The Ideal
Page 109
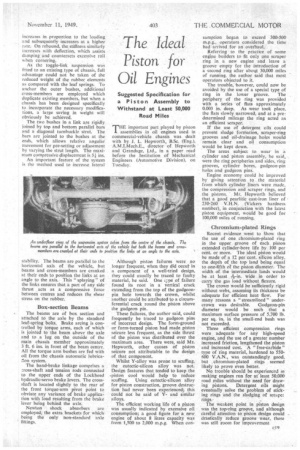
If you've noticed an error in this article please click here to report it so we can fix it.
Piston for Oil Engines
Suggested Specification for a Piston Assembly to Withstand at Least 50,000 Road Miles
THE important part played by piston 4. assemblies in oil engines used in commercial-vehicle chassis was dealt with by J. L. Hepworth, B.Sc. (Eng.). A.M.I.Mech.E., director of Hepworth and Grandage, Ltd., in a paper read before the Institution of Mechanical Engineers (Automotive Division), on Tuesday.
Although piston failures were no longer frequent, when they did omit in a component of a well-tried design, they could usually he traced to faulty material, he said. One iype of failure found its root in a vertical crack extending from the top of the gudgeonpin hole towards the crown, whilst another could be attributed to a circumferential crack round the piston above the gudgeon pin.
These failures, the author said, could frequently be traced to gudgeon pins of incorrect design. The form-ground or form-turned piston had made piston seizure less frequent, as the side thrust of the piston was distributed over the maximum area. There were, said Mr. Hepworth, other causes of piston seizure not attributable to the design of that component.
Whilst Y-alloy was prone to scuffing, the eutectic-silicon alloy was not. Design features that tended to keep the -piston cool would help to reduce scuffing. Using eutectic-silicon alloy for piston construction, groove destruction had never been experienced; this could not be said of Yand similar alloys.
The efficient working life of a piston was usually indicated by excessive oil consumption; a good figure for a new engine of about 8 litres capacity was from 1,500 to 2,000 m.p.g. When con
sumption began to exceed 300-500 m.p.g.. operators considered the time had arrived for an overhaul, Referring to the practice of some engine builders to fit only one scraper ring in a new engine and leave a groove empty for the introduction of a second ring after about 30,000 miles of running, the author said that most operators objected to it.
The trouble, however, could now be avoided by the use of a special type of ring in the lower groove. The periphery of the ring was provided with a series of flats approximately 0.003 in. deep. As wear took place. the flats slowly narrowed, and at a predetermined mileage the ring acted as an efficient scraper.
If the use of detergent oils could prevent sludge formation, scraper-ring grooves and oil-drainage holes would remain clear and oil consumption would be kept down.
The areas subject to wear in a cylinder and piston assembly, he said, were the ring peripheries and sides, ring grooves, cylinder bores, gudgeon-pin holes and gudgeon pins.
Engine economy could be improved by giving attention to the material from which cylinder liners were Made, . the compression and scraper rings, and the pistons. Mr. Hepworth believed that a good pearlitic cast-iron liner of 230-260 V.H.N. (Vickers hardness number), in conjunction with the latest piston equipment, would be good for 100,000 miles of running.
Chromium-plated Rings
Recent evidence went to.Allow that the use of one chromium-plated ring in the upper groove of each. piston extended cylinder-bore life .by 100 per cent, or more. The ideal piston would be made of a 12 per cent. silicon alloy, the depth of the top land being equal to one-fifth of the piston diameter. The width of the intermediate lands would be at least wide . in order to carry the gas load without flexure.
The crown would .be sufficiently rigid without webs, assuming its thickness be adequate for efficient heat flow. For many reasons a "streamlined" undercrown was desirable. Gudgeon-pin diameter would be such that a maximum surface pressure of 5,700 lb. per sq. in. in the small-end bush was not exceeded.
Three efficient compression rings were adequate for any high-speed engine, and the use of a greater number increased friction, lengthened the piston and increased cost. A "free-carbide" type of ring material, hardened to 550600 V.A.N., was outstandingly good. but . chromium-plated rings seemed likely to prove even better.
No trouble should be experienced in making engines run for at least 50,000 road miles without the "need for drawing pistons. Detergent oils might eventually solve the problem of sticking rings and the sludging of serapet rings, The weakest point in piston design was the top-ring groove, and although careful attention to piston design could drastically reduce groove wear, there was still room for improvement.