IS THIS THE IDEAL BUS CHASSIS?
Page 43
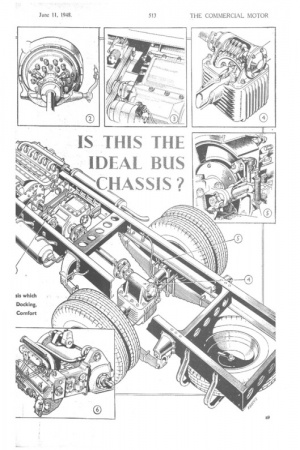
Page 42
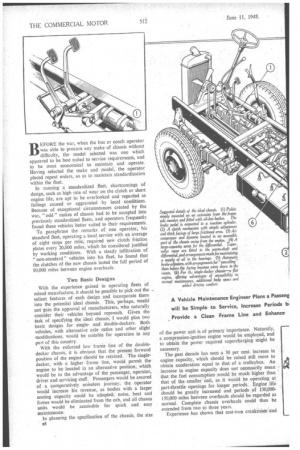
Page 44
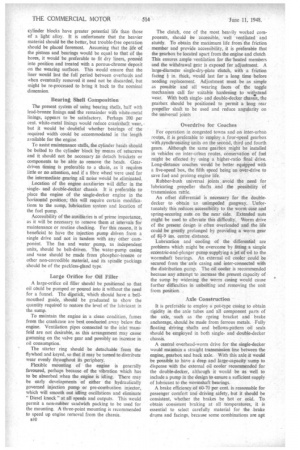
Page 47
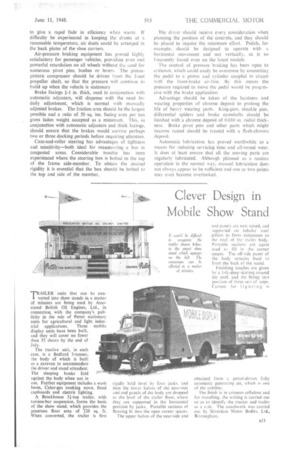
If you've noticed an error in this article please click here to report it so we can fix it.
BEFORE the war, when the bus or coach operator was able to procure any make of chassis without difficulty, the model selected was one which appeared to be best suited to service requirements, and to be most economical to maintain and operate. Having selected the make and model, the operator placed repeat orders, so as to maintain standardization within the fleet.
In running a standardized fleet, shortcomings of design, such as high rate of wear on the clutch or short engine life, are apt to be overlooked and regarded as failings caused or aggravated by local conditions. Because of exceptional circumstances created by the war, " odd " makes of chassis had to be accepted into previously standardized fleets, and operators frequently found these vehicles better suited to their requirements.
To paraphrase the remarks of one operator, his standard fleet, operating a local service with an average of eight stops per mile, required new clutch friction plates every 20,000 miles, which he considered justified by working conditions, With a steady infiltration of "non-standard" vehicles into his fleet, he found that the clutches of the new chassis lasted the full period of 80,000 miles between engine overhauls.
Two Basic Designs With the experience gained in operating fleets of mixed manufacture, it should be possible to pick out the salient features of each design and incorporate them into the potential ideal chassis. This, perhaps, would not gain the approval of manufacturers, who naturally consider their vehicles beyond reproach. Given the task of specifying the ideal chassis, I would plan two basic designs for singleand double-deckers. Both vehicles, with alternative axle ratios and other slight modifications, would be suitable for operation in any part of this country.
With the enforced low frame line of the doubledecker chassis, it is obvious that the present forward position of the engine should be retained. The singledecker, with a higher frame tine, would permit the engine to be located in an alternative position, which would be to the advantage of the passenger, operator, driver and servicing staff. Passengers would be assured of a comparatively noiseless journey; the operator would increase his revenue, as bodies with a larger seating capacity could be adopted; noise, heat and fumes would be eliminated from the cab, and all chassis units would be accessible for quick and easy maintenance.
In planning the specification of the chassis, the size of the power unit is of primary importance. Naturally, a compression-ignition engine would be employed, and to obtain the power required supercharging might be necessary.
