FOR SMOOTH RUNNING AT HIGH SPEEDS.
Page 68
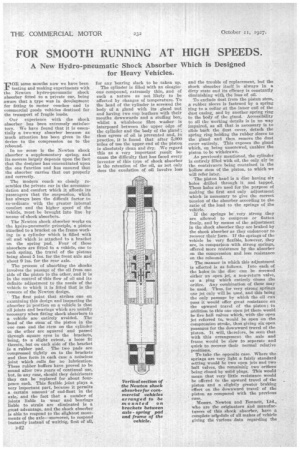
Page 69
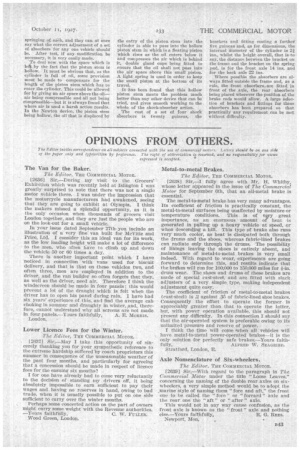
If you've noticed an error in this article please click here to report it so we can fix it.
A New Hydro-pneumatic Shock Absorber Which is Designed for Heavy Vehicles.
FOR some months now we have been testing and making experiments with the Newton hydro-pneumatic shock absorber fitted to a private car, being aware that a type was in development for fitting to motor coaches and to commercial goods vehicles destined for the transport of fragile loads.
Our experience with the shock absorber has been extremely satisfactory. We have found that it is essentially a two-way absorber because as much attention has been given in the device to the compression as to the rebound.
In no sense is the Newton shock absorber a supplementary spring, and its success largely depends upon the fact that the designer has concentrated upon the one function and has ensured that the absorber carries that out properly and correctly.
The modern coach so closely resembles the private ear in the accommodation and comfort which it affords its passengers that the suspension, which has always been the difficult factor to co-ordinate with the greater internal comfort and the higher speed of the vehicle, must be brought into line by means of shock absorbers.
The Newton shock absorber works on the hydro-pneumatic principle, a piston attached to a bracket on the frame working in a cylinder which is filled with oil and which is attached to a bracket on the spring pad. Four of these absorbers are fitted to a vehicle, one to each spring, the travel of the pistons being about 5 ins, for the front axle and about 9 ins, for the rear axle.
The process of absorbing the shocks involves the passage of the oil from one side of the piston to the other, and it is in the control of this flow of oil and its definite adjustment to the needs of the vehicle to which it is fitted that is the essence of the Newton design.
The first point that strikes one on examining this design and inspecting the absorber in position on a vehicle is that all joints and bearings which are usually necessary when fitting shock absorbers to a vehicle are entirely avoided. The head of the stem of the piston in the one case and the stem on the cylinder in the other are squared and passed through square eyes in the brackets, being, to a slight extent, a loose fit therein, but on each side of the bracket is a rubber pad. The two pads are compressed tightly on to the brackets and thus form in each case a noiseless joint which calls for no lubrication. These rubber buffers have proved to be sound after two years of continual use, but, in any case, should they deteriorate they can be replaced for about fourpence each. This flexible joint plays a very important part, because it permits a certain amount of end-float in the axle, and the fact that a number of joints liable to wear and bearings liable to strain are eliminated is a great advantage, and the shock absorber is able to respond to the slightest movements of the axle—moreover, to respond instantly instead of waiting, first of all, for any bearing slack to be taken up.
The cylinder is filled with an oleaginous compound, extremely thin, and of such a nature as not likely to be affected by changes of temperature. To the head of the cylinder is screwed the body of a gland with its gland nut and having two cup leathers with their mouths downwards and a stuffing box, whilst a whalebone fibre washer is interposed between the upper edge of the cylinder and the body of the glands thus egress of oil is prevented and, in practice, it is found that after 5,000 miles of use the upper end of the piston is absolutely clean and dry. We regard this as a very important result because the difficulty that has faced every inventor of this type of shock absorber is the retention of the oil, as not only does the exudation of oil involve loss and the trouble of replacement, but the shock absorber itself is always in a dirty state and its efficacy is constantly diminishing with the loss of oil.
