Aircraft Practice Applied
Page 35
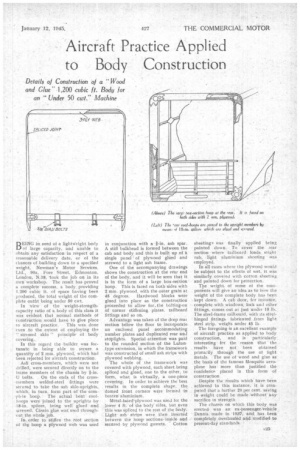
If you've noticed an error in this article please click here to report it so we can fix it.
to Body Construction BEING in need of a lightweight body of large capacity, and unable to obtain any satisfaction in respect of a reasonable delivery date, or of the chances of building down to a specified weight, Newman's Motor Services. Ltd., 90a, Fore Street, Edmonton. London, N.18, -took the job on in its own workshop. The result has proved a complete success, a body providing 1.200 cubic it. of space having been produced. the total weight of the complete outfit being under 50 cwt.
In view of the weight-strengthcapacity ratio of a body of this class it was evident that normal methods of construction would have to give place
to aircraft practice. This was done even to the extent of employing the " stressed skin " principle at body covering..
In this regard the -builder was fortunate in being able to secure a quantity of 2 mm. plywood, which had been rejected for aircraft construction.
Ash cross-members, which were not drilled, were secured directly on to the frame members of the chassis by j-in. 11 bolts. . On the ends of the cross-in embers welded-steel fittings were secured to take the ash side-uprights, which, in turn, form part of the cornph.te hoop. The actual bent roofhoops were joined to the uprights by 18-in. splices, being well glued and screwed. Casein glue was used throughout the whole job.
In order to stiffen the roof section of the hoop a plywood web was used in conjunction with a i-in, ash spar. A stiff bulkhead is formed between the cab and body and this is built up of a single panel of plywood glued and screwed to a light ash frame.
One of the accompanying drawings shows the construction at the rear end of the body, and it will be seen that it is in the form of a large . box-section hoop. This is faced on both sides with 2 mm. plywood, with the outer grain at 45 degrees. Hardwood blocks were glued into place as the construction proceeded to allow for.the bolting-on of corner stiffening. plates. tailboard fittings and so on.
Advantage was taken of the deep rent section below the floor to. incorporate an enclosed panel accommodating number plates and duplicated rear and stoplights. Special attention was paid to the rounded section of the Lutontype extension, in which the framework was constructed of small ash strips with plywood webbing.
The whole of the framework was covered with plywood, each sheet being spliced and glued, one to the other, to form, what is virtually, a one-piece covering. In order to achieve the best results in the complete shape, the domed front corners were formed in beaten aluminium.
Metal-faced-plywood was used for the lower 4 ft. of the body sides, but even this was spliced to the rest of the body. Lightash strips were then Inserted between the hoop sectionsinside and secured by plywood gussets. Cotton
sheeting' was finally applied being painted down. To cover the rear section where tailboard loads might rub, light aluminium sheeting was employed.
In all cases where the plywood would be subject to the etlects of wet, it was similarly covered with cotton sheeting and painted down for protection.
The weight. of some of the components will give an idea as to how the weight of the complete body has been kept down. A cab door, for instance. complete with windows, lock an:1 other fittings, comes out at just under 19 lb. The steel-frame tailboard, with its steel. hinged fittings fabricated from light steel strip, weighs under 45 lb.
The foregoing is an excellent example of aircraft practice as applied to body construction, and is particularly interesting for the reason that the results have not been obtained prima:ily through the use of tight metals. The use ol wood and glue as the basis of the famous Mosquito aeroplane has more than justified the confidence placed in this form of construction Despite the results which' have been achieved in this instance, it is coinputed that a further 20 per cent, saving in weight could be made:without any sacrifice in strength The chassis on which this body was erected was an ex-passeager.Vehicle Dennis made in 1937, and has been completely overhauled arid modified to present-day standards.