boost control device can be tailored more accurately with the in-line pump by slowly moving the rack. Linking something to the rotor on a DPA is a lot more difficult. As CAV predicts that the vast majority of diesel engines will be turbocharged by 1985, this is an important point.
As I mentioned earlier, the Cummins range of engines uses slightly different methods to get the fuel into the engine. Known as the PT system (PressureTime), it has the pressure control function in the fuel pump with the metering function being in the injector itself.
The fuel pump is driven by the engine's gear train but it does not require timing to the engine as is the case with say, a conventional in-line pump. It is self-adjusting for wear and Cummins claims that it can operate for long periods without recalibration.
The injectors are operated by the engine camshaft and are fed from a single supply gallery. One advantage of the Cummins system is that the fuel delivery from the pump to the injector is. at a much lower pressure than that of a conventional system.
Servicing.
As far as CAV is concerned, there are a number of options -available to the operator when a pump replacement becomes
necessary. He can fit a new unit, have his old pump repaired or get a factory exchange unit (if available).
The first of these choices is self-explanatory. With the second, the problem arises where the vehicle is out of action while the pump is being rep aired. CAV operates its Unit Exchange Service to cover the rotary pump and injectors.
With this scheme the opera tor pays a flat exchange rate, whatever is wrong with his own pump. His own pump is then repaired and updated and returned to CAV stock. Thus an operator not only gets a fully operational pump but, in most cases, it will be more up-to-date than the one he traded in. The same warranty applies to the exchange unit as for a brandnew one.
The normal exchange cost for a DPA pump is £59.95 trade with surcharges if the old unit is not returned complete. The exchange cost for injectors varies between £3.40 and £5.10, depending upon type, with a similar surcharge system if necessary.
This exchange scheme is not available for in-line pumps, In this case the old unit must be repaired, when the operator can ask for a full refurbishing (replacing all the worn bits etc) or merely for the malfunction to be corrected.
CAV's advice to an operator with a pump problem is to leave it alone and have a specialist look at it. With engines and their associated systems more sophisticated each year, it becomes more and more advisable not to meddle with the specialist knowledge and equipment required.
To keep the fuel injection system in first-class working order, there are many things that the operator can do and most of them are centred around keeping the fuel clean. The major effort should be concentrated around the fuel tank itself as the major source of contamination — it is practically impossible for the fuel to become contaminated anywhere else in the system.
The first thing the operator can do to help is to buy his fuel from a reputable source and then to store it under adequate conditions for its protection. This means using one large tank in preference to a lot of smaller drums.
Large tanks should be installed at a slight angle so that any sediment or water which does collect can be drawn off easily at the lower end of the tank. For the same reasons, the draw-off cock should be positioned at the high end of the inclined tank. As far as the tank material itself is concerned, it should definitely not be galvanised.
After a bulk delivery of derv, the fuel should be allowed to settle for as long as is practicable before any is drawn off. To .eliminate condensation as much as possible, the driver should top up the vehicle tank last thing at night to cut down on the
empty surfaces available for water to form. Mopping up: immediately after refuelling is another important recommendation as dery does not evaporate like petrol and so gathers dirt.
First class filter
Moving through the fuel system from the tank, the next stage is to ensure that a firstclass filter element is used — preferably the one that is specified as original equipment. Most filters today utilise a replacement element which consists of impregnated paper wound around a central core.
CAV claims that this method of construction gives a filtration area many times larger for a given size of filter canister than any other method. The CAV 296 filter element for example provides no less than 3.500sqcnn (535sqin) of filter area.
Any filter cab cope with the large lumps in the fuel — what sorts out the good filters from the bad is their ability to cope with particles in the 5 to 20 micron range. These are the ones which do the most damage. For in-line pumps, the.
critical areas for wear are the elements, while the distributor rotor is crucial for rotary pumps. If a filter element doesn't last long, then it is only doing its job.
It is a false economy to. take the filter right up to the mileage figure given in the operator's handbook as this is the maximum figure which should never,
be exceeded. Quoted mileage figures are for convenience only, to draw the operator's attention to the need for a filter change.
