ENFORCEMENT COMMENTARY: ROSS-ON-WE WEIGHING
Page 6
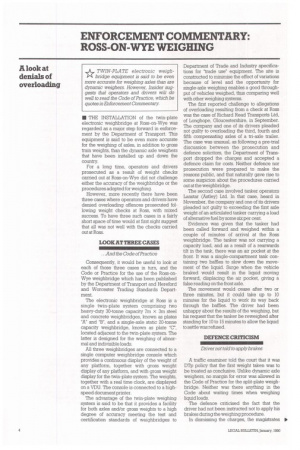
Page 7
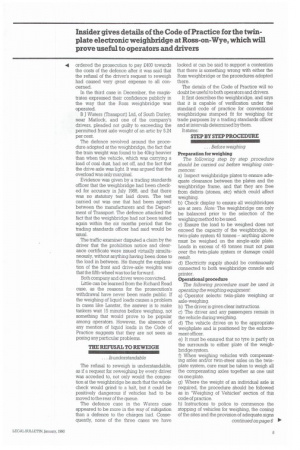
Page 8
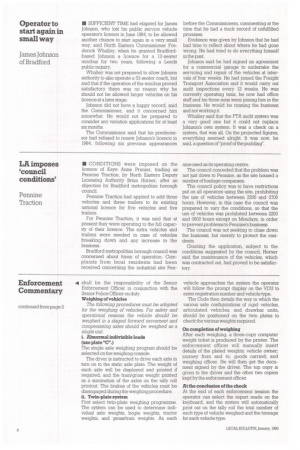
If you've noticed an error in this article please click here to report it so we can fix it.
A look at denials of overloading
TWIN-PLATE electronic weighkA bridge equipment is said to be even more accurate for weighing axles than are dynamic weighers. However, Insider suggests that operators and drivers will do well to read the Code of Practice, which he quotes in Enforcement Commentary.
• THE INSTALLATION of the twin-plate electronic weighbridge at Ross-on-Wye was regarded as a major step forward in enforcement by the Department of Transport. This equipment is said to be even more accurate for the weighing of axles, in addition to gross train weights, than the dynamic axle weighers that have been installed up and down the country.
For a long time, operators and drivers prosecuted as a result of weight checks carried out at Ross-on-Wye did not challenge either the accuracy of the weighbridge or the procedures adopted for weighing.
However, more recently there have been three cases where operators and drivers have denied overloading offences prosecuted following weight checks at Ross, with mixed success. To have three such cases in a fairly short space of time would at first sight suggest that all was not well with the checks carried out at Ross.
LOOK AT THREE CASES And the Code of Practice Consequently, it would be useful to look at each of those three cases in turn, and the Code or Practice for the use of the Ross-onWye weighbridge which has been published by the Department of Transport and Hereford and Worcester Trading Standards Department.
The electronic weighbridge at Ross is a single twin-plate system comprising two heavy-duty 30-tonne capacity 7m x 3m steel and concrete weighbridges, known as plates "A" and "B", and a single-axle static 20-tonne capacity weighbridge, known as plate "C", located adjacent to the twin-plate system. The latter is designed for the weighing of abnormal and indivisible loads.
All three weighbridges are connected to a single computer weighbridge console which provides a continuous display of the weight of any platform, together with gross weight display of any platform, and with gross weight display for the twin-plate system. The weights, together with a real time clock, are displayed on a VDU. The console is connected to a highspeed document printer.
The advantage of the twin-plate weighing system is said to be that it provides a facility for both axles and/or gross weights to a high degree of accuracy meeting the test and certification standards of weighbridges to Department of Trade and Industry specifications for "trade use" equipment. The site is constructed to minimise the effect of variations because of level and the opportunity for single-axle weighing enables a good throughput of vehicles weighed, thus comparing well with other weighing systems.
The first reported challenge to allegations of overloading resulting from a check at Ross was the ease of Richard Read Transports Ltd, of Longhope, Gloucestershire, in September. The company and one of its drivers pleaded not guilty to overloading the third, fourth and fifth compensating axles of a tri-axle trailer. The case was unusual, as following a pre-trial discussion between the prosecution and defence solicitors, the Department of Transport dropped the charges and accepted a defence claim for costs. Neither defence nor prosecution were prepared to make the reasons public, and that naturally gave rise to some suspicion about the procedures carried out at the weighbridge.
The second rAse involved tanker operators Lanstar (Astley) Ltd. In that case, heard in November, the company and one of its drivers pleaded not guilty to exceeding the first axle weight of an articulated tanker carrying a load of alternative fuel by some six per cent.
Evidence was given that the tanker had been called forward and weighed within a couple of minutes of arrival at the Ross weighbridge. The tanker was not carrying a capacity load, and as a result of a rearwards tilt in the tank, there was an air pocket at the front. It was a single-compartment tank containing two baffles to slow down the movement of the liquid. Surge when the vehicle braked would result in the liquid moving forward, displacing the air pocket, giving a false reading on the front axle.
The movement would cease after two or three minutes, but it could take up to 10 minutes for the liquid to work its way back through the baffles. The driver had been unhappy about the results of the weighing, but his request that the tanker be reweighed after standing for 10 to 15 minutes to allow the liquid to settle was refused.
DEFENCE CRITICISM Dnver not told to apply brakes A traffic examiner told the court that it was DTp policy that the first weight taken was to be treated as conclusive. Unlike dynamic axle weighers, no margin for error was allowed in the Code of Practice for the split-plate weighbridge. Neither was there anything in the Code about waiting times when weighing liquid loads.
