Planning for Profit
Page 60
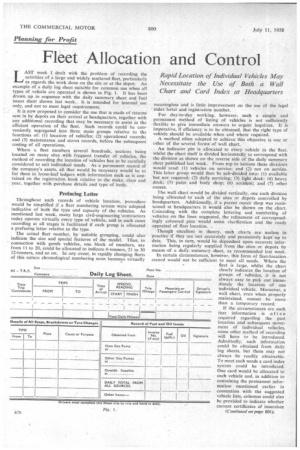
Page 63
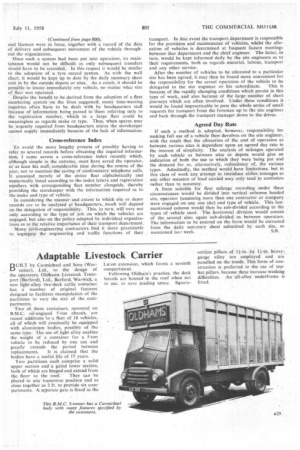
If you've noticed an error in this article please click here to report it so we can fix it.
Fleet Allocation and Control
AST week I dealt with the problem of recording the activities of a large and widely scattered fleet, particularly as regards the work done on the site or at the depot. An example of a daily log sheet suitable for common use when all types of vehicle are operated is shown in Fig. 1. It has been drawn up in sequence with the daily summary sheet and fuel issues sheet shown last week._ It is intended for internal ,usc only, and not to meet legal requirements.
It is now proposed to consider the use that is made of returns sent in by depots on their arrival at headquarters, together with any additional recording that may be necessary to assist in the efficient operation of the fleet. Such records could be conveniently segregated into three main groups relative to the functions of: (1) location of vehicles; (2) operational records; and (3) maintenance and stores records, before the subsequent costing of all operations.
Where a fleet numbers several hundreds, sections being located on many sites with frequent transfer of vehicles, the method of recording the location of vehicles has to be carefully considered to suit individual needs. As a permanent record of the company's assets, all that would be necessary would be to list them in loose-leaf ledgers with information such as is contained on the registration book relative to the make, class and year, together with purchase details and type of body.
Prefacing Letter
Throughout such records of vehicle location, procedure would be simplified if a fleet numbering system were adopted indicative of both the type and capacity of the vehicles. As mentioned last week, many large civil-engineering 'contractors today operate virtually every type of vehicle, and in such cases recording at all stages is facilitated if each group is allocated a prefacing letter relative to the type.
The actual fleet number, by suitable grouping, could also indicate the size and special features of the model. Ttius, in connection with goods vehicles, one block of numbers, say from 11 to 20; could be allocated to indicate 8-tonners, 21 to 30 l2-tonners, and so on. In any event, in rapidly changing fleets of this nature chronological numbering soon becomes virtually meaningless and is little improvement on the use of the legal index letter and registration number.
For day-to-day working, however, such a simple and permanent method of listing of vehicles is not sufficiently flexible to give immediate answers to urgent inquiries. It is imperative, if efficiency is to be obtained, that the right type of vehicle should be available when and where required.
A method often adopted to achieve this objective is one or other of the several forms of wall chart.
An indicator pin is allocated to every vehicle in the fleet,
whilst the chart itself is divided horizontally to correspond with the division as shown on the reverse side of the daily summary sheet published last week. From tdp to bottom these divisions would read: (1) vehicles on service; and (2) not on service. This latter group would then be sub-divided into: (1) available but not required; (2). daily servicing; (3) light dock; (4) heavy dock: (5) paint and body shop; (6) accident; and (7) other causes.
The wall chart would be divided vertically, one such division
being allocated to each of the sites or depots controlled by headquarters. Additionally, if a parent repair shop was maintained at headquarters it would also be shown on the chart. Coinciding with the complete lettering and numbering of vehicles on the lines suggested, the refinement of correspond.ingly coloured pins would assist clarification and the ready appraisal of fleet location.
Though excellent; in theory, such charts are useless in practice if they are not accurately and persistently kept up to date. This, in turn, would be dependent upon accurate information being regularly supplied from the sites. or depots by means of a daily summary sheet, as recommended last week.
