Know Your Air Brakes
Page 61
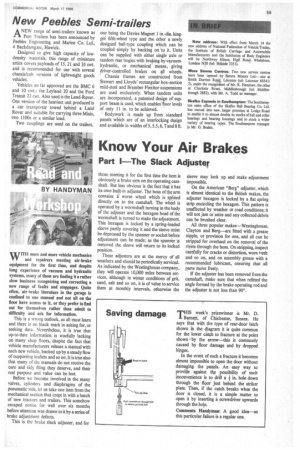
If you've noticed an error in this article please click here to report it so we can fix it.
Part I The Slack Adjuster
WITH more and more vehicle mechanics and repairers meeting air-brake equipment for the first time, and despite long experience of vacuum and hydraulic systems, many of them are finding it a rather slow business recognizing and correcting a new range of faults and stoppages. Quite often, air-brake literature in the garage is confined to one manual and not all on the floor have access to it, or they prefer to find Out for themselves rather than admit to difficulty and ask for Information.
This is a wrong outlook, as all must learn and there is no black mark in asking for, or seeking data. Nevertheless, it is true that up-to-date information is woefully lacking on many shop floors, despite the fact that vehicle manufacturers release a manual with each new vehicle, backed up by a steady flow of supporting leaflets and so on. It is true also that many of the manuals do not receive the care and tidy filing they deserve, and their real purpose and value can be lost.
Before we become involved in the many valves, cylinders and diaphragms of the pneumatic side, let us take one item from the mechanical section that crept in with a batch of new tractors and trailers. This somehow escaped notice for well over six months before attention was drawn to it by a series of brake adjustment defects.
This is the brake slack adjuster, and for those meeting it for the first time the item is obviously a brake arm on the operating camshaft. But less obvious is the fact that it has its own built-in adjuster. The boss of the arm contains a: worm wheel which is splined directly on to the camshaft. The wheel is operated by a wormshaft turning in the body of the adjuster and the hexagon head of the wormshaft is turned to make the adjustment. This hexagon is locked by a spring-loaded sleeve partly covering it and the sleeve must be depressed by the spanner or socket before adjustment can be made; as the spanner is removed the sleeve will return to its locked position.
These adjusters are at the mercy of all weathers and should be periodically serviced. As indicated by the Westinghouse company, they will operate 10,000 miles between services, although in winter conditions of grit, sand, salt and so on, it is of value to service them at monthly intervals, otherwise the sleeve may lock up and make adjustment impossible.
On the American "Berg" adjuster, which is almost identical to the British makes, the adjuster hexagon is locked by a flat spring strip encircling the hexagon. This pattern is unaffected by weather or road conditions; it will not jam or seize and any collected debris can be brushed clear.
All three popular makes—Westinghouse, Clayton and Berg—are fitted with a grease nipple, or provision for one, and all can be stripped for overhaul on the removal of the rivets through the boss. On stripping, inspect carefully for cracks or distortion, worn meth and so on, and on assembly grease with a recommended lubricant, ensuring that all parts move freely.
If the adjuster has been removed from the camshaft, make sure that when refitted the angle formed by the brake operating rod and the adjuster is not less than 900.