Water in the fuel is a wellknown problem, although it is more prevalent in plant hire than in trucks. It should never be forgotten that water can be just as destructive as abrasive par ticles, leading to corrosion and possibly pump seizure. To remove water from the system, an agglomerator or a sedimenter should be fitted — or both if the
problem has reached disaster proportions. For minor water contamination, an agglomerator can be used.
In the CAV case, the FAS unit can replace the existing filter, as it takes out dirt as well as water.
The water is collected in the base (which may be of glass or aluminium) and can be drained off without dismantling the whole unit. Such a unit can be retrofitted as it utilizes the standard top section as for the CAV 296 (or the larger 796) filter.
The agglomerator will remove water present in fine suspension but if there is evidence of a large quantity of water in the fuel, then a sedi menter should be fitted, as close to the tank as possible. This should remove around 90 per cent of the water but as it is not a complete filter, an agglomerator should be used to collect the rest of the rubbish. The agglomerator should be mounted in the circuit immediately after the lift pump.
If a glass bowl is fitted, then the level of contaminant can be checked quite easily. In the case of the aluminium type (fitted if there is a danger of the bowl getting a knock) this is obviously not possible, so it has to be drained on a routine basis. In either case, a weekly inspection is certainly recommended. Although agglomerators and sedimenters cost money, it is cheaper than buying a new pump or missing a ship at the docks.
The CAV equipment used to illustrate the filtration principles so far do stop working when they are full of water. To alert the driver to the problem, CAV markets a range of sedimenters which can provide an audible or visual warning signal (or both) in the cab and, in the event of this being ignored, total shut-down of the engine can be catered for.
Leaks
If there is a leak anywhere in the fuel system then, apart from fuel getting out, air can get in. The moral here is the simple one of always being on the look-out for fuel leaks — which means keeping the engine clean enough to spot them. If there is a leak in the system, then it is not unknown for the fuel to drain back overnight, leading to the need to bleed the system before the engine can be started the following morning.
The last link in the chain comprising the fuel injection system is the injector itself. Of all the system components, it is the one which varies the most from engine to engine. The main function of the injector is to break down the fuel delivered from the pump and atomise it to such an extent that it will mix easily with the induction air when sprayed through the nozzle hole(s).
Different types of nozzle are used depending on the design of the engine, or, more accurately, the design of the combustion chamber. The operating pressures can be as high as 24,000kN /sqm (3,500psi).
The use of additives in the fuel has posed some serious problems for CAV in the past. In the case of the DPA, rapid wear of the transfer pump has occurred due to the presence of barium compounds which are often used as an anti-smoke additive. So although the company is not totally opposed to additives in principle, neither is it enthusiastic.
Adding a dose of petrol to the dery in the' belief that it will prevent waxing and ease cold starting problems is an idea which is firmly squashed by the CAV men. Their advice is never to add petrol to derv, whatever the circumstances.
Apart from the fact that it can bedangerous, the cold starting will probably be worse due to the difference in octane /cetane rating and the change in timing because of the different viscosity. With the fuel supplied in the UK, waxing should not be a problem. If it is, then really the only solution is to try and store the vehicle in the warm — often more difficult than it sounds.
Many vehicle manufacturers fit some sort of starting device to ease winter problems. Chrysler, Ford, Leyland and Bedford are just four of the customers for the CAV Thermostart. This is a device which allows burning diesel oil to enter the inlet manifold to raise the temperature of the usual air/fuel mixture, which can greatly improve the starting performance.
The operating principle of the Thermostart is simple. When the switch is energised, an electric current heats a heater coil and an igniter coil. As the heater coil expands, it causes a ball valve to lift which allows fuel to flow through the Thermostart. This fuel is ignited by the igniter coil and drawn into the engine. When the unit is switched off, everything cools down and the ball-valve closes.
The only maintenance .requirement for the Thermostart is to check that the ball valve does in fact shut off as required, otherwise a dribble of fuel can lead to black smoke and erratic running. Although the Thermostart can be retro-fitted in the odd instance, it i4.not generally practical to do so and should be specified at the initial build stage.
A different type of cold starting aid makes use of a very volatile liquid (usually ether) which is introduced into the manifold as the engine is cranked on the starter.
• Graham Montgomerie