road and
Page 48
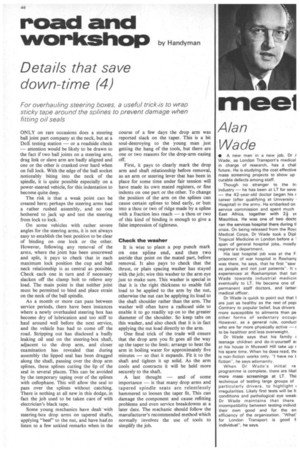
If you've noticed an error in this article please click here to report it so we can fix it.
workshop by Handyman
Details that save down-time (4)
For overhauling steering boxes, a useful trick.is to wrap sticky tape around the splines to prevent damage when fitting oil seals
ONLY on rare occasions does a steering ball joint part company at the neck, but at a DoE testing station — or a roadside check — attention would be likely to be drawn to the fact if two ball joints on a steering arm, drag link or slave arm are badly aligned and one or the other is cranked over hard when on full lock. With the edge of the ball socket noticeably biting into the neck of the spindle, it is quite possible especially on a power-steered vehicle, for this indentation to become quite deep.
The risk is that a weak point can be created here; perhaps the steering arms had a rather rushed assembly, and no one bothered to jack up and test the steering from lock to lock.
On some vehicles with rather severe angles for the steering arms, it is not always easy to establish the best position to be clear of binding on one lock or the other. However, following any removal of the arms, where the joint has been unscrewed and split, it pays to check that in each maximum lock position the cup and ball neck relationship is as central as possible. Check each one in turn and if necessary slacken off the clamp bolt to relieve any load. The main point is that neither joint must be permitted to bind and place strain on the neck of the ball spindle.
As a mouth or more can pass between service periods, there have been instances where a newly overhauled steering box has become dry of lubrication and too stiff to haul around well before the next service, and the vehicle has had to come off the road. Stripping out has disclosed a badly leaking oil seal on the steering-box shaft, adjacent to the drop arm, and closer examination has revealed that during assembly the lipped seal has been dragged along the shaft, passing over the drop arm splines, these splines cutting the lip of the seal in several places. This can be avoided by the temporary taping over of the splines with cellophane. This will allow the seal to pass over the splines without catching. There is nothing at all new in this dodge, in fact the job used to be taken care of with electrician's black tape.
Some young mechanics have dealt with steering-box drop arms on tapered shafts, applying "beef" to the nut, and have had.to listen to a few unkind remarks when in the course of a few days the drop arm was reported slack on the taper. This is a bit soul-destroying to the young man just getting the hang of the tools, but there are one or two reasons for the drop-arm easing off.
First, it pays to clearly mark the drop arm and shaft relationship before removal, as an arm or steering lever that has been in place for some time under fair tension will have made its own mated registers, or fine indents on one part or the other. To change the position of the arm on the splines can cause certain splines to bind early, or butt into a thou or two of ridge made by a spline with a fraction less reach — a thou or two of this kind of binding is enough to give a false impression of tightness.
Check the washer It is wise to place a pop punch mark on one spline end, and then two astride that point on the mated part, before removal. It also pays to check that the thrust, or plain spacing washer has stayed with the job; wire this washer to the arm eye just to make sure. This washer is special in that it is the right thickness to enable full load to be applied to the arm by the nut, otherwise the nut can be applying its load to the shaft shoulder rather than the arm. The washer will often have a radiused side to enable it to go readily up on to the greater diameter of the shoulder. So keep tabs on this washer, and also check that it is in fact applying the nut load directly to the arm.
One final trick of the trade will ensure that the drop arm you fit goes all the way up the taper to the limit; arrange to heat the arm in boiling water for approximately five minutes — so that it expands. Fit it to the shaft and tighten it up solid. As the arm cools and contracts it will be held more securely to the shaft.
A last thought — and of some importance — is that many drop arms and tapered spindle seats are relentlessly hammered to loosen the taper fit. This can damage the component and cause refitting problems and even service breakdowns at a later date. The mechanic should follow the manufacturer's recommended method which normally involves the use of tools to simplify the job.