The defence criticised the fact that the driver had not been instructed not to apply his brakes during the weighing procedure.
In dismissing the charges, the magistrates • ordered the prosecution to pay £400 towards the costs of the defence after it was said that the refusal of the driver's request to reweigh had caused very great expense to all concerned.
In the third case in December, the magistrates expressed their confidence publicly in the way that the Ross weighbridge was operated.
B J Waters (Transport) Ltd, of South Darley, near Matlock, and one of the companYs drivers, pleaded not guilty to exceeding the permitted front axle weight of an artic by 5.24 per cent.
The defence revolved around the procedure adopted at the weighbridge, the fact that the train weight was found to be 40kg heavier than when the vehicle, which was carrying a load of coal dust, had set off, and the fact that the drive axle was light. It was argued that the overload was only marginal.
Evidence was given by a trading standards officer that the weighbridge had been checked for accuracy in July 1988, and that there was no statutory test laid down. The test carried out was one that had been agreed between the manufacturers and the Department of Transport. The defence attacked the fact that the weighbridge had not been tested again within the six months period that the trading standards officer had said would be usual.
The traffic examiner disputed a claim by the driver that the prohibition notice and clearance certificate were issued virtually simultaneously, without anything having been done to the load in between. He thought the explanation of the front and drive-axle weights was that the fifth-wheel was too far forward.
Both company and driver were convicted.
Little can be learned from the Richard Read case, as the reasons for the prosecution's withdrawal have never been made public. If the weighing of liquid loads causes a problem in cages like Lanstar, the answer is to make tankers wait 15 minutes before weighing, not something that would prove to be popular among operators. However, the absence of any mention of liquid loads in the Code of Practice suggests that they are not seen as posing any particular problems.
THE REFUSAL TO RE WEIGH
. . . Is understandable The refusal to reweigh is understandable, as if a request for reweighing by every driver was acceded to, not only would the congestion at the weighbridge be such that the whole check would grind to a halt, but it could be positively dangerous if vehicles had to be moved to the rear of the queue.
The defence case in the Waters case appeared to be more in the way of mitigation than a defence to the charges laid. Consequently, none of the three cases we have looked at can be said to support a contention that there is something wrong with either the Ross weighbridge or the procedures adopted there.
The details of the Code of Practice will no doubt be useful to both operators and drivers.
It first describes the weighbridge, and says that it is capable of verification under the standard code of practice for conventional weighbridges stamped fit for weighing for trade purposes by a trading standards officer and at intervals determined by them.
It states: STEP BY STEP PROCEDURE 1■IONEHOM■■ . . . Before weighing Preparation for weighing The following step by step procedure should be carried out before weighing commences: a) Inspect weighbridge plates to ensure adequate clearance between the plates and the weighbridge frame, and that they are free from debris (stones, etc) which could affect weighing.
b) Check display to ensure all weighbridges are at zero. Note: The weighbridge. can only be balanced prior to the selection of the weighing method to be used.
c) Ensure the load to be weighed does not exceed the capacity of the weighbridge, ie twin-plate system 45 tonnes anything above must be weighed on the single-axle plate. Loads in excess of 45 tonnes must not pass over the twin-plate system or damage could result.
d) Electricity supply should be continuously connected to both weighbridge console and printer.
Operational procedure The followkig procedure must be used in operating the weighing equipment: a) Operator selects: twin-plate weighing or axle-weighing.
b) The driver is given clear instructions.
c) The driver and any passengers remain in the vehicle during weighing.
d) The vehicle drives on to the appropriate weighplate and is positioned by the enforcement officer.
e) It must be ensured that no tyre is partly on the surrounds to either plate of the weighbridge system.
I) When weighing vehicles with compensating axles and/or twin-steer axles on the twinplate system, care must be taken to weigh all the compensating axles together as one unit on one plate.
g) Where the weight of an individual axle is required, the procedure should be followed as in "Weighing of Vehicles" section of this code of practice.
h) Instructions to police to commence the stopping of vehicles for weighing, the coning of the sites and the provision of adequate signs continued on page 6 • shall be the responsibility of the Senior Enforcement Officer in conjunction with the Senior Police Officer on duty.
Weighing of vehicles The following procedures must be adopted for the weighing of vehicles. For safety and operational reasons the vehicle should be weighed in a staged forward movement and compensating axles should be weighed as a single unit L Abnormal indivisible loads (use plate "C".) The single axle weighing program should be selected on the weighing console.
The dryer is instructed to drive each axle in turn on to the static axle plate. The weight of each axle will be displayed and printed if required, and the train/gross weight printed as a summation of the axles on the tally roll printout. The brakes of the vehicles must be disengaged during the weighing procedure.
IL Twin-plate system First select twin-plate weighing programme. The system can be used to determine individual axle weights, bogie weights, tractor weights, and gross/train weights. As each vehicle approaches the system the operator will follow the prompt display on the VDU to enter registration number and vehicle type.
The Code then details the way in which the various axle configurations of rigid vehicles, articulated vehicles, and drawbar units, should be positioned on the twin plates to check the various weights required.
On completion of weighing After each weighing, a three-copy computer weight ticket is produced by the printer. The enforcement officer will manually insert details of the plated weights; vehicle owner; journey from and to; goods carried; and weighing officer. He will then get the document signed by the driver. The top copy is given to the driver and the other two copies kept by the enforcement officer.
At the conclusion of the check At the end of each enforcement session the operator can select the report made on the keyboard, and the system will automatically print out on the tally roll the total number of each type of vehicle weighed and the tonnage for each vehicle type.