In certain circumstances, however, this form of fleet-location. record would not be sufficient to meet all needs. Where the • fleet is large, whilst the chart clearly indicates the location of groups of vehicles, it is not always easy to pick out imme diately the location of one individual vehicle. Moreover, a wall chart, even when properly maintained, cannot be more than a temporary record.
If the circumstances are such that information is of ten required regarding the past location and subsequent movement of individual vehicles, some other method of recording will have to be introduced. Admittedly, such information could be obtained from daily log sheets, but these may not always be readily obtainable. To meet such needs a card index system could be introduced. One card would be allocated to each vehicle and, in addition to containing the permanent information mentioned earlier in connection with the suggested vehicle lists, columns could also be provided to indicate whether current certificates of insurAce
(Continued on page 801).
and licences were in force, together with a record of the date of delivery and subsequent movement of the vehicle throughout the organization.
Once such a system had been put into operation, its maintenance would not be difficult as only subsequent transfers would have to be recorded. In this respect it would be similar to the adoption of a tyre record system. As with the wall chart, it would be kept up to date by the daily summary sheet sent in by the outside depots or sites. As a result, it should be possible to locate immediately any vehicle, no matter what size of fleet was operated.
Despite the benefit to be derived from the adoption of a fleet numbering system on the lines suggested, .many time-wasting inquiries often have to be dealt with by headquarters staff because of information being passed to them referring only to the registration number, which in a large fleet could be meaningless as regards make or type. Thus, when spares may be .urgently required from headquarters stores the storekeeper cannot supply immediately because of the lack of information.
Cross-reference Index
To avoid the more lengthy process of possibly having to refer to several records before obtaining the required information. I came across a cross-reference index recently which, although simple in the extreme, must have saved the operator, or at least his staff, considerable time during the course of the year, not to mention the saving of confirmatory telephone calls. It consisted merely of the entire fleet alphabetically and numerically listed according to the index letters and registration numbers with corresponding fleet number alongside, thereby providing the storekeeper with the information required as to the make and type of vehicle.
In considering the manner and extent to which site or depot records are to be analysed at headquarters, much will depend on the delegation of responsibility: This, in turn, will vary not only according to the type. of job on which the vehicles are engaged, but also on the policy adopted by individual organizations as to the relative importance of their transport department.
• Many civil-engineering contractors find it More practicable to segregate the engineering and traffic functions of their transport. In that event the transport department is responsible for the provision and maintenance of vehicles, whilst the allocation of vehicles is determined at frequent liaison meetings between that department and the chief engineer. The latter, in turn, would be kept informed daily by the site engineers as to their requirements, both as regards material, labour, transport and any other service.
After the number of vehicles to be allocated to a particular site has been agreed, it may then be found more convenient for the responsibility for the actual operation of the vehicle to be delegated to the site engineer or his subordinate. This is because of the rapidly changing conditions which persist in this type of work, and also because of the large number of short journeys which are often involved. Under these conditions it would be found impracticable to pass the whole series of small requests for transport from the foreman up to the site engineer and hack through the transport manager down to the driver.
Agreed Day Rate If such a method is adopted, however, responsibility for making full use of a vehicle then devolves on the site engineer, with the result that the allocation of the cost of operation as between various sites is dependent upon an agreed day rate in the interest of simplicity. The analysis of mileages operated by each vehicle as between sites or depots would give an indication of both the use to which they were being put and the demand for or, alternatively, redundancy of, the various types. Admittedly, the method would have limitations, but in this class of work any attempt to introduce either, tonnages or any other measure of load carried may only tend to confusion rather than to accuracy.
A form suitable for fleet mileage recording under these circumstances would be divided into vertical columns headed site, operator (assuming more than one contractor or company were engaged on any one site) and type of vehicle. This lastmentioned column would then be sub-divided according to the types of vehicle used. The horizontal division would consist of the several sites again sub-divided as between operators. The information to be entered on the form would be extracted from the daily summary sheet submitted by each site, as mentioned last week. S.B.