A Simple New Syster • of Unloading Powde
Page 48
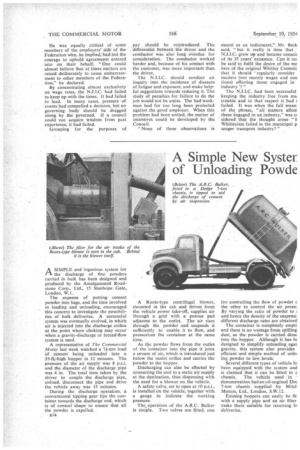
If you've noticed an error in this article please click here to report it so we can fix it.
ASIMPLE and ingenious system for the discharge of fine powders carried in bulk has been designed and prOduced by the Amalgamated Roadstone Corp., Ltd., 15 Stanhope Gate, London, W.I.
The expense of putting cement powder into bags, and the time involved in loading and unloading, encouraged this concern to investigate the possibilities of bulk deliveries, A successful system was eventually evolved, in which air is injected into the discharge orifice at the point where choking may occur when a gravity-discharge or forced-flow system is used.
A representative of The Commercial Motor last week watched a 7i-ton load Of cement being unloaded into a 35-4.-high hopper in 12 minutes. The pressure of the air supply was 8 p.s.i. and the diameter of the discharge pipe was 4 in. The total time taken by the driver to couple the discharge pipe, unload, disconnect the pipe and drive the vehicle away was 15 minutes.
During the discharge operation; a conventional tipping gear tips the container towards the discharge end, which is of conical 'shape to ensure that all the powder is expelled.
B14 A Roots-type centrifugal blower, Mounted in the cab and driven from the vehicle power take-off, supplies air through a grid with a porous pad adjacent to the outlet. The air rises through the powder and suspends it sufficiently to enable it to flow, and pressurizes the container at the same time.
AS the powder flows from the outlet of the containerinto the pipe it joins a stream of air, which is introduced just below the outlet orifice and carries the powder to the hopper.
Discharging can also be effected by connecting the unit to a static air supply at the destination, thus dispensing with the need for a blower on the vehicle.
A safety valve, set to open at 10 p.s.i., is installed On the vehicle, together with a gauge to indicate the working pressure.
The operation of the A.R.C. Bulker is simple. Two valves are fitted, one for controlling the flow of powder a the other to control the air press'. By varying the ratio of powder to 1 and hence the density of the suspensi different discharge rates are obtained The container is completely empti and there is no wastage from spilling dust, as the powder is carried dire( into the hopper. Although it has IN designed to simplify unloading agai gravity, this system also provides efficient and simple method of link); ing powder to low levels.
Several different types of vehicle In been equipped with the system and is claimed that it can be fitted to a chassis. The vehicle used in • demonstration had an oil-engined Dos 7-ton chassis supplied by Mita Motors, Ltd., London, S.W.I2.
Existing hoppers can easily be fit with a supply pipe and an air filter make them suitable for receiving bi deliveries.