York's Northallerton plant in full swing
Page 49
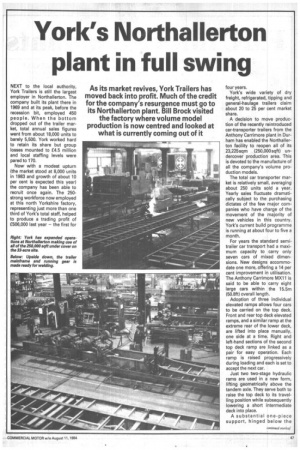
Page 50
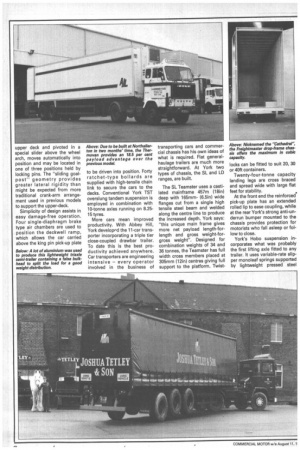
Page 51
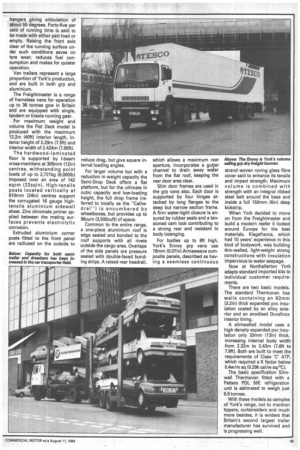
If you've noticed an error in this article please click here to report it so we can fix it.
As its market revives, York Trailers has moved back into profit. Much of the credit for the company's resurgence must go to its Northallerton plant. Bill Brock visited the factory where volume model production is now centred and looked at what is currently coming out of it
NEXT to the local authority, York Trailers is still the largest employer in Northallerton. The company built its plant there in 1969 and at its peak, before the recession bit, employed 450 people. When the bottom dropped out of the trailer market, total annual sales figures went from about 18,000 units to barely 5,500. York worked hard to retain its share but group losses mounted to £4.5 million and local staffing levels were pared to 170.
Now with a modest upturn (the market stood at 8,000 units in 1983 and growth of about 10 per cent is expected this year) the company has been able to recruit once again. The 250strong workforce now employed at this north Yorkshire factory, representing just more than one third of York's total staff, helped to produce a trading profit of £506,000 last year — the first for four years.
York's wide variety of dry freight, refrigerated, tipping and general-haulage trailers claim about 20 to 25 per cent market share.
A decision to move production of the recently reintroduced car-transporter trailers from the Anthony Carrimore plant in Durham has enabled the Northallerton facility to reopen all of its 23,225 sqm (250,000 sqft) undercover production area. This is devoted to the manufacture of all the company's volume production models.
The total car transporter market is relatively small, averaging about 250 units sold a year. Yearly sales fluctuate dramatically subject to the purchasing dictates of the few major companies who have charge of the movement of the majority of new vehicles in this country. York's current build programme is running at about four to five a month.
For years the standard semitrailer car transport had a maximum capacity to carry only seven cars of mixed dimensions. New designs accommodate one more, offering a 14 per cent improvement in utilisation. The Anthony Carrimore MX11 is said to be able to carry eight large cars within the 15.5m (50.8ft) overall length.
Adoption of three individual elevated ramps allows four cars to be carried on the top deck. Front and rear top deck elevated ramps, and a similar ramp at the extreme rear of the lower deck, are lifted into place manually, one side at a time. Right and left,hand sections of the second top deck ramp are linked as a pair for easy operation. Each ramp is raised progressively during loading and each is set to accept the next car.
Just two two-stage hydraulic rams are used in a new form, lifting geometrically above the tandem axle. They serve both to raise the top deck to its travelling position while subsequently lowering a short intermediate deck into place.
A substantial one-piece support, hinged below the upper deck and pivoted in a special slider above the wheel arch, moves automatically into position and may be located in one of three positions held by locking pins. The "sliding goalpost" geometry provides greater lateral rigidity than might be expected from more traditional crank-arm arrangement used in previous models to support the upper-deck.
Simplicity of design assists in easy damage-free operation. Four single-diaphragm brake type air chambers are used to position the deckwell ramp, which allows the car carried above the king pin pick-up plate to be driven into position. Forty ratchet-type bollards are supplied with high-tensile chain link to secure the cars to the decks. Conventional York TST overslung tandem suspension is employed in combination with 10-tonne axles running on 8.2515 tyres.
