VIE GIFTS 86 MEl
Page 38
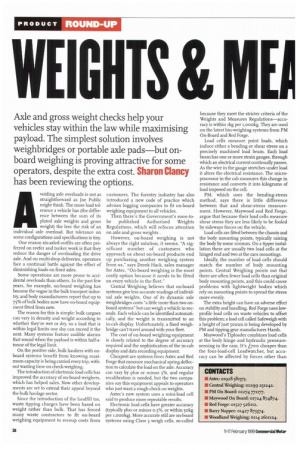
Page 39
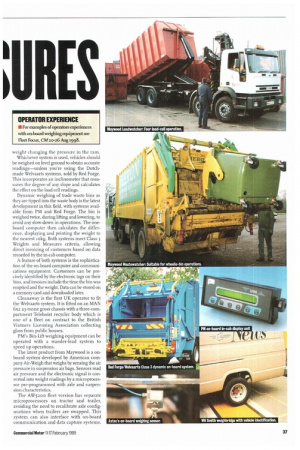
If you've noticed an error in this article please click here to report it so we can fix it.
1111ES
Axle and gross weight checks help your vehicles stay within the law while maximising payload. The simplest solution involves weighbridges or portable axle pads—but on board weighing is proving attractive for some
operators, despite the extra cost. Sharon Clancy
has been reviewing the options.
Avoiding axle overloads is not as straightforward as Joe Public might think. The more load tolerance a vehicle has (the difference between the sum of its plated axle weights and gross weight) the less the risk of an individual axle overload. But tolerance on some configurations and specifications is tiny.
One reason six-wded outfits are often preferred on reefer and tanker work is that they reduce the danger of overloading the drive axle. And on multi-drop deliveries, operators face a continual battle against the effect of diminishing loads on front axles.
Some operations are more prone to accidental overloads than others. In the past few years, for example, on-board weighing has become the vogue in the bulk transport industry, and body manufacturers report that up to 75% of bulk bodies now have on-board equipment fitted from new.
The reason for this is simple: bulk cargoes can vary in density and weight according to whether they're wet or dry, so a load that is within legal limits one day can exceed it the next. Many systems feature audible alarms that sound when the payload is within half-atonne of the legal limit.
On the positive side, bulk hauliers with onboard systems benefit from knowing maximum capacity is being carried every trip, without wasting time on check-weighing.
The introduction of electronic load cells has improved the accuracy of on-board weighers, which has helped sales. Now other developments are set to extend their appeal beyond the bulk haulage sector.
Since the introduction of the landfill tax, waste tipping charges have been based on weight rather than bulk. That has forced many waste contractors to fit on-board weighing equipment to recoup costs from customers. The forestry industry has also introduced a new code of practice which advises logging companies to fit on-board weighing equipment to all vehicles.
Then there's the Government's soon-tobe published Authorised Weights Regulations, which will refocus attention on axle and gross weights.
However, on-board weighing is not always the right solution, it seems. "A significant number of customers who approach us about on-board products end up purchasing another weighing system from us," says Derek Hack, sales manager for Axtec. "On-board weighing is the most costly option because it needs to be fitted on every vehicle in the fleet."
Central Weighing believes that on-board systems give less accurate readings of individual axle weights. One of its dynamic axle weighbridges costs "a little more than two onboard systems" but can weigh a vehide in seconds. Each vehicle can be identified automatically, and the weight is transmitted to an in-cab display. Unfortunately, a fixed weighbridge can't travel around with your fleet.
The cost of on-board weighing equipment is closely related to the degree of accuracy required and the sophistication of the in-cab display and data recording equipment.
Cheapest are systems from Axtec and Red Forge that measure mechanical spring deflection to calculate the load on the axle. Accuracy can vary by plus or minus 5%, and regular recalibration is needed, but the two companies say this equipment appeals to operators who just want a rough check on weights.
Axtec's new system uses a mini-load cell said to produce more repeatable results.
Electronic load cells have greater accuracy (typically plus or minus o.5%, or within 5okg per 1, 000kg). More accurate still are on-board systems using Class 3 weigh cells, so-called because they meet the stricter criteria of the Weights and Measures Regulations—accuracy is within rkg per i,000kg. They are used on the latest bin-weighing systems from PM On-Board and Red Forge.
Load cells measure point loads, which induce either a bending or shear stress on a precisely machined load beam. Each load beam has one or more strain gauges, through which an electrical current continually passes. As the wire in the gauge stretches under load it alters the electrical resistance. The microprocessor in the cab measures this change in resistance and converts it into kilograms of load imposed on the cell.
PM, which uses the bending-stress method, says there is little difference between that and shear-stress measurement. However, Maywood and Red Forge, argue that because their load cells measure shear stress they are less likely to be fooled by sideways forces on the vehicle.
Load cells are fitted between the chassis and the body mounting points, typically raising the body by some roomm. On a tipper installation there are usually two load cells at the hinged end and two at the ram mountings.
Ideally, the number of load cells should match the number of body mounting points. Central Weighing points out that there are often fewer load cells than original body mounting points, and this could cause problems with lightweight bodies which rely on mounting points to spread the stress more evenly.
The extra height can have an adverse effect on stability and handling. Red Forge uses lowprofile load cells on waste vehicles to offset this problem; a load cell called Safeweigh with a height of just somm is being developed by PM and tipping gear manufacturer Harsh.
Maywood's Tiploader combines load cells at the body hinge and hydraulic pressuresensing in the ram. It's L'7oo cheaper than the four-load-cell Loadwatcher, but accuracy can be affected by forces other than weight changing the pressure in the ram.
Whichever system is used, vehicles should be weighed on level ground to obtain accurate readings—unless you're using the Dutchmade Welvaarts systems, sold by Red Forge. This incorporates an inclinometer that measures the degree of any slope and calculates the effect on the load cell readings.
Dynamic weighing of trade waste bins as they are tipped into the waste body is the latest development in this field, with systems avail able from PM and Red Forge. The bin is weighed twice, during lifting and lowering, to avoid any slow, down in operations. The one board computer then calculates the difference, displaying and printing the weight to the nearest lokg. Both systems meet Class 3 Weights and Measures criteria, allowing direct invoicing of customers based on data recorded by the in-cab computer.
A feature of both systems is the sophistication of the on-board computer and communi cations equipment. Customers can be precisely identified by the electronic tags on their bins, and invoices include the time the bin was emptied and the weight. Data can be stored on a memory card and downloaded later.
Cleanaway is the first UK operator to fit the Welvaarts system. It is fitted on an MAN 6x2 23-tonne gross chassis with a three-compartment Telehoist recycler body which is one of a fleet on contract to the British Vintners Licensing Association collecting glass from public houses.
PM's Bin-Lift weighing equipment can be operated with a wander-lead system to speed up operations.
The latest product from Maywood is a onboard system developed by American com
pany Air-Weigh that weighs by sensing the air pressure in suspension air bags. Sensors read air pressure and the electronic signal is con verted into weight readings by a microprocessor pre-programmed with axle and suspension characteristics.
The AW5200 fleet version has separate microprocessors on tractor and trailer, avoiding the need to recalibrate axle configurations when trailers are swapped. This system can also interface with on-board communication and data capture systems