How Precision Maintenance Keeps 1,000 Buses on the Road
Page 96
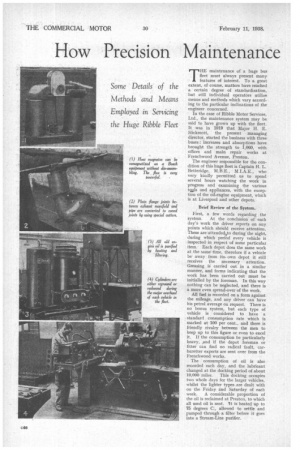
Page 97

Page 98
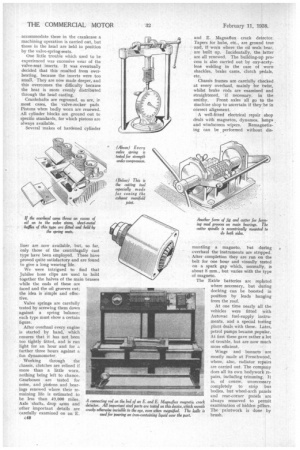
If you've noticed an error in this article please click here to report it so we can fix it.
THE maintenance of a huge bus fleet must always present many features of interest. To a great extent, of course, matters have reached a certain degree of standardization, but still individual operators utilize means and methods which vary according to the particular inclinations of the engineer concerned.
In the case of Ribble Motor Services, Ltd., the maintenance system may be said to have grown up with the fleet. It was in 1919 that Major H. E. Hickmott, the present managing director, started the business with three buses ; increases and absorptions have brought the strength to 1,060, with offices and main repair works at Frenchwood Avenue, Preston, The engineer responsible for the condition of this huge fleet is Captain H. L. Betteridge, M.B.E., INI.I.A.E., who very kindly permitted us to spend several hours watching the work in progress and examining the various tiagls and appliances, with the exception of the oil-engine equipment, which is at Liverpool and other depots.
Brief Review of the System.
First, a few words regarding the system. At the conclusion of each day's work the driver reports on any points which should receive attention. These are attended.to during the night, during which period every vehicle is inspected in respect of some particular item. Each depot does the same work at the same time, therefore if a vehicle be away from itsown depot it still receives the necessary attention. Greasing is carried out in a similar manner, and forms indicating that the work has been carried out must be initialled by the foreman. In this way nothing can be neglected, and there is a more even spread-over of the work.
All fuel is recorded on a form against the mileage, and any driver can have his petrol average on request. There is no bonus system, hut each type of vehicle is considered to have a standard consumption rate which is marked at 100 per cent., and there is friendly rivalry between the men to keep up to this figure or even to excel it. If the consumption be particularly heavy, and if the depot foreman or fitter can find no radical fault, carburetter experts are sent over from the Frenchwood works.
The consumption of oil is also recorded each day, and the lubricant changed at the docking period of about 10,000 miles. This docking occupies two whole days for the larger vehicles, whilst the lighter types are dealt with on the Friday and Saturday of each week. A considerable proportion of the oil is reclaimed at Preston, to which all used oil is sent. It is heated up to 75 degrees C., allowed to settle and pumped through a filter before it goes into a Stream-Line purifier.
Tyres are run under contract, the maker having fitters on night duty to check pressures and make changes. On the buses new and partly worn .tyres are crossed, so, that there is a perfect tyre at the front and back, and, of course, the others, even U worn, must be good. On the express vehicles every tread must be perfect.
Complete vehicle overhauls are done, the unit-exchange principle is not used. These overhauls are carried out at a fixed mileage and until this mileage is run no major work is done. At Frenchwood works up to eight buses are brought in for overhaul each week. The body is removed on the day the machine is brought in, and the chassis stripped of its units, which are then completely dismantled.
After stripping, the parts are washed in a hot soda-ash liquid, for which purpose they are carried on trays and run on rollers into a sheet-steel con tamer, which has upper and lower rotary sprayers, an external steam boiler providing the heat_ Three minutes suffice thoroughly to clean, say, a gearbox and all its parts. For some details, paraffin is used, the tank having a semi-rotary hand pump and nozzle;• this, however, is mostly employed by the docking shop.
