elp stop wheel loss
Page 20
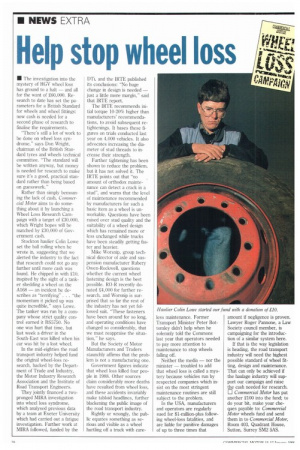
If you've noticed an error in this article please click here to report it so we can fix it.
DTi, and the IRTE published • The investigation into the mystery of HGV wheel loss has ground to a halt — and all for the want of .W0,000. Research to date has set the parameters for a British Standard for wheels and wheel fittings: now cash is needed for a second phase of research to finalise the requirements.
"There's still a lot of work to he done on wheel loss syndrome," says Don Wright, chairman of the British Standard tyres and wheels technical committee. "The standard will be written anyway, but money is needed for research to make sure it's a good, practical standard rather than being based on guesswork."
Rather than simply bemoaning the lack of cash, Commercial Motor aims to do something about it by launching a Wheel Loss Research Campaign with a target of 230,000, which Wright hopes will be matched by M0,000 of Government cash.
Stockton haulier Cohn Lowe set the ball rolling when he wrote in, suggesting that we alerted the industry to the fact that research could not go any further until more cash was found. He chipped in with £10, inspired by the sight of a tanker shedding a wheel on the A168 — an incident he describes as "terrifying" . . . "the momentum it picked up was quite incredible," says Lowe. The tanker was run by a company whose strict quality control earned it BS5750. No one was hurt that time, but last week a driver in the South-East was killed when his car was hit by a lost wheel.
In the mid-eighties the road transport industry helped fund the original wheel-loss research, backed by the Department of Trade and Industry, the Motor Industry Research Association and the Institute of Road Transport Engineers.
They jointly financed a twopronged MIRA investigation into wheel loss syndrome, which analysed previous data by a team at Exeter University which had carried out a fatigue investigation. Further work at MIRA followed, funded by the DTi, and the IRTE published its conclusions: "No huge change in design is needed — just a little more margin," said that IRTE report.
The IRTE recommends initial torque 10-20% higher than manufacturers' recommendations, to avoid subsequent retightenings. It bases these figures on trials conducted last year on 4,000 vehicles. It also advocates increasing the diameter of stud threads to increase their strength.
Further tightening has been shown to reduce the problem, but it has not solved it. The IRTE points out that "no amount of orthodox maintenance can detect a crack in a stud", and warns that the level of maintenance recommended by manufacturers for such a basic item as a wheel is unworkable. Questions have been raised over stud quality and the suitability of a wheel design which has remained more or less unchanged while trucks have been steadily getting faster and heavier.
Mike Worsnip, group technical director of axle and suspension manufacturer Rubery Owen-Rockwell. questions whether the current wheel fastening design is the best possible. RO-R recently donated 24,000 for further research, and VVorsnip is surprised that so far the rest of the industry has not yet followed suit, ''These fasteners have been around for so long, and operating conditions have changed so considerably, that we must reappraise the situation," he says.
But the Society of Motor Manufacturers and Traders staunchly affirms that the problem is not a manufacturing one.
Government figures indicate that wheel loss killed four people in 1988. Other sources claim considerably more deaths have resulted from wheel loss, and these accidents invariably make tabloid headlines, further blackening the public image of the road transport industry.
Rightly or wrongly, the public equates something as serious and visible as a wheel hurtling off a truck with care less maintenance. Former Transport Minister Peter Bottomley didn't help when he solemnly told the Commons last year that operators needed to pay more attention to maintenance to stop wheels falling off.
Neither the media — nor the minister — troubled to add that wheel loss is called a mystery because vehicles run by respected companies which insist on the most stringent maintenance routines are still subject to the problem.
In the USA, manufacturers and operators are regularly sued for $1-million-plus following wheel-loss fatalities, and are liable for punitive damages of up to three times that amount if negligence is proven. Lawyer Roger Pannone, a Law Society council member, is campaigning for the introduction of a similar system here.
If that is the way legislation is heading, the road transport industry will need the highest possible standard of wheel fitting, design and maintenance. That can only be achieved if the haulage industry will support our campaign and raise the cash needed for research.
Commercial Motor has put another £100 into the fund; to do your bit, make your cheques payable to: Commercial Motor wheels fund and send them in to Commercial Motor, Room 403, Quadrant House, Sutton, Surrey SM2 5AS.