• Plastics pioneers set for big future
Page 70
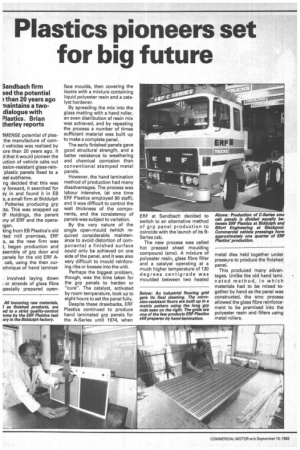
Page 71
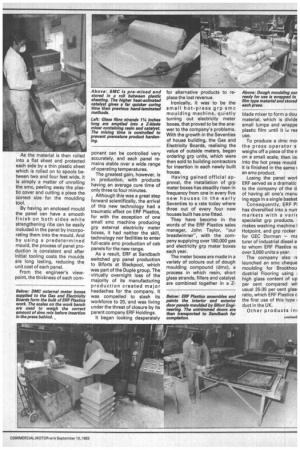
Page 72

If you've noticed an error in this article please click here to report it so we can fix it.
Sandbach firm sed the potential than 20 years ago naintains a twodialogue with Plastics. Brian therley reports
11V1ENSE potential of plasthe manufacture of coma vehicles was realised by ore than 20 years ago. It d that it would pioneer the uction of vehicle cabs out osion-resistant glass-reinplastic panels fixed to a :eel subframe.
rig decided that this was iy forward, it searched for 3y in and found it in EB s, a small firm at Biddul ph Potteries producing grp :Is. This was snapped up IF Holdings, the parent iny of ERF and the opera:gen.
king from EB Plastics's old led mill premises, ERF s, as the new firm was began production and ssembly of grp door and panels for the old ERF Acab, using the then cur!chnique of hand laminat involved laying down ; or strands of glass fibre ipeciatly prepared open
face moulds, then covering the layers with a mixture containing liquid polyester resin and a catalyst hardener.
By spreading the mix into the glass matting with a hand roller, an even distribution of resin mix was achieved, and by repeating the process a number of times sufficient material was built up to make a complete panel.
The early finished panels gave good structural strength, and a better resistance to weathering and chemical corrosion than conventional stamped metal panels.
However, the hand lamination method of production had many disadvantages. The process was labour intensive, (at one time ERF Plastics employed 90 staff), and it was difficult to control the wall thickness of the components, and the consistency of panels was subject to variation.
By the very nature of the single open-mould (which required considerable maintenance to avoid distortion of components) a finished surface could only be achieved on one side of the panel, and it was also very difficult to mould reinforcing ribs or bosses into the unit.
Perhaps the biggest problem, though, was the time taken for the grp panels to harden or "cure". The catalyst, activated by room temperature, took up to eight hours to set the panel fully.
Despite these drawbacks, ERF Plastics continued to produce hand laminated grp panels for the A-Series until 1974, when ERF at Sandbach decided to switch to an alternative method of grp panel production to coincide with the launch of its BSeries cab.
The new process was called hot pressed sheet moulding compound (smc). A mixture of polyester resin, glass fibre filler and a catalyst operating at a much higher temperature of 130 degrees centigrade was moulded between two heated metal dies held together under pressure to produce the finished panel.
This produced many advantages. Unlike the old hand laminated method, in which materials had to be mixed together by hand as the panel was constructed, the smc process allowed the glass fibre reinforcement to be premixed into the polyester resin and fillers using metal rollers. As the material is then rolled into a flat sheet and protected each side by a thin plastic sheet which is rolled on to spools between two and four feet wide, it is simply a matter of unrolling the smc, peeling away the plastic cover and cutting a piece the correct size for the moulding tool, By having an enclosed mould the panel can have a smooth finish on both sides while strengthening ribs can be easily included in the panel by incorporating them into the mould. And by using a predetermined mould, the process of panel production is consistent and after initial tooling costs the moulds are long lasting, reducing the unit cost of each panel.
From the engineer's viewpoint, the thickness of each corn ponent can be controlled very accurately, and each panel remains stable over a wide range of operating temperatures.
The greatest gain, however, is in production, with products having an average cure time of only three to four minutes.
