Spraying Five Coats in One Day
Page 43
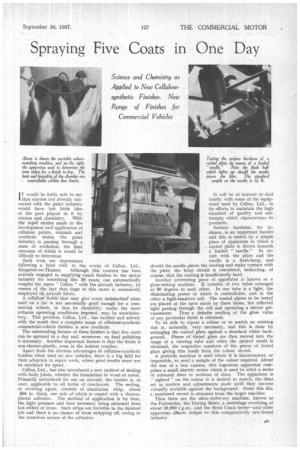
If you've noticed an error in this article please click here to report it so we can fix it.
iT would be fairly safe to say that anyone not directly connected with the paint industry would have but little idea of the part played in it by science and chemistry. With the rapid strides made in the development and application of cellulose paints, enamels and synthetic resins, the paint industry is passing through a state of evolution, the final Outcome of which it would be difficult to determine.
Such were our impressions following a brief visit to the works of Cellon, Ltd., Kingston-on-Thames, Although this concern has been actively engaged in