FAST FORWARD
Page 146
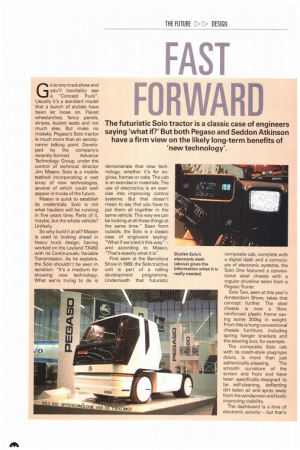
Page 147
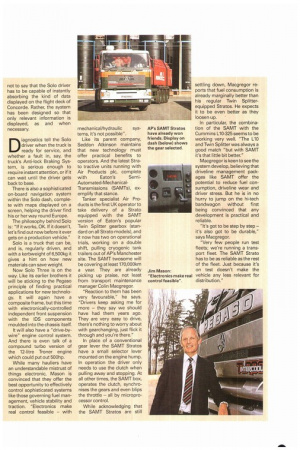
If you've noticed an error in this article please click here to report it so we can fix it.
The futuristic Solo tractor is a classic case of engineers saying 'what if?' But both Pegaso and Seddon Atkinson have a firm view on the likely long-term benefits of 'new technology'.
Go to any truck show and you'll inevitably see a "Concept Truck". Usually it's a standard model that a bunch of stylists have been let loose on. Flared wheelarches, fancy panels, stripes, bucket seats and not much else. But make no mistake, Pegaso's Solo tractor is much more than an aerodynamic talking point. Developed by the company's
recently-formed Advance Technology Group, under the control of technical director Jim Mason, Solo is a mobile testbed incorporating a vast array of new technologies, several of which could well appear in trucks of the future.
Mason is quick to establish its credentials. Solo is not what hauliers will be running in five years time. Parts of it, maybe, but the whole vehicle? Unlikely.
So why build it at all? Mason is used to looking ahead in heavy truck design, having worked on the Leyland TX450 with its Continuously Variable Transmission. As he explains, the Solo shouldn't be seen in isolation: "It's a medium for showing new technology. What we're trying to do is demonstrate that new technology, whether it's for engines, frames or cabs. The cab is an exercise in materials. The use of electronics is an exercise into improving control systems. But that doesn't mean to say that you have to put them all together in the same vehicle. This way we can be looking at all these things at the same time." Seen from outside, the Solo is a classic case of engineers saying: "What if we tried it this way" — and according to Mason, "That's exactly what it is".
First seen at the Barcelona Show in 1989, the Solo tractive unit is part of a rolling development programme. Underneath that futuristic composite cab, complete with a digital dash and a cornucopia of electronic systems, the Solo One featured a conventional steel chassis with a regular driveline taken from a Pegaso Ironer.
Solo Two, seen at this year's Amsterdam Show, takes that concept further. The steel chassis is now a fibrereinforced plastic frame saving some 200kg in weight. From this is hung conventional chassis furniture, including spring hanger brackets and the steering box, for example.
The composite Solo cab with its coach-style plug-type doors, is more than just asthectically-pleasing. The smooth curvature of the screen and front end have been specifically-designed to be self-cleaning, deflecting dirt laden air and spray away from the windscreen and body improving visibility.
The dashboard is a hive of electronic activity — but that's not to say that the Solo driver has to be capable of instantly absorbing the kind of data displayed on the flight deck of Concorde. Rather, the system has been designed so that only relevant information is displayed, as and when necessary.
D'agnostics tell the Solo driver when the truck is ready for service, and whether a fault in, say, the truck's Anti-lock Braking System, is serious enough to require instant attention, or if it can wait until the driver gets back to base.
There is also a sophisticated on-board navigation system within the Solo dash, complete with maps displayed on a screen, helping the driver find his or her way round Europe.
The philosophy behind Solo is: "If it works, OK. If it doesn't, let's find outflow before it ever gets on a production vehicle."
Solo is a truck that can be, and is, regularly driven, and with a kerbweight of 6,500kg it gives a hint on how new materials can save weight.
Now Solo Three is on the way. Like its earlier brothers it will be sticking to the Pegaso principle of finding practical applications for new technology. It will again have a composite frame, but this time with electronically-controlled independent front suspension with the IDS components moulded into the chassis itself.
It will also have a "drive-bywire" engine control system. And there is even talk of a compound turbo version of the 12-litre Troner engine which could put out 500hp.
While many hauliers have an understandable mistrust of things electronic, Mason is convinced that they offer the best opportunity to effectively control sophisticated systems like those governing fuel management, vehicle stability and traction. "Electronics make real control feasible — with mechanical/hydraulic sys tems, it's not possible".
Like its parent company, Seddon Atkinson maintains that new technology must offer practical benefits to operators. And the latest Strato tractive units running with Air Products plc, complete
with Eaton's SemiAutomated-Mechanical
Transmissions (SAMTs), exemplify that stance.
Tanker specialist Air Products is the first UK operator to take delivery of a Strato equipped with the SAMT version of Eaton's popular Twin Splitter gearbox (standard on all Strato models), and it now has two on operational trials, working on a double shift, pulling cryogenic tank trailers out of AP's Manchester site. The SAMT twosome will be covering at least 170,000km a year. They are already picking up praise, not least from transport maintenance manager Colin Macgregor.
"Reaction to them has been very favourable," he says. "Drivers keep asking me for more — they say we should have had them years ago. They are very easy to drive, there's nothing to worry about with gearchanging, just flick it through and you're there."
In place of a conventional gear lever the SAMT Stratos have a small selector lever mounted on the engine hump. In operation the driver only needs to use the clutch when pulling away and stopping. At all other times, the SAMT box, operates the clutch, synchronises the gears and even blips the throttle — all by microprocessor control.
While acknowledging that the SAMT Stratos are still settling down, Macgregor reports that fuel consumption is already marginally better than his regular Twin Splitterequipped Stratos. He expects it to be even better as they loosen up.
In particular, the combination of the SAMT with the Cummins L10-325 seems to be working very well. "The L10 and Twin Splitter was always a good match "but with SAMT it's that little bit better."
Macgregor is keen to seethe system develop, believing that driveline management packages like SAMT offer the potential to reduce fuel consumption, driveline wear and driver stress. But he is in no hurry to jump on the hi-tech bandwagon without first being convinced that any development is practical and reliable.
"It's got to be step by step — it's also got to be durable," says Macgregor.
"Very few people run test fleets; we're running a transport fleet, The SAMT Strato has to be as reliable as the rest of the fleet, Just because it's on test doesn't make the vehicle any less relevant for distribution."