, Although this was a great step forward scientifically, the arrival of this new technology had a traumatic effect on ERF Plastics, for with the exception of one small smc machine producing grp external electricity meter boxes, it had neither the skill, technology nor facilities to enter full-scale smc production of cab panels for the new range.
As a result, ERF at Sandbach switched grp panel production to Biforts at Blackpool, which was part of the Duple group. The virtually overnight loss of the majority of its manufacturing production created major headaches for the company. It was compelled to slash its workforce to 20, and was living under the threat of closure by its parent company ERF Holdings.
It began looking desperately for alternative products to replace the lost revenue.
Ironically, it was to be the small hot-press grp smc moulding machine, quietly turning out electricity meter boxes, that proved to be the answer to the company's problems. With the growth in the Seventies of house building, the Gas and Electricity Boards, realising the value of outside meters, began ordering grp units, which were then sold to building contractors for insertion in each newly built house.
Having gained official approval, the installation of grp meter boxes has steadily risen in frequency from one in every five new houses in the early Seventies to a rate today where three out of every four new houses built has one fitted.
They have become in the words of the ERF Plastics sales manager, John Taylor, "our breadwinner", with the company supplying over 180,000 gas and electricity grp meter boxes each year.
The meter boxes are made in a variety of colours out of dough moulding compound (dmc), a process in which resin, short glass strands, fillers and catalyst are combined together in a Z blade mixer to form a dou material, which is divide small lumps and wrappe plastic film until it i rea use.
To produce a dmc mol the press operator s weighs off a piece of the n on a small scale, then int into the hot press mould it is finished in the same 1 an smc product.
Losing the panel worl, ERF served as a dramatic to the company of the d. of having all one's menu ing eggs in a single basket
Consequently, ERF PI has diversified into a nun' markets with a variE specialist grp products. makes washing machine I Hotpoint, and grp rocker for GEC Dorman — ma turer of industrial diesel e to whom ERF Plastics si over 3,000 units a year.
The company also rE launched an smc cheque moulding for Brockhou dustrial Flooring using i high glass content of up per cent compared wil usual 25-35 per cent glas: ratio, which ERF Plastics c the first use of this type I duct in the UK.
Other products ini aild, a d-i-y cement brick I made out of grp which [(inched last year but so far ot been extensively marand an smc moulding for machines.
) expand into any market an," says John Taylor. e's no such thing as full ty. We work day and night and weekends and this ur turnover will be close to decision by ERF Holdings close down the Biddulph y has been well rewarded ERF Plastics expanding on le between 20 to 30 per ach year since.
Holdings has responded resting capital in the cornThe workforce is back to now has 11 smc presses. Taylpr feels it now gets a support from the parent any, providing "we can )ur figures right."
company came full circle e 1979 when it was aped by ERF at Sandbach a view to supplying smc 5 for the current C-Series job is split equally beERF Plastics at Biddulph .ifort Engineering, a situaohn Taylor prefers to the -Series days of total prom. Bifort makes roof, back 5, doors and grilles, while Plastics produces wings, panels, mid rails, step ; and assembles the inner )uter untrimmed door ; produced by Bifort.
return to the commercial e market has not been ut its problems, particua light of the recession and fect it has had on product Sandbach.
a work we do for ERF is 50 per cent," John Taylor ie. "That's why we look to cts like chequerplate."
ipite of the problems at )ach and the reduction in ibuilding which has hit boxes, ERF Plastics has ged to increase its penetrain decreasing markets. y competitors have gone the business," says John; I we've bought three as from one that's just I down."
jinally regarded with susby some operators and aers (possibly as a legacy the old hand lamination grp in either dmc or smc ong since become the ted engineering material mmercial vehicle manufaclooking to replace heavy KI metal components with r units, without sacrificing ct strength. However, the use of grp has remained confined to the cab and John Taylor feels that there are many revolutionary applications to which grp can be put.
"All the easy jobs have been done. We're now going into new markets, asking the material to do things it's never done before," he said. For example, producing whole cab units out of grp rather than having a steel subframe as a supporting base.