The past decade has seen a 30 per cent. increase in engine capacity, which should be raised still more to obtain acceleration equal to that of a trolleybus. An increase in engine capacity does not necessarily mean that the fuel consumption would be much higher than that of the smaller unit, as it would be operating at part-throttle openings for longer periods.. Engine life should be greatly increased and periods of 130,000150,000 miles between overhauls should be regarded as normal. Complete chassis overhauls could thus be extended from two to three years.
Experience has shown that cast-iron crankcases: and
cylinder blocks have greater potential life than those of a light alloy. It is unfortunate that the heavier material should be the better, but trouble-free operation should be placed foremost. Assuming that the life of the pistons and bearings would be equal to that of the bones, it would be preferable to fit dry liners, pressed into position and treated with a porous-chrome deposit on the wearing surfaces. This would ensure that the liner would last the full period between overhauls and when eventually removed it need not be discarded, but might be re-processed to bring it back to the nominal dimension.
Bearing Shell Composition
The present system of using bearing shells, half with lead-bronze linings and the remainder with white-metal linings, appears to be satisfactory. Perhaps 100 per cent. white-metal linings would reduce crankshaft wear, but it would be doubtful whether bearings of the required width could be accommodated in the length available for the engine To assist maintenance staffs, the cylinder heads should be bolted to the cylinder block by means of setscrews and it should not be necessary to detach brackets or components to be able to remove the heads. Geardriven timing is preferable to a chain, as it requires little or no attention, and if a fibre wheel were used for the intermediate gearing all noise would be eliminated.
Location of the engine auxiliaries will differ in the singleand double-decker chassis It is preferable to place the engine of the single-decker engine in the horizontal position: this will require certain modifications to the sump, lubrication system and location of the fuel pump.
Accessibility of the auxiliaries is of prime importance, as it will be necessary to remove them at intervals for maintenance or routine checking. For this reason, it is beneficial to have the injection pump driven from a single drive and not in tandem with any Other component. The fan and water pump, as independent units, should be belt-driven. The water-pump casing and vane should be made from phosphor-bronze or other non-corrodible material, and its spindle packings should be of the packless-gland type.
Large Orifice for Oil Filler A large-orifice oil filler should be positioned so that oil could be pumped or poured into it without the need for a funnel. The dipstick, which should have a bellmouthed guide, should be graduated to show the quantity required to restore the level of the lubricant in the surnp.
To maintain the engine in a clean condition, fumes from the crankcase are best conducted away below the engine. Ventilation pipes connected to the inlet manifold are not desirable, as this arrangement may cause gumming on the valve gear and possibly an increase in oil consumption.
The starter ring should be detachable from the flywheel and keyed, so that it may be turned to distribute wear evenly throughout its periphery.
Flexible mounting of the engine is generally favoured, perhaps because of the vibration which has to be absorbed when the engine is idling. There may be early developments of either the .hydraulically governed injection pump or pre-combustion injector, which will smooth out idling oscillations and eliminate "Diesel knock" at all speeds and outputs. This would permit a non-rubber sandwich packing to be used for the mounting. A three-point mounting is recommended to speed up engine removal from the chassis.
B10 The clutch, one of the most heavily worked components, should be accessible, well ventilated and sturdy. To obtain the maximum life from the friction member and provide accessibility, it is preferable that the gearbox be located apart from the engine and clutch This ensures ample ventilation for the'heated members and the withdrawal gear is exposed for .adjustment. A large-diameter single-dry-plate clutch, with a friction facing Iin. thick, would last for a long time before needing replacement. Adjustment must be as simple as possible and all wearing faces of the toggle mechanism call for suitable hardening to witstand wear. With both singleand double-decker chassis, the gearbox should be positioned to permit a long rear propeller shaft to be used and reduce angularity on the universal joints
Overdrive for Coaches
For operation in congested towns and on inter-urban routes, it is preferable to employ a ,four-speed gearbox with synchronizing units on the second, third and fourth gears. Although the same gearbox might be installed in vehicles on inter-urban routes, conservation of fuel might be effected by using a higher-ratio final drive. Long-distance coaches would be better equipped with a five-speed box, the fifth speed being an over-drive to save fuel and prolong engine life.
