Simple hints for smooth running
Page 37
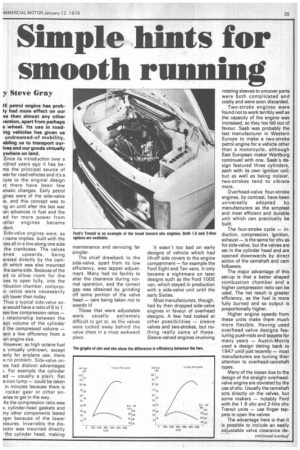
Page 38
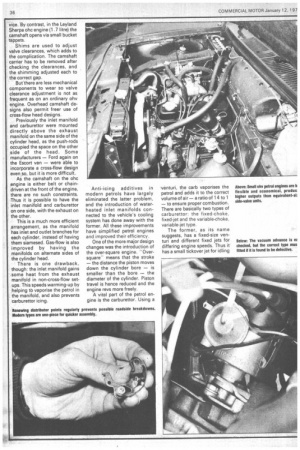
Page 39
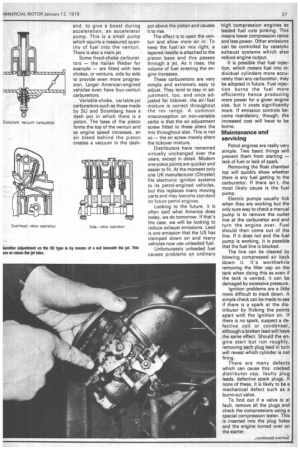
Page 40
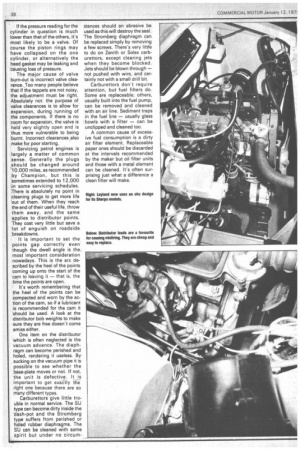
If you've noticed an error in this article please click here to report it so we can fix it.
y Steve Gray
IE petrol engine has probly had more effect on our es than almost any other rention, apart from perhaps B wheel. Its use in roadfrig vehicles has given us undreamed-of mobility, abling us to transport ourIves and our goods virtually ywhere on land.
Since its introduction over a ndred years ago it has beme the principal source of wer for road vehicles and its a Dute to the original design at there have been few )matic changes. Early petrol gines were of the side-valve )e, and this concept was to ng on until after the last war len advances in fuel and the ed for more power from ialler engines became ident.
Side-valve engines were, as ) name implies, built with the Ives all in a line along one side
the crankcase. The valves ened upwards, being erated directly by the careaft which was also mounted the same side. Because of the ed to allow room for the Ives to open fully, into the -nbustion chamber, compresin ratios were necessarily ich lower than today.
Thus a typical side-valve enie would have a ratio of 6 to 1. ese low compression ratios — a relationship between the 'ept volume of the cylinder d the compressed volume — :ant a low efficiency from a fen engine size.
However, as high octane fuel is virtually unknown, except terly for airplane use, there is no problem. Side-valve enles had distinct advantages ). For example the cylinder ad — usually a plain, flat 5t-iron lump — could be taken in minutes because there is rocker gear or other anaries to get in the way.
As the compression ratio was v, cylinder-head gaskets and iny other components lasted -Ter because of the lower assures. Invariably the disDutor was mounted directly
the cylinder head, making maintenance and servicing far simpler.
The chief drawback to the side-valve, apart from its low efficiency, was tappet adjustment. Many had no facility to alter the clearance during normal operation, and the correct gap was obtained by grinding off some portion of the valve head — care being taken not to overdo it!
Those that were adjustable were usually extremely difficult to get at, as the valves were tucked away behind the valve chest in a most awkward place. It wasn't too bad on early designs of vehicle which had lift-off side covers to the engine compartment — for example the Ford Eight and Ten vans. It only became a nightmare on later designs such as the Ford 1 00 E van, which stayed in production with a side-valve unit until the early Sixties.
Most manufacturers, though, had by then dropped side-valve engines in favour of overhead designs. A few had looked at other possibilities — sleeve valves and two-strokes, but nothing really came of these. Sleeve-valved engines involving rotating sleeves to uncover ports were both complicated and costly and were soon discarded.
Two-stroke engines were found not to work terribly well as the capacity of the engine was increased, so they too fell out of favour. Saab was probably the last manufacturer in Western Europe to make a two-stroke petrol engine for a vehicle other than a motorcycle, although East European maker Wartburg continued with one. Saab's design featured three cylinders, each with its own ignition coil;, but as well as being noisier, two-strokes tend to vibrate more.
