• It was not that long ago that the general
Page 45
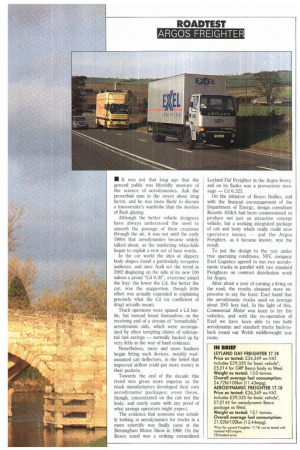
Page 46
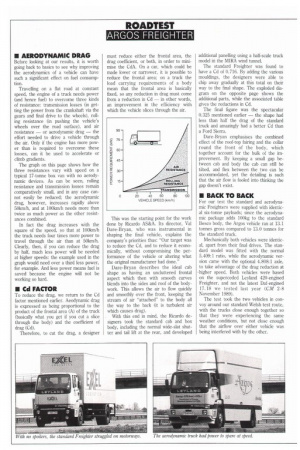
Page 47
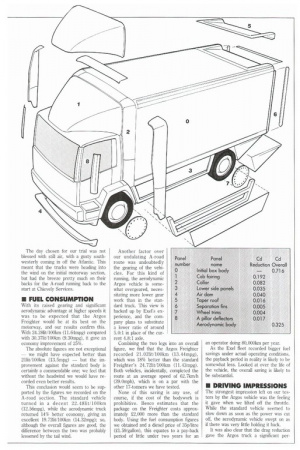
Page 48
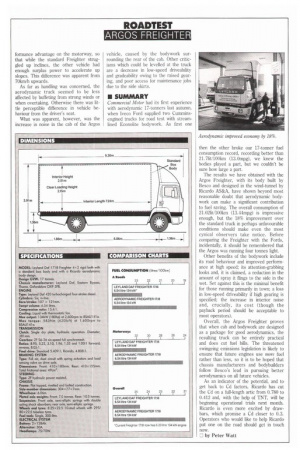
If you've noticed an error in this article please click here to report it so we can fix it.
public was blissfully unaware of the science of aerodynamics. Ask the proverbial man in the street about drag factor, and he was more likely to discuss a transvestite's wardrobe than the niceties of flush glazing.
Although the better vehicle designers have always understood the need to smooth the passage of their creations through the air, it was not until the early 1980s that aerodynamics became widely talked about, as the marketing whizz-kids began to exploit a new set of buzz words.
In the car world the idea of slippery body shapes found a particularly receptive audience, and once Audi set the trend in 1982 displaying on the side of its new 100 saloon a proud "Cd 0.30", everyone joined the fray: the lower the Cd, the better the car, was the suggestion, though little effort was actually expended in explaining precisely what the Cd (or coefficient of drag) actually meant.
Truck operators were spared a Cd battle, but instead found themselves on the receiving end of a stream of "remarkable" aerodynamic aids, which were accompanied by often tempting claims of substantial fuel savings — normally backed up by very little in the way of hard evidence.
Nonetheless, more and more hauliers began fitting such devices, notably roofmounted cab deflectors, in the belief that improved airflow could put more money in their pockets.
Towards the end of the decade this trend was given more impetus as the truck manufacturers developed their own aerodynamic packages; even these, though, concentrated on the cab not the body, and rarely came with any proof of what savings operators might expect.
The evidence that someone was actually looking at aerodynamics for trucks in a more scientific way finally came at the Birmingham Motor Show in 1988. On the Besco stand was a striking streamlined
Leyland Daf Freighter in the Argos livery, and on its flanks was a provocative message — Cd 0.325.
On the initiative of Besco Bodies, and with the financial encouragement of the Department of Energy, design consultant Ricardo AS&A had been commissioned to produce not just an attractive concept vehicle, but a working integrated package of cab and body which really could save operators money — and the Argos Freighter, as it became known, was the result.
To put the design to the test under true operating conditions, NFC company Exel Logistics agreed to run two aerodynamic trucks in parallel with two standard Freighters on contract distribution work for Argos.
After about a year of earning a living on the road, the results obtained were impressive to say the least: Exel found that the aerodynamic trucks used on average about 20% less fuel. In the light of this, Commercial Motor was keen to try the vehicles, and with the co-operation of Exel we have been able to run both aerodynamic and standard trucks back-toback round our Welsh middleweight test route.
• AERODYNAMIC DRAG
Before looking at our results, it is worth going back to basics to see why improving the aerodynamics of a vehicle can have such a significant effect on fuel consumption.