Rubber-bush universal joints avoid the need for lubricating propeller shafts and the possibility of transmission rattle.
An offset differential is necessary for the doubledecker to obtain an unimpeded gangway. Unfortunately this reduces accessibility to the worm case and spring-securing nuts on the near side. Extended nuts might be used to alleviate this difficulty. Worm drive of the present design is often overloaded and the life could be greatly prolonged by providing a worm gear of 81-9 ins, centre distance.
Lubrication and cooling of the differential are problems which might be overcome by fitting a simple eccentric-and-plunger pump supplying a jet of oil to the wormshaft bearings. An external oil cooler could be secured from the axle casing and inter-connected with the distribution pump. The oil cooler is recommended because any attempt to increase the present capacity of the sump by widening the worm casing would cause further difficulties in unbolting and removing the unit from position.
Axle Construction It is preferable to employ a pot-type casing to obtain rigidity in the axle tubes and all component parts of the axle, such as the spring bracket and brake anchorage, should be made from ferrous metals. Fully floating driving shafts and bellows-pattern oil seals should be employed in both singleand double-decker chassis.
A central overhead-worm drive for the single-decker would maintain a straight transmission line between the engine, gearbox and back axle. With this axle it would be possible to have a deep and large-capacity sump to dispense with the external oil cooler recommended for the double-decker, although it would be as well to include a pump in the design to ensure a sufficient supply of lubricant to the wormshaft bearings.
A brake efficiency of 60-70 per cent. is reasonable for passenger comfort and driving safety, but it should be consistent, whether the brakes be hot or cold. To obtain consistent braking at all temperatures, it is essential to select carefully material for the .brake drums and facings, because some combinations are apt
to give a rapid fade in efficiency when warm. If difficulty be experienced in keeping the drums at a reasonable temperature, air ducts could be arranged in the back plates of the shoe carriers.
Air-pressure braking equipment has proved highly satisfactory for passenger vehicles, providing even and powerful retardation on all wheels without the need for numerous pivot pins, bushes or levers. The pistonpattern compressor should be driven from the front propeller shaft, so that the pressure vvill continue to build up when the vehicle is stationary Brake facings fEki in. thick, used in conjunction with automatic adjusters, will dispense with the need for daily adjustment, which is normal with manually adjusted brakes. The friction area should be the largest possible and a ratio of 50 sq. ins, facing area per ton gross laden weight accepted as a minimum. This, in conjunction with automatic adjusters and thick facings, should ensure that the brakes would survive perhaps two or three docking periods before requiring attention.
Cam-and-roller steering has advantages of lightness and sensitivity—both ideal for manoeuvring a bus in congested areas. Considerable trouble has been experienced where the steering box is bolted to the top of the frame side-member. To obtain the desired rigidity it is essential that the box should be bolted to the top and side of the member.
The driver should receive every consideration when planning the position of the controls, and they should be placed to require the minimum effort. Pedals, for example. should be designed to operate with a horizontal movement and not vertically, as is so frequently found even on the latest models.
The control of pressure braking has been open to criticism, which could easily be overcome by connecting the pedal to a piston and cylinder coupled in circuit with the front-brake air-line. By this means the Pressure required to move the pedal would be progressive with the brake application.
Advantage should he taken of the hardness and wearing properties of chrome deposit to prolong the life of heavy wearing parts. King-pins, shackle pins, differential spiders and brake camshafts should be .finished with a chrome deposit of 0.010 in. radial thickness. Brake pivot pins and other parts which might become rusted should be treated with a flash-chrome deposit.
Automatic lubrication has proved worthwhile as a means for reducing servicing time and all-round wear: It does at least ensure that all the moving parts are regularly lubricated. Although planned as a routine operation in the normal way, manual lubrication does not always appear to be sufficient and one or two points may even become overlooked.