THERMO-CHEMICAL ASI IS OF GASEOUS FUELS
Page 30
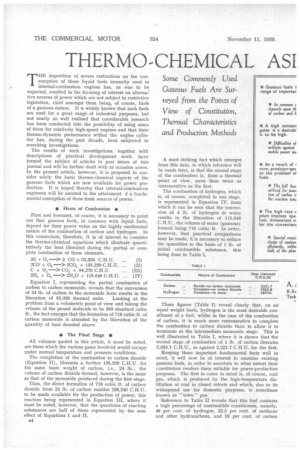
Page 31
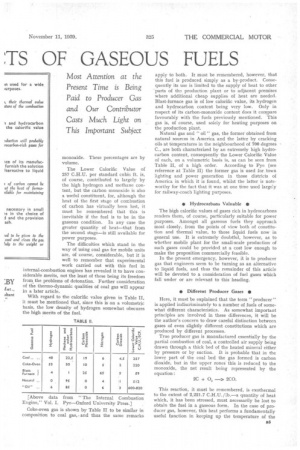
Page 32
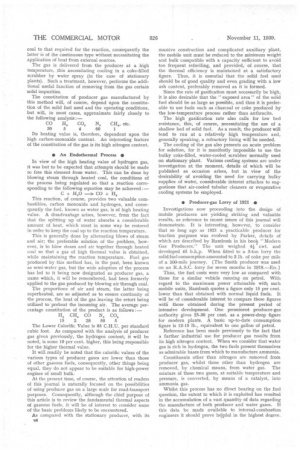
If you've noticed an error in this article please click here to report it so we can fix it.
THE imposition of severe restrictions on the consumption of those liquid fuels normally used in
..internal-combustion engines has, as was to be expected, resulted in the focusing of interest on alterna: five sources of power which are not subject to restrictive legislation, chief amongst them being, of course, fuels of a gaseous nature. It is widely known that such fuels are used for a great range of industrial purposes, but not nearly so well realized that considerable research has been conducted into the possibility of using some of them for relatively high-speed engines and that their thermo-dynamic performance within the engine cylinder has, during the past decade, been subjected to searching investigations. '
The results of such investigations, together with descriptions of practical development work, have formed the subject of articles in past issues of tnis journal and will be further dealt with as occasion arises. In the present article, however, it is proposed to consider solely the basic thermo-chemical aspects of the gaseous fuels which are now available for power production. It is hoped thereby that internal-combustion engineers will be assisted to the attainment d a fundamental conception of these fresh sources of power.
• Heats of Combustion •
First and foremost, of course, it is necessary to point out that gaseous fuels, in common with liquid fuels, depend for their power value on the highly exothermal nature of the combustion of carbon and hydrogen. In this connection, therefore, it is of interest to consider the thermo-chemical equations which illustrate quantitatively the heat liberated during the partial or complete combustion of these elements.
2C + 02—> 2 CO + 53,320 C.H.U. ... 2C0 405—>2CO2 + 135,220 C.H.U. ...
C + 02—> CO2 + 94,270 C.H.U. ...
211, + 02 —> 211,0 + 115,640 C.H.U. ...
Equation I, representing the partial combustion of carbon to carbon monoxide, reveals that the conversion of 24 lb. of carbon to the monoxide form results in the liberation of 53,320 thermal units. Looking at the problem from a volumetric point of view and taking the volume of the pound molecule to be 359 standard cubic ft., the fact emerges that the formation of 718 cubic ft. of carbon monoxide is attended by the liberation of the quantity of heat denoted above, • The Final Stage • All volumes quoted in this article, it must be noted, are those which the various gases involved would occupy under normal temperature and pressure conditions.
The completion of the combustion to carbon dioxide (Equation II), liberates a further 135,220 C.H.U. for the same basic weight of carbon, i.e., 24 lb.; the volume of carbon dioxide formed, however, is the same as that of the monoxide produced during the first stage.
Thus, the direct formation of 718 cubic ft. of carbon dioxide from 24 lb. of carbon enables 188,540 C.H.U. to be made available for the production of power, this reaction being represented in Equation III, where it must be noted, however, that the quantities of reacting substances are half of those represented by the sum effect of Equations I and II.
B4 A most striking fact which emerges from this data, to which reference will be made later, is that the second stage of the combustion is, from a thermal point of view, more than twice as remunerative as the first.
The combustion of hydrogen, which is, of course, completed in one stage, is represented in Equation IV, from which it can be seen that the conversion of 4 lb. of hydrogen to water results in the liberation of 115,640 C.H.U., the volume of water (gaseous) formed being 718 cubic ft. In order, however, that practical comparisons may be made, it is necessary to reduce the quantities to the basis of 1 lb. of initial combustible substance, this being done in Table I.