Travelling on a flat road at constant speed, the engine of a truck needs power (and hence fuel) to overcome three kinds of resistance: transmission losses (in getting the power from the crankshaft via the gears and final drive to the wheels), rolling resistance (in pushing the vehicle's wheels over the road surface), and air resistance — or aerodynamic drag — the effort needed to drive a vehicle through the air. Only if the engine has more power than is required to overcome these losses, can it be used to accelerate or climb gradients.
The graph on this page shows how the three resistances vary with speed on a typical 17-tonne box van with no aerodynamic devices. As can be seen, rolling resistance and transmission losses remain comparatively small, and in any case cannot easily be reduced; the aerodynamic drag, however, increases rapidly above 50km/h, and at 100km/h needs more than twice as much power as the other resistances combined.
In fact the drag increases with the square of the speed, so that at 100km/h the truck needs four times more power to travel through the air than at 50kmfh. Clearly, then, if you can reduce the drag by half, much less power will be needed at higher speeds: the example used in the graph would need over a third less power, for example. And less power means fuel is saved because the engine will not be working so hard.
• Cd FACTOR
To reduce the drag, we return to the Cd factor mentioned earlier. Aeodynamic drag is expressed as being proportional to the product of the frontal area (A) of the truck (basically what you get if you cut a slice through the body) and the coefficient of drag (Cd).
Therefore, to cut the drag, a designer must reduce either the frontal area, the drag coefficient, or both, in order to minimise the CdA. On a car, which could be made lower or narrower, it is possible to reduce the frontal area; on a truck the load carrying requirements of a body mean that the frontal area is basically fixed, so any reduction in drag must come from a reduction in Cd — in other words, an improvement in the efficiency with which the vehicle slices through the air.
This was the starting point for the work done by Ricardo AS&A. Its director, Val Dare-Bryan, who was instrumental in shaping the final vehicle, explains the company's priorities thus: "Our target was to reduce the Cd, and to reduce it economically, without compromising the performance of the vehicle or altering what the original manufacturer had done."
Dare-Bryan describes the ideal cab shape as having an uncluttered frontal aspect which then with smooth curves blends into the sides and roof of the bodywork. This allows the air to flow quickly and smoothly over the front, keeping the stream of air "attached" to the body all the way to the back (it is turbulent air which causes drag).
. With this end in mind, the Ricardo designers took the standard cab and box body, including the normal wide-slat shutter and tail lift at the rear, and developed additional panelling using a half-scale truck model in the MIRA wind tunnel.
The standard Freighter was found to have a Cd of 0.716. By adding the various mouldings, the designers were able to chip away gradually at this total on their way to the final shape. The exploded diagram on the opposite page shows the additional parts, while the associated table gives the reductions in Cd.
The final figure was the spectacular 0.325 mentioned earlier — the shape had less than half the drag of the standard truck and amazingly had a better Cd than a Ford Sierra.
Dare-Bryan emphasises the combined effect of the roof-top fairing and the collar round the front of the body, which together account for the bulk of the improvement. By keeping a small gap between cab and body the cab can still be tilted, and flex between the two can be accommodated, yet the detailing is such that the air flow is fooled into thinking the gap doesn't exist.
• BACK TO BACK
For our test the standard and aerodynamic Freighters were supplied with identical six-tonne payloads; since the aerodynamic package adds 100kg to the standard Besco body, the Argos vehicle ran at 13.1 tonnes gross compared to 13.0 tonnes for the standard truck.
Mechanically both vehicles were identical, apart from their final drives. The standard model was fitted with the normal 5.409:1 ratio, while the aerodynamic version came with the optional 4.808:1 axle, to take advantage of the drag reduction at -higher speed. Both vehicles were based on the superceded Leyland 420-engined Freighter, and not the latest Daf-engined 17.18 we tested last year (CM 2-8 November 1989).
The test took the two vehicles in convoy around our standard Welsh test route, with the trucks close enough together so that they were experiencing the same weather conditions, but not close enough that the airflow over either vehicle was being interfered with by the other. The day chosen for our trial was not blessed with still air, with a gusty southwesterly coming in off the Atlantic. This meant that the trucks were heading into the wind on the initial motorway section, but had the breeze pretty much on their backs for the A-road running back to the start at Chievely Services.
• FUEL CONSUMPTION
With its raised gearing and significant aerodynamic advantage at higher speeds it was to be expected that the Argos Freighter would be at its best on the motorway, and our results confirm this. With 24. 281it/100km (11. 64mpg) compared with 30.371it/100km (9.30mpg), it gave an economy improvement of 25%.