Overhead-valve four-stroke engines, by contrast, have been universally adopted by manufacturers as the simplest and most efficient and durable unit which can practically be built.
The four-stroke cycle — induction, compression, ignition, exhaust — is the same for oh)" as for side-valve, but the valves are set in the cylinder head and are opened downwards by direct action of the camshaft and cam followers.
The major advantage of this set-up is that a better shaped combustion chamber and a higher compression ratio can be used. The net result is greater efficiency, as the fuel is more fully burned and so output is proportionally higher.
Higher engine speeds from these units make them much more flexible. Having used overhead valve designs featuring push-rods and tappets for many years — Austin-Morris used a design dating back to 1947 until just recently — most manufacturers are turning their attention to overhead-camshaft types.
Many of the losses due to the design of the straight overheadvalve engine are obviated by the use of ohc. Usually the camshaft acts directly on the valves, but some makers — notably Ford with the 1.6 ohc and 2-litre ohc Transit units — use finger tappets to open the valves.
The advantage here is that it is possible to include an easily adjustable valve clearance de-, vice. By contrast, in the Leyland Sherpa ohc engine (1.7 litre) the camshaft opens via small bucket tappets Shims are used to adjust valve clearances, which adds to the complication. The camshaft carrier has to be removed after checking the clearances, and the shimming adjusted each to the correct gap.
Bufthere are less mechanical components to wear so valve clearance adjustment is not as frequent as on an ordinary ohv engine. Overhead camshaft designs also permit freer use of cross-flow head designs.
Previously the inlet manifold and carburettor were mounted directly above the exhaust manifold on the same side of the cylinder head, as the push-rods occupied the space on the other side of the head. Some manufacturers — Ford again on the Escort van — were able to incorporate a cross-flow design even so, but it is more difficult.
As the camshaft on the ohc engine is either belt or chaindriven at the front of the engine, there are no such constraints. .Thus it is possible to have the inlet manifold and carburettor on one side, with the exhaust on the other.
This is a much more efficient .arrangement, as the manifold has inlet and outlet branches for each cylinder, instead of having them siamesed. Gas-flow is also improved by having the manifolds on alternate sides of the cylinder head.
There is one drawback, though: the inlet manifold gains some heat from the exhaust manifold in non-cross-flow setups. This speeds warming-up by helping to vaporise the petrol in the manifold, and also prevents carburettor icing. Anti-icing additives in modern petrols have largely eliminated the latter problem, and the introduction of waterheated inlet manifolds connected to the vehicle's cooling system has done away with the former. All these improvements have simplified petrol engines and improved their efficiency.
One of the more major design changes was the introduction of the over-square engine. Oversquaremeans that the stroke — the distance the piston moves down the cylinder bore — is smaller than the bore — the diameter of the cylinder. Piston travel is hence reduced and the engine revs more freely.
A vital part of the petrol engine is the carburettor. Using a .venturi, the carb vaporises the petrol and adds it to the correct volume of air — a ratio of 14 to 1 — to ensure proper combustion. There are basically two types of carburettor: the fixed-choke. fixed-jet and the variable-choke, variable-jet type.
The former, as its name suggests, has a fixed-size venturi and different fixed jets for differing engine speeds. Thus it has a small tickover jet for idling and, to give a boost during acceleration, an accelerator pump. This is a small pump which squirts a measured quantity of fuel into the venturi. There is also a main jet.
Some fixed-choke carburettors — the Italian Weber for example — are fitted with two chokes, or venturis, side by side to provide even more progression. Larger American-engined vehicles even have four-venturi carburettors.
Variable-choke, variable-jet carburettors such as those made by SU and Stromberg have a dash pot in which there is a piston. The base of the piston forms the top of the venturi and as engine speed increases, an air bleed behind the piston creates a vacuum in the dash pot above the piston and causes it to rise.
The effect is to open the venturi and allow more air in. To keep the fuel/ air mix right, a tapered needle is attached to the piston base and this passes through a jet. As it rises, the volume of fuel entering the engine increases.
These carburettors are very simple and extremely easy to adjust. They tend to stay in adjustment, too, and once adjusted for tickover, the air/fuel mixture is correct throughout the rev range. A common misconception on non-variable carbs is that the air adjustment screw fitted to these alters the mix throughout also. This is not so — the air screw merely alters the tickover mixture, Distributors have remained virtually unchanged over the years, except in detail. Modern one-piece points are quicker and easier to fit. At the moment only one UK manufacturer (Chrysler) fits electronic ignition systems to its petrol-engined vehicles, but this replaces many moving parts and may become standard on future petrol engines.