More cars mean improved productivity. With Abbey Hill, York developrd the 11-car transporter incorporating a triple tier close-coupled drawbar trailer. To date this is the best productivity achieved anywhere. Car transporters are engineering intensive — every operator involved in the business of
transporting cars and commercial chassis has his own ideas of what is required. Flat generalhaulage trailers are much more straightforward. At York two types of chassis, the SL and LD ranges, are built.
The SL Teamster uses a castilated mainframe 457m (18in) deep with 165mm(6.5in) wide flanges cut from a single high tensile steel beam and welded along the centre line to produce the increased depth. York says: "this unique main frame gives more net payload length-forlength and gross weight-forgross weight". Designed for combination weights of 34 and 36 tonnes, the Teamster has full width cross members placed at 305mm (12in) centres giving full support to the platform. Twist locks can be fitted to suit 20, 30 or 40ft containers.
Twenty-four-tonne capacity landing legs are cross braced and spread wide with large flat feet for stability.
At the front end the reinforced pick-up plate has an extended rolled lip to ease coupling, while at the rear York's strong anti-underrun bumper mounted to the chassis provides protection for motorists who fall asleep or follow to close.
York's Hobo suspension incorporates what was probably the first lifting axle fitted to any trailer. It uses variable-rate slipper monoleaf springs supported by lightweight pressed steel hangers giving articulation of about 55 degrees. Forty-five per cent of running time is said to be made with either part load or empty. Raising the front axle clear of the running surface under such conditions saves on tyre wear, reduces fuel consumption and makes for quieter operation.
Van trailers represent a large proportion of York's production, and are built in both grp and aluminium.
The Freightmaster is a range of frameless vans for operation up to 38 tonnes gcw in Britain and are equipped with single, tandem or triaxle running gear.
For maximum weight and volume the Flat Deck model is produced with the maximum 12.2m (40ft) interior length, interior height of 2.29m (7.5ft) and interior width of 2.424m (7.95ft).
The hardwood-laminated floor is supported by I-beam cross-members at 305mm (121n) centres, withstanding point loads of up to 2,721kg (6,0001b) imposed over an area of 142 sqcm (22sqin). High-tensile posts located vertically at 610mm (24in) centres support the corrugated 16 gauge hightensile aluminium sidewall sheet. Zinc chromate primer applied between the mating surfaces prevents electrolytic corrosion.
Extruded aluminium corner posts fitted to the front panel are radiused on the outside to reduce drag, but give square internal loading angles.
For larger volume but with a reduction in weight capacity the Semi-Drop Deck offers a flat platform, but for the ultimate in cubic capacity and low-loading height, the full drop frame (referred to locally as the "Cathedral'') is encumbered by wheelboxes, but provides up to 96cum (3,500cuft) of space.
Common to the entire range, a one-piece aluminium roof is edge sealed and bonded to the roof supports with all rivets outside the cargo area. Overlaps of the side panels are pressure sealed with double-faced bonding strips. A raised rear headrail, which allows a maximum rear aperture, incorporates a gutter channel to drain away water from the flat roof, keeping the rear door area clear.
Slim door frames are used in the grp vans also. Each door is supported by four hinges attached by long flanges to the deep but narrow section frame. A firm water-tight closure is ensured by rubber seals and a tensioned cam lock contributing to a strong rear end resistant to body lozenging.
For bodies up to 8ft high, York's Envoy grp vans use 18mm (0.07in) Armaweave composite panels, described as having a seamless continuous strand woven roving glass fibre cover said to enhance its tensile and impact strength. Maximum volume is combined with strength with an integral ribbed steel belt around the base and inside a full 150mm (6in) deep kickstrip.
When York decided to move on from the Freightmaster and build a modern reefer it looked around Europe for the best materials. Klegefrance, which had 10 years' experience in this kind of bodywork, was building thin-walled, light-weight strong constructions with insulation impervious to water seepage.
Now at Northallerton York adapts standard imported kits to individual customer requirements.
There are two basic models. The standard Thermovan has walls containing an 83mm (3.2in) thick expanded pvc insulation coated by an alloy exterior and an anodised Duralinox interior lining.
A slimwalled model uses a high density expanded pvc insulation only 33mm (13in) thick, increasing internal body width from 2.32m to 2.43m (7.6ft to 7.9ft). Both are built to meet the requirements of Class 'C' ATP, which required a K factor below 0.4w/m sq (0.29k cal/w sq/°C).
The basic specification Slimwall Thermovan fitted with a Petters PDL 50E refrigeration unit is estimated to weigh just 6.9 tonnes.
With these models as samples of York's range, not to mention tippers, curtainsiders and much more besides, it is evident that Britain's second largest trailer manufacturer has survived and is progressing well.