While still very much on the drawing board in this country, earlier this year in the United States GMC announced its intention to build a totally grp-cabbed version of its top-weight tractive unit — the GMC General — with the result that a number of these vehicles with double-skinned grp cabs are currently undergoing operational fleet trials.
If the concept of complete grp cabs proves to be successful, then the three or four-year corrosion warranties being offered on today's steel-cabbed vehicles will be as redundant as ten shilling notes.
The never-ending search for lightweight materials to replace steel has seen grp joined by carbon fibre, which has been used to a large extent in Ford's Concept Cargo, although its application is likely to be restricted by the very nature of its construction.
A carbon fibre panel with a random fibre pattern similar to grp offers only marginally better performance than glass reinforced plastic, with the process of producing an equivalent carbon fibre panel being longer and more expensive than smc.
If, however, the carbon fibres (which are held together by 6poxides rather than with polyester resins) are laid down in a unidirectional form, the unit strength is far superior to grp.
ERF Plastics sees the use of carbon fibre in commercial vehicle construction restricted to structures like axle beams or in the case of Ford's Concept Cargo, prop shafts, where the unidirectional forces of the carbon fibres can be arranged in the direction of the applied torque.
For many grp manufacturers, the method of establishing final product specifications has been somewhat vague, with practical experience playing a great part in the final dimensions of a moulding.
In search of a more scientific approach, three years ago ERF Plastics set up a Finite Element Analysis (FEA) programme jointly funded with the Polymer Engineering Directorate and housed at Nottingham University.
Run by postgraduate students, the FEA programme involved exhaustive tests on grp products. The results, which are due to be released this month, will give ERF Plastics two important future reference sources for component predictability — the FEA programme includes full destruction tests on a number of grp components including some made by ERF Plastics; and from a cost-saving criteria, the minimum safe specification required by each moulding should emerge.
ERF Plastics also stands to gain a commercial advantage over its competitors for the results of the programme, which it claims is the first of its kind to be carried out in the UK, will remain the property of ERF Plastics for the next two years.
All this information will be shared with colleagues at Sandbach, with whom ERF Plastics maintains a constant twoway dialogue. Ultimately though, the final specification for cv components comes from ERF Ltd.
The recent manufacturing agreement struck between ERF and Japanese lorry manufacturer Hino, whereby Sandbach will assemble 12 to 15-ton fourwheel vehicles, is unlikely to have an immediate effect at Biddulph.
The UK-built vehicles will use Hino's all-steel cab (launched 18 months ago), although ERF Ltd hopes that Hino will take advantage of its experience with smc components for use in markets which do not want steel cabs.
ERF Plastics managing director Harry Knight has already played host to a party of Japanese visitors, although he does not see any sudden changes in the company's business as a result of the Japanese/British deal.
"It's early days, but I don't see us selling smc parts to Japan, although if Nino does use smc, we would hope to do the moulding for UK models."
One criticism arising out of the use of glass-reinforced plastics in commercial vehicle construction is the difficulty some operators have experienced in maintaining an acceptable paint finish compared to that on conventional pressed steel panels.
The solution says ERF Plastics is to prepare correctly and prime each panel before final painting, although John Taylor also feels that failing to remove all residual releasing agent, which is included in the grp mixture and collects on the outer panel skin preventing the pressing sticking to the mould, may affect paint bonding.
Ironically, the very use of smc components seems to make vehicle painting unnecessary, particularly as the original reason for doing so is to provide steel bodywork with a corrosionresistant finish — a quality already inherent in grp.
With grp commercial vehicle mouldings forming only 20 to 25 per cent of the total production of ERF Plastics, sharing the same name as the vehicle manufacturing division has had its drawbacks as far as ERF Plastics is concerned. Some prospective customers wrongly assume that ERF Plastics is a part of the Sandbach lorry builder, ERF Ltd, a misunderstanding Harry Knight is quick to dispel.
"ERF Ltd has no control in this factory. We're completely independent. We can talk to Seddon Atkinson or Leyland in absolute confidence."
ERF Plastics has come almost full circle since they started 20 years ago, although it is unlikely that it will ever again be in danger of closing.
If the business continues to expand successfully, people might one day have a different confusion over the relationship between ERF Plastics and ERF Ltd. They might think ERFL is part of ERFP!