Looking to the future, it is often said what America does today, we do tomorrow. If that's the case, we will be looking to reduce exhaust emissions. Lead is one emission that the US has clamped down on and many vehicles now use unleaded fuel.
Unfortunately unleaded fuel causes problems on ordinary high compression engines as leaded fuel cuts pinking. This means lower compression ratios and less power. Other emissions can be controlled by catalytic exhaust systems which also reduce engine output.
It is possible that fuel injection, which meters fuel into individual cylinders more accurately than any carburettor, may be adopted in future. Fuel injection burns the fuel more efficiently hence producing more power for a given engine size, but it costs significantly more. If emission controls become mandatory, though, the increased cost will have to be borne.
Maintenance and servicing
Petrol engines are really very simple. Two basic things will prevent them from starting — lack of fuel or lack of spark.
Removing the float chamber top will quickly show whether there is any fuel getting to the carburettor. If there isn't, the most likely cause is the fuel Pump.
Electric pumps usually tick when they are working but the only sure way to check a manual pump is to remove the outlet line at the carburettor end and turn the engine over. Fuel should then come out of the line. If it does not and the fuel pump is working, it is possible that the fuel line is blocked.
The line can be cleared by blowing compressed air back down it. It's worthwhile removing the filler cap on the tank when doing this as even if the tank is vented, it can be damaged by excessive pressure.
Ignition problems are a little more difficult to track down. A simple check can be made to see if there is a spark at the distributor by flicking the points apart with the ignition on. If there is no spark, suspect a defective coil or condenser„ although a broken lead will have , the same effect. Should the engine start but run roughly, removing each plug lead in turn will reveal which cylinder is not firing.
There are many defects which can cause this: cracked distributor cap, faulty plug leads, defective spark plugs. If none of these, it is likely to be a mechanical defect such as a burnt-out valve.
To find out if a valve is at fault, remove all the plugs and check the compressions using a special compression tester. This is inserted into the plug holes and the engine turned over on the starter. If the pressure reading for the cylinder in question is much lower than that of the others, it's most likely to be a valve. Of course the piston rings may have collapsed on the one cylinder, or alternatively the head gasket may be leaking and causing loss of pressure.
The major cause of valve burn-out is incorrect valve clearance.,Too many people believe that if the tappets are not noisy, the adjustment must be right. Absolutely not: the purpose of valve clearances is to allow for expansion, during running of the components. If there is no room for expansion, the valve is held very slightly open and is thus more vulnerable to being :burnt. Incorrect clearances also • make for poor starting.
Servicing petrol engines is largely a matter of common sense. Generally the plugs ,should be changed around 10,000 miles, as recommended by Champion, but this is sometimes extended to 12,000 in some servicing schedules. There is absolutely no point in !cleaning plugs to get more life 'out of them. When they reach the end of their useful life, throw them away, and the same applies to distributor points. They cost very little but save a lot of anguish on roadside breakdowns.
It is important to set the points gap correctly even though the dwell angle is the. most important consideration nowadays. This is the arc described by the heel of the points coming up onto the start of the cam to leaving it — that is, the time the points are open.
It's worth remembering that the heel of the points can be compacted and worn by the action of the cam, so if a lubricant is recommended for the cam it 'should be used. A look at the distributor bob weights to make sure they are free doesn't come amiss either.
One item on the distributor which is often neglected is the vacuum advance. The diaphragm can become perished and holed, rendering it useless. By sucking on the vacuum pipe it is possible to see whether the base-plate moves or not. If not, the unit is defective. It is important to get exactly the right one because there are so many different types.
Carburettors give little trouble in normal service. The SU type can become dirty inside the dash-pot and the Stromberg type suffers from perished or holed rubber diaphragms. The SU can be cleaned with some spirit but under no circum stances should an abrasive be used as•this will destroy the seal. The Stromberg diaphragm can be replaced simply by removing a few screws. There's very little to do on Zenith or Solex carburettors, except clearing jets when they become blocked. Jets should be blown through — not pushed with wire, and certainly not with a small drill bit.
Carburettors don't require attention, but fuel filters do. Some are replaceable; others, usually built into the fuel pump, can be removed and cleaned with an air line. Sediment traps in the fuel line — usually glass bowls with a filter — can be unclipped and cleaned too.
A common cause of excessive fuel consumption is a dirty air filter element. Replaceable paper ones should be discarded at the intervals recommended by the maker but oil filter units and those with a metal element can be cleaned. It's often surprising just what a difference a clean filter will make.