The absolute figures are not exceptional — we might have expected better than 211it/100km (13.5mpg) — but the improvement against the standard body is certainly a commendable one; we feel that without the headwind we would have recorded even better results.
This conclusion would seem to be supported by the figures we recorded on the A-road section. The standard vehicle turned in a decent 22.481it/100km (12.56mpg), while the aerodynamic truck returned 14% better economy, giving an excellent 19.721ft/100km (14.32mpg); so, although the overall figures are good, the difference between the two was probably lessened by the tail wind. Another factor over our undulating A-road route was undoubtedly the gearing of the vehicles. For this kind of running, the aerodynamic Argos vehicle is somewhat overgeared, necessitating more lower gear work than in the standard truck. This view is backed up by Exel's experience, and the company plans to substitute a lower ratio of around 5.0:1 in place of the current 4.8;1 axle.
Combining the two legs into an overall figure, we find that the Argos Freighter recorded 21.0214/100km (13.44mpg), which was 18% better than the standard Freighter's 24.721it/100km (11.43mpg). Both vehicles, incidentally, completed the route at an average speed of 62.7km/1 (39.0mph), which is on a par with the other 17-tonners we have tested.
None of this saving is any use, of course, if the cost of the bodywork is prohibitive. Besco estimates that the package on the Freighter costs approximately .4:2,000 more than the standard body. Using the fuel consumption figures we obtained and a diesel price of 35p/litre (21.59/gallon), this equates to a pay-hack period of little under two years for an
an operator doing 80,000km per year.
As the Exel fleet recorded bigger fuel savings under actual operating conditions, the payback period in reality is likely to be somewhat less. Looked at over the life of the vehicle, the overall saving is likely to be substantial.
• DRIVING IMPRESSIONS
The strongest impression left on our testers by the Argos vehicle was the feeling it gave when we lifted off the throttle. While the standard vehicle seemed to slow down as soon as the power was cut off, the aerodynamic vehicle swept on as if there was very little holding it back.
It was also clear that the drag reduction gave the Argos truck a significant per formance advantage on the motorway, so that while the standard Freighter struggled up inclines, the other vehicle had enough surplus power to accelerate up slopes. This difference was apparent from 70km/h upwards.
As far as handling was concerned, the aerodynamic truck seemed to be less affected by buffeting from strong winds or when overtaking. Otherwise there was little perceptible difference in vehicle behaviour from the driver's seat.
What was apparent, however, was the increase in noise in the cab of the Argos vehicle, caused by the bodywork surrounding the rear of the cab. Other criticisms which could be levelled at the truck are a decrease in low-speed driveability and gradeability owing to the raised gearing, and poor access for maintenance jobs due to the side skirts.
• SUMMARY
Commercial Motor had its first experience with aerodynamic 17-tonners last autumn. when lveco Ford supplied two Cumminsengined trucks for road test with streamlined Econolite bodywork. As first one
then the other broke our 17-tonner fuel consumption record, recording better than 21.71it/100km (13.0mpg), we knew the bodies played a part, but we couldn't be sure how large a part.
The results we have obtained with the Argos Freighter, with its body built by Besco and designed in the wind-tunnel by Ricardo AS&A, have shown beyond most reasonable doubt that aerodynamic bodywork can make a significant contribution to fuel saving. The overall consumption of 21.02lit1100km (13.44mpg) is impressive enough, but the 18% improvement over the standard truck in perhaps unfavourable conditions should make even the most cynical observers take notice. Before comparing the Freighter with the Fords, incidentally, it should be remembered that the Argos was running four tonnes light.
Other benefits of the bodywork include its road behaviour and improved performance at high speed; its attention-grabbing looks and, it is claimed, a reduction in the amount of spray it flings to the side in the wet. Set against this is the minimal benefit for those running primarily in town; a loss in low-speed driveability if high gearing is specified; the increase in interior noise and, crucially, its cost (though the payback period should be acceptable to most operators).
Overall, the Argos Freighter proves that when cab and bodywork are designed as a package for good aerodynamics, the resulting truck can be entirely practical and does cut fuel bills. The threatened swingeing emissions legislation is likely to ensure that future engines use more fuel rather than less, so it is to be hoped that chassis manufacturers and bodybuilders follow Besco's lead in pursuing better aerodynamics on all future vehicles.
As an indicator of the potential, and to get back to Cd factors, Ricardo has cut the Cd on a full-length artic from 0.780 to 0.412 and, with the help of TNT, will be beginning operational trials next month. Ricardo is even more excited by drawbars, which promise a Cd closer to 0.3. Operators who would like to help Ricardo put one on the road should get in touch now.
by Peter Watt