To exclude dust from the piston stem, a rubber sleeve is fastened by a spring ring to a collar at the inner end of the dust easing, and by another spring ring to the body of the gland. Accessibility to all the working details is in no way impaired, as all that is necessary is to slide back the dust cover, detach the spring ring holding the rubber sleeve to the gland and then remove the dust cover entirely. This exposes the gland which, on being unscrewed, enables the piston to be withdrawn. As previously mentioned, the cylinder is entirely filled with oil, the only air in the contrivance being contained in the hollow stem of the piston, to which we will refer later.
The piston head is a disc having six holes drilled through it and tapped. These holes are used for the purpose of making the first and only adjustment which is necessary to give the correct tension of the absorber according to the ratio of the load to the springs of the vehicle.
If the springs be very strong they are allowed to compress or flatten freely, and by means of the adjustment in the shock absorber they are braked by the shock absorber as they endeavour to recover their form. If the springs of the vehicle be very flexible, however, they are, in comparison with strong springs, offered more resistance by the absorber on the compression and less resistance on the rebound.
The manner in which this adjustment is effected is as follows. Into each of the holes in the disc can be screwed either an open jet, a non-return valve, or a plug which entirely doses the orifice. Any combination of these may be used. Thus, for very strong springs one jet only will be used, and this being the only passage by which the oil can pass it would offer great resistance on the upward travel of the piston ; in addition to this one open jet there would be five ball valves which, -with the open jet referred to, would be open on the compression stroke, thus giving six open passages for the downward travel of the piston. It will, therefore, be seen that with this arrangement the axle and frame would be slow to separate and quick to recover their normal relative positions.
To take the opposite case. Where the sprisgs are very light a fairly standard setting would be two open jets and two ball valves, the remaining two orifices being closed by solid plugs. This would mean that very little resistance would be offered to the upward travel of the piston and a slightly greater braking effect on the downward travel of the piston as compared with the previous case.
Messrs. Newton and Bennett, Ltd., who are the originators and manufacturers of this shock absorber, have a complete schedule of all makes of vehicle giving the various data regarding the
springing of .each, and they can at once say what the correct adjustment of a set of absorbers for any one vehicle should be. After test, if any modification be necessary, it is very easily made.
To deal now with the space which is le* by the fact that the piston stem is hollow. It must be obvious that, as the cylinder is full of oil, some provision must be made to compensate for the length of the piston stem which has to enter the cylinder. This could be allowed for by giving an air space above the oil— air being compressible and oil not being compressible—but it is always found that where air is used a harsh action results. In the Newton device, the piston stern being hollow, the oil that is displaced by the entry of the piston stern into the cylinder is able to pass into the hollow pistott stem in which is a floating piston which rises as the oil enters below it and compresses the air which is behind it, double gland cups being fitted to ensure that the oil shall not pass into the air space ibove this small piston. A light spring is used in order to keep the small piston at the bottom of its travel.
It-has been found that this hollow piston stem meets the problem much better than any other device that can be tried, and gives smooth working to the whole of the shock-absorber action.
The cost of a set of four shock Asorbers is twenty guineas, the brackets and fitting costing a further five guineas and, as for dimensions, the internal diameter of the cylinder is 21 ins., whilst the height overall, that is-to say, the distance between the bracket on the frame and the bracket on the spring pad, is for the front axle 14 ins, and for the back axle 22 ins.
Where Possible the absorbers are always fitted outside the frame and, as a rule, the front absorbers:rare fitted in front of the axle, the rear absorbers being placed wherever the position of the brake rods would allow. A large selection of brackets and fittings for these absorbers has been prepared so that practically any requirement eau be met without difficulty.