A MISCELLANY OF USEFUL IDEAS.
Page 31
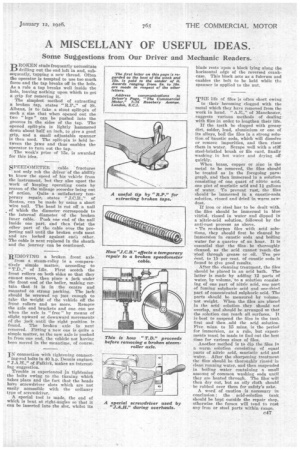
If you've noticed an error in this article please click here to report it so we can fix it.
Some Suggestions from Our Driver and Mechanic Readers.
BROKEN studs frequently necessitate drilling out the end left in and, subsequently, tapping a new thread. Often the operator is tempted to use too much force and the tap breaks off in the hole. As a rule a tap breaks well inside the hole, leaving nothing upon which to get a grip for removing it.
The simplest method of extracting a broken tap, states " R.P.," of St. Albans, is to take a stout split-pin of such a size that when opened out the two " legs " can be pushed into the grooves in the sides of the tap. The opened split-pin is lightly hammered down about half an inch, to give a good grip, and a small adjustable spanner is then used. The split-pin is held between the jaws and thus enables the operator to turn out the tap. The week's prize of 15s. is awarded for this idea.
SPEEDOMETER cable fractures
not only rob the driver of the ability to know the speed of his vehicle from the instrument, but they also upset the work of keeping operating costs by reason of the mileage recorder being out of action. Quite a satisfactory temporary repair, states " J.C.E.," of Reston, can be made by using a short wire nail. The head is cut off a nail of which the diameter corresponds to the internal diameter of the broken inner cattle. Push one end of the nail inside one part, and then fwist the other part of the cable over the projecting nail until the broken ends meet and are locked against each other. The cable is next replaced in the sheath and the journey can be continued.
REMOVING a broken front axle from a steam-roller is a comparatively simple matter, according to " T.D.," of Idle. First scotch the front rollers on both -sides so that they cannot move, then place a jack under the front end of the boiler, making certain that it is in the centre and mounted on strong packing. The jack should be screwed up just enough to take the weight of the vehicle off the front rollers and no more. Remove the axle end brackets and one can see when the axle is " free " by means of slight upward or downward movements of the jack until the right position is found. The broken axle is next removed. Fitting a new one is quite a simple matter, as the new axle is pushed in from one end, the vehicle not having been moved in the meantime, of course.
IN connection with tightening connecting-rod bolts in 40 h,p. Dennis engines, "J.A.H.," of Falkirk, makes an interesting suggestion.
Trouble Is experienced in tightening the bolts owing to the titrning which takes place and the fact that the heads have screwdriver slots which are not easily accessible with the ordinary type of screwdriver.
A special tool is made, the end of which is bent at right-angles so that it can be inserted into the slot, whilst its blade rests upon a block lying along the horizontal edge of the reversed crankcase. This block acts as a fulcrum and enables the bolt to be held while the spanner is applied to the nut.
THE life of files is often short owing to their becoming clogged with the metal which they have removed from the work in hand. " A.E.," of Manchester, suggests various methods of dealing with files in order to lengthen their life.
If the teeth be clogged with greasy dirt, solder, lead, aluminium or one of its alloys, boil the files in a strong solution of baustic soda, which will dissolve or remove impurities, and then rinse them in water. Scrape well with a stiff steel-bristled brush or file card, finally washing in hot water and drying off quickly.
When brass, copper or zinc is the metal to be removed, the files should be treated as in the foregoing paragraph, and then immersed in a solution consisting of one quart of nitric acid, one pint of muriatic acid and 13gallons of water. To prevent rust, the files should be immersed in a caustic-soda solution, rinsed and dried in warm sawdust.
If iron or steel has to be dealt with, the files should be immersed in blue vitriol, rinsed in water and dipped in a nitric-acid solution, followed by the anti-rust process as above.
s To re-sharpen files with acid solutions, they should first be cleaned by immersion in caustic soda and boiling water for a quarter of an hour. It is essential that the files • be thoroughly cleaned, as the acid cannot reach-the steel through grease or oil. Ten per cent. to 15 per cent, of caustic soda is found to give good results.
After the cleaning treatment, the files should be placed in an acid bath. The latter is made by adding 12 parts of water, by volume, to a solution consisting of one part of nitric acid, one part of fuming sulphuric acid and one-third part of concentrated sulphuric acid. The parts should be measured by volume. not weight. When the files are Placed in the acid solution they should not overlap, and should be arranged so that the solution can reach all surfaces. It is best to suspend the files in the tank first and then add the acid solution. Five mins. to 15 mins. is the period for immersion, as a rule, but experiments must be made to find out the best time for various sizes of files.
Another method is to dip the files in a warm solution consisting of equal parts of nitric acid, muriatic acid and water. After the sharpening treatment the files should be thoroughly rinsed in clean running water, and then suspended in boiling water containing a small amount of common washing soda until they are heated through. The files will then dry out, but an oily cloth should. be rubbed over them for safety's sake.
A word of caution is necessary in conclusion : the acid-solution tank should be kept outside the repair shop, otherwise the fumes will tend to rust any iron or steel parts within range.