For overhaul, all engine bearings are remetalled. The big-ends are bored in the maihine shop, but in the case of the main bearings this operation is carried out in situ, utilizing boring bars of the company's own make.
Two simple jigs and milling tools are employed for cutting the mud grooves, also for finishing, whilst another gives such a good surface on the white metal that practically no fitting is required. The bearings are finished quite circular, the only relief being the 'mud grooves, Dealing with the Cylinders.
The cylinders are either reground or, resleeved. In the older types cast-, iron valve-seat inserts are pressed in ; in later models the Stellite seats are screwed, In each case they are finished in a Black and Decker machine. It is noteworthy that no valve grinding with paste is required, facing the valves and machine grinding of the seats being effective,
The heads are all tested by compressed air at 80 lb, pressure, this being done both before the heads leave the machine shop and after assembly_ The heads and blocks are also tested for
water-tightness. Many hundreds of the earlier models had a flanged joint between the exhaust manifold and pipe, and it was found preferable to utilize a coned joint, so special cutters were devised tp make the alteration—there are actually two, one for the manifold and one for the exhaust pipe. In connection with the reduction of oil consumption special baffies are used in the crankcase and cylinder head. To
accommodate these in the crankcase a machining operation is carried out, but those in the head are held in position by the valve-spring seats.
One little trouble which used to be experienced was excessive wear of the valve-seat inserts. It was eventually decided that this resulted from overheating, because the inserts were too small. They are now made deeper, and this overcomes the difficulty because the heat is more evenly distributed through the head casting.
Crankshafts are reground, as are, in most cases, the valve-rocker pads Pistons when badly worn are renewed. All cylinder blocks are ground out to specific standards, for which pistons are always available.
Several makes of hardened cylinder liner are now available, but, so far, only those of the centrifugally cast type have been employed. These have proved quite satisfactory and are found to give a long wearing life.
Valve springs are carefully tested by screwing them down against a spring balance: each type must show a certain figure.
After overhaul every engine is started by hand, which ensures that it has not been too tightly fitted, and is run light for an hour and for a further three hours against a • fan dynamometer.
Working through the chassis, clutches are relined if more than a little worn, nothing being left to chance. Gearboxes are tested for noise, and pinions and bearings renewed where their remaining life is estimated to be less than 49,000 miles. Axle shafts, drop arms and other important details are carefully examined on an E.
c48
and E. Magnaflux crack detector. Tapers for hubs, etc., are ground true and, if worn where the oil seals bear, are built up. Incidentally, the latter are all renewed. The building-up pro, cess is also carried out by oxy-acetylene welding in the case of worn shackles, brake cams, clutch pedals, etc.
Chassis frames are carefully checked at every overhaul, mainly for twist, whilst brake rods are examined and straightened, if neceq.sary, in the smithy. Front axles all go to the machine shop to ascertain if they be in correct alignment.
A well-fitted electrical repair shop deals with magnetos, dynamos, lamps and windscreen wipers. Remagnetizing can be performed without as mantling a magneto, but during overhaul the instruments are stripped. After completion they are run on the belt for one hour and visually tested on a spark gap which, normally, is about 8 mm., but varies with the type of magneto.
The Exide batteries arc replated where necessary, but during docking can be boosted in position by leads hanging from the roof.
At one time nearly all the vehicles were fitted with Autovac fuel-supply instruments, and a special testing plant deals with these. Later, petrol pumps became popular. At first these gave rather a lot of trouble, but are now much more efficient.
Wings and bonnets are mostly made at Frenchwood, where, also, radiator repairs are carried out. The company does all its own bodywork repairs, including trinnning, It is, of course, unnecessary completely to strip bus bodies, but wheel-arch panels and rear-corner panels are always removed to permit examination of hidden pillars. The paintwork is done by brush.