Fifty proud years for our sole survivor
Page 39
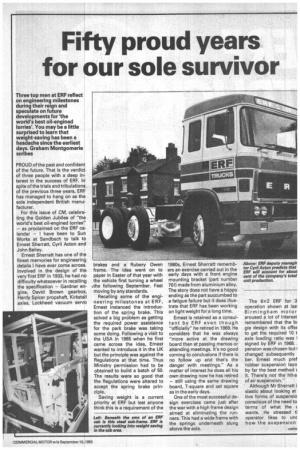
Page 40
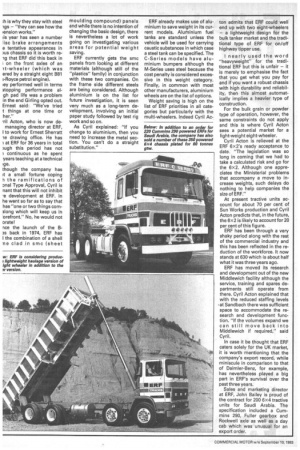
If you've noticed an error in this article please click here to report it so we can fix it.
Three top men at ERF reflect on engineering milestones during their reign and speculate on future developments for 'the world's best oil-engined lorries'. You may be a little surprised to learn that weight-saving has been a headache since the earliest days. Graham Montgomerie scribes PROUD of the past and confident of the future. That is the verdict of three people with a deep interest in the success of ERF. In spite of the trials and tribulations, of the previous three years, ERF has managed to hang on as the sole independent British manufacturer.
For this issue of CM, celebrating the Golden Jubilee of "the world's best oil-engined lorries" — as proclaimed on the ERF calendar — I have been to Sun Works at Sandbach to talk to Ernest Sherratt, Cyril Acton and John Bailey.
Ernest Sherratt has one of the finest memories for engineering details I have ever come across. Involved in the design of the very first ERF in 1933, he had no difficulty whatsoever in recalling the specification — Gardner engine, David Brown gearbox, Hardy Spicer propshaft, Kirkstall axles, Lockheed vacuum servo brakes and a Rubery Owen frame. The idea went on to paper in Easter of that year with the vehicle first turning a wheel the following September. Fast moving by any standards.
Recalling some of the engineering milestones at ERF, Ernest instanced the introduction of the spriing brake. This solved a big problem as getting the required power assistance for the park brake was taking some doing. Following a visit to the USA in 1965 when he first came across the idea, Ernest wanted to introduce it in the UK but the principle was against the Regulations at that time. Thus Ministry permission had to be obtained to build a batch of 50. The results were so good that the Regulations were altered to accept the spring brake principle.
Saving weight is a current priority at ERF but lest anyone think this is a requirement of the 1980s, Ernest Sherratt remembers an exercise carried out in the early days with a front engine mounting bracket (part number 70!) made from aluminium alloy. The story does not have a happy ending as the part succumbed to a fatigue failure but it does illustrate that ERF has been working on light weight for a long time.
Ernest is retained as a consultant by ERF even though "officially" he retired in 1969. He considers that he was always "more active at the drawing board than at passing memos or attending meetings. It's no good coming to conclusions if there is no follow up and that's the danger with meetings." As a matter of interest he does all his own drawing now he has retired — still using the same drawing board, T-square and set square as in the early days.
One of the most successful design exercises came just after the war with a high frame design aimed at eliminating the runners. This had a wide frame with the springs underneath slung above the axle. The 6x2 ERF for 3 operation shown at Iasi Birmingham motor aroused a lot of interest remembered that the IN gie design with its offse to get the required 10 t axle loading ratio was I signed by ERF in 1968. , pension was chosen but I changed subsequently ber. Ernest much pref rubber suspension layo by far the best method c it. There's not the hit-a of air suspension."
Although Mr Sherratt i siastic about looking at tive forms of suspensio conscious of the need to terms of what the c wants. He stressed tl operator likes to unc how the suspension
:h is why they stay with steel igs — "they can see how the iension works."
is year has seen a number isc brake arrangements e tentative appearances in )us chassis so it is worth re
ig ERF did this back in
• on the front axles of an it-wheeler (which was ered by a straight eight B81 ;-Royce petrol engine).
ley performed well in terms stopping performance algh pad life was a problem in the end Girling opted out. Ernest said: "We've tried t things at one time or her."
'ril Acton, who is now demanaging director at ERF, Ito work for Ernest Sherratt le drawing office. He has at ERF for 36 years in total nigh this period has not 1 continuous as he spent years teaching at a technical !ge.
though the company has it a small fortune coping n the ramifications of 3 nal Type Approval, Cyril is nant that this will not inhibit -e development at ERF. In he went so far as to say that has "one or two things cornalong which will keep us in orefront." No, he would not orate!
ice the launch of the Bs back in 1974, ERF has I the combination of a shell ne clad in smc (sheet
moulding compound) panels and while there is no intention of changing the basic design, there is nevertheless a lot of work going on investigating various areas for potential weight saving.
ERF currently gets the smc panels from looking at different materials (although still of the "plastics" family) in conjunction with these two companies. On the frame side different steels are being considered. Although aluminium is on the list for future investigation, it is seen very much as a long-term development, involving an initial paper study followed by test rig work and so on.
As Cyril explained: "If you change to aluminium, then you need to increase the metal section. You can't do a straight substitution." ERF already makes use of aluminium to save weight in its current models. Aluminium fuel tanks are standard unless the vehicle will be used for carrying caustic substances in which case a steel tank can be specified. The C-Series models have aluminium bumpers although the M-Series uses steel because the cost penalty is considered excessive in this weight category. Finally, in common with most other manufacturers, aluminium wheels are on the list of options.
Weight saving is high on the list of ERF priorities in all categories but particularly with the multi-wheelers. Indeed Cyril Ac ton admits that ERF could well end up with two eight-wheelers — a lightweight design for the bulk tanker market and the traditional type of ERF for on/off highway tipper use.
I nearly used the word "heavyweight" for the traditional ERF but this is unfair — it is merely to emphasise the fact that you get what you pay for and if you want a robust chassis with high durability and reliability, then this almost automatically implies a heavier type of construction.
For the bulk grain or powder type of operation, however, the same constraints do not apply and this is where Cyril Acton sees a potential market for a light-weight eight-wheeler.
Cyril Acton is relieved at the ERF 6x2's ready acceptance to date. "The legislation was so long in coming that we had to take a calculated risk and go for the 6x2. Although one appreciates the Ministerial problems that accompany a move to increase weights, such delays do nothing to help companies the size of ERF."
At present tractive units account for about 70 per cent of Sun Works production and Cyril Acton predicts that, in the future, the 6x2 is likely to account for 20 per cent of this figure.
ERF has been through a very shaky period along with the rest of the commercial industry and this has been reflected in the reduction of the workforce. It now stands at 630 which is about half what it was three years ago.
ERF has moved its research and development out of the new Middlewich facility although the service, training and spares departments still operate from there. Cyril Acton explained that with the reduced staffing levels at Sandbach there was sufficient space to accommodate the research and development function. "If the volumes expand we can still move back into Middlewich if required," said Cyril.
In case it be thought that ERF caters solely for the UK market, it is worth mentioning that the company's export record, while miniscule in comparison to that of Daimler-Benz, for example, has nevertheless played a big part in ERF's survival over the past three years.
Sales and marketing director at ERF, John Bailey is proud of the contract for 200 6x4 tractive units for Saudi Arabia. The specification included a Cummins 290, Fuller gearbox and Rockwell axle as well as a day cab which was unusual for an export order.