These figures (Table I) reveal clearly that, on an equal weight basis, hydrogen is the most desirable constituent of a fuel, whilst in the case of the combustion of carbon, it is much more remunerative to complete the combustion to carbon dioxide than to allow it to terminate at the intermediate monoxide stage. This is well illustrated in Table I, where it is shown that the second stage of combustion of 1 lb. of carbon liberates 5,634.1 C.H.U., as against 2,221.7 C.H.U. for the first.
Keeping these important fundamental facts well in mind, it will now be of interest to examine existing gaseous fuels, in order to ascertain to what extent their constitution renders them suitable for power-production purposes. The first to come to mind is, of course, coal gas, which is produced by the high-temperature distillation of coal in closed retorts and which, due to its widespread use for domestic purposes, is sometimes known as " town " gas.
Reference to Table II reveals that this fuel contains a high percentage of combustible constituents, namely, 48 per cent. of hydrogen, 22.5 per cent, of methane and other hydrocarbons, and 19 per cent. of carbon monoxide. These percentages are by volume.
The Lower Calorific Value of 257 C.H.U. per standard cubic ft. is, of course, contributed to largely by the high hydrogen and methane content, but the carbon monoxide is also a useful constituent, for, although the heat of the first stage of combustion of carbon has virtually been lost, it must be remembered that this is inevitable if the fuel is to be in the gaseous condition. In any case the greater quantity of heat—that from the second_ stage—is still available for power purposes.
The difficulties which stand in the way of using coal gas for mobile units are, of course, considerable, but it is well to remember that experimental work carried out with this fuel in internal-combustion engines has revealed it to have considerable merits, not the least of these being its freedom from the problems of detonation. Further consideration of the thermo-dynamic qualities of coal gas will appear in a later article.
With regard to the calorific value given in Table II, it must be mentioned that, since this is on a volumetric basis, the low density of hydrogen somewhat obscures the high merits of the fuel.
[Above data from " The Internal Combustion Engine," Vol. I. Pye—Oxford University Press.]
Coke-oven gas is shown by Table H to be similar in composition to coal gas, • and thus the same remarks apply to both. It must be remembered, however, that this fuel is produced simply as a by-product. Consequently its use is limited to the supply of heat to other parts of the production plant or to adjacent premises where additional cheap supplies of heat are needed. Blast-furnace gas is of low calorific value, its hydrogen and hydrocarbon content being very low. Only in respect of its carbon-monoxide content does it compare favourably with the fuels previously mentioned. This gas is, of course, used solely for heating purposes on the production plant.
Natural gas and " oil " gas, the former obtained from natural sources in America and the latter by cracking oils at temperatures in the neighbourhood of 700 degrees C., are both characterized by an extremely high hydrocarbon content, consequently the Lower Calorific Value of each, on a volumetric basis is, as can be seen from Table II, of a high order. According to Pye (see reference at Table H) the former gas is used for town lighting and power generation in those districts of America in which it is found, whilst the latter is noteworthy for the fact that it was at one time used largely for railway-coach lighting purposes.
• Hydrocarbons Valuable • The high calorific values of gases rich in hydrocarbons renders them, of course, particularly suitable for power purposes. Amongst all gaseous fuels they approach most closely, from the points of view both of constitution and thermal value, to those liquid fuels now in general use. It is extremely doubtful, however, as to whether mobile plant for the small-scale productionof such gases could be provided at a cost low enough to make the proposition commercially feasible.
In the present emergency, however, it is to producer gas that engineers seem to be turning as an alternative to liquid fuels, and thus the remainder of this article will be devoted to a consideration of fuel gases which fall under or are relevant to this heading.
• Different Producer Gases • Here, it must be explained that the term " producer " is applied indiscriminately to a number of fuels of somewhat different characteristics. As somewhat important principles are involved in these differences, it will be the author's concern to draw careful distinction between gases of even slightly different constitutions which are produced by different processes.
True producer gas is manufactured essentially by the partial combustion of coal, a controlled air supply being drawn through a thick bed of the heated mineral either by pressure or by suction. It is probable that in the lower part of the coal bed the gas formed is carbon dioxide, but in the upper zones this is reduced to the monoxide, the net result being represented by the equation :
2C + 02 —> 2C0.
This reaction, it must be remembered, is exothermal to the extent of 2,221.7 C.H.U. / lb.—a quantity of heat which, it has been stressed, must necessarily be lost to obtain the fuel in a gaseous form. In the case of producer gas, however, this heat performs a fundamentally useful function in keeping up the temperature of the coal to that required for the reaction, consequently the latter is of the continuous type without necessitating the application of heat from external sources.
The gas is delivered from the producer at a high temperature, this necessitating cooling in a coke-filled scrubber by water spray (in the case of stationary plants). Such a treatment, however, performs the additional useful function of removing from the gas certain solid impurities.
The constitution of producer gas manufactured by this method will, of course, depend upon the constitution of the solid fuel used and the operating conditions, but will, in most cases, approximate fairly closely to the following analysis:—
CO 11, CO2 N, CH4, etc.
30 5 4 60 1 Its heating value is, therefore, dependent upon the high carbon-monoxide content. An interesting feature of the constitution of the gas is its high nitrogen content.
• An Endothermal Process •
In view of the high heating value of hydrogen gas, it was but to be expected that attempts should be made to free this element from water. This can be done by blowing steam through heated coal, the conditions of the process being regulated so that a reaction corresponding to the following equation may be achieved :—
C 1120 —> CO + H,
This reaction, of course, provides two valuable combustibles, carbon monoxide and hydrogen, and consequently the fuel, known as water gas, is of high heating value. A disadvantage arises, however, from the fact that the splitting up of water absorbs a considerable amount of heat, which must in some way be restored in order to keep the coal up to the reaction temperature.
This is generally done by alternating blows of steam and air; the preferable solution of the problem, however, is to blow steam and air together through heated coal so that a gas of high thermal value is obtained, while maintaining the reaction temperature. Fuel gas produced by this method has, in the past, been known as semi-water gas, but the wide adoption of the process has led to it being now designated as producer gas, a name which, it will be remembered, had been formerly applied to the gas produced by blowing air through coal.
The proportions of air and steam, the latter being superheated, are so adjusted as to ensure continuity of the process, the heat of the gas leaving the retort being utilized to preheat the incoming air. The average percentage constitution of the product is as follows
CH, CO N2 CO2
15 2 28 50 5 The Lower Calorific Value is 85 C.H.U. per standard cubic foot. As compared with the analysis of producer gas given previously, the hydrogen content, it will be noted, is some 10 per cent, higher, this being responsible for the higher thermal value.
It will readily be noted that the calorific values of the various types of producer gases are lower than those of other gaseous fuels, consequently, other things being equal, they do not appear to be suitable for high-power engines of small bulk.
At the present time, of course, the attention of readers of this journal is naturally focused on the possibilities of using producer gas on a large scale for road-transport purposes. Consequently, although the chief purpose of this article is to review the fundamental thermal aspects of gaseous fuels, it will be of interest to consider some of the basic problems likely to be encountered.
As compared with the stationary producer, with its ,s6
massive construction and complicated auxiliary plant, the mobile unit must be reduced to the minimum weight and bulk compatible with a capacity sufficient to avoid too frequent refuelling, and provided, of course, that the thermal efficiency is maintained at a satisfactory figure. Thus, it is essential that the solid fuel used should be of good quality and even grading with a low ash content, preferably removed as it is formed.
Since the rate of gasification must necessarily be high, it is also desirable that the "exposed area" of the solid fuel should be as large as possible, and thus it is preferable to use fuels such as charcoal or coke produced by the low-temperature process rather than anthracite.
The high gasification rate also calls for low bed resistance, this, of course, necessitating the use of a shallow bed of solid fuel. As a result, the producer will tend to run at a relatively high temperature and, generally speaking, a refractory lining will be needed. . The cooling of the gas also presents an acute problem for solution, for it is manifestly impossible to use the bulky coke-filled, water-cooled scrubber normally used on stationary plant. Various cooling systems are under investigation at the moment, details of which will be published as occasion arises, but in view of the desirability of avoiding the need for carrying bulky supplies of water, considerable interest attaches to suggestions that air-cooled tubular cleaners or evaporative cooling systems be employed.
• Producer-gas Lorry of 1921 •
Investigations now proceeding into the design of mobile producers are yielding striking and valuable results, as reference to recent issues of this journal will demonstrate. It is interesting, however, to consider that so long ago as 1921 a practicable producer for traction purposes was evolved by Parker, details of which are described by Rambush in his book "Modern Gas Producers." The unit weighed 4 I 4 cwt. and developed 45 b.h.p. When fitted to a 3-ton lorry the solid fuel consumption amounted to 3 lb. of coke per mile of a 100-mile journey. jThe Smith producer was used on an R.A.S.C. lorry for seven months in 1918.—ED.1
Thus, the fuel costs were very low as compared with those for a similar vehicle running on petrol. With regard to the maximum power attainable with such mobile units, Rarnbush quotes a figure only 15 per cent. lower than that obtained with normal liquid fuels. It will be of considerable interest to compare these figures with those obtained during the present period of intensive development. One prominent producer-gas authority gives 25-30 per cent. as a power-drop figure for modern plants. A basic up-to-date consumption figure is 12-15 lb., equivalent to one gallon of petrol.
Reference has been made previously to the fact that a further industrial use for producer gas results from its high nitrogen content. When we consider that water gas is rich in hydrogen, the two fuels present themselves as admirable bases from which to manufacture ammonia.
Constituents other than nitrogen are removed from producer gas, whilst those other than hydrogen are removed, by chemical means, from water gas. The mixture of these two gases, at suitable temperature and pressure, is converted, by means of a catalyst, into ammonia gas.
Whilst this process has no direct bearing on the fuel question, the extent to which it is exploited has resulted in the accumulation of a vast quantity of data regarding the manufacture of both producer and water gases. If this data be made available to internal-combustion engineers it should prove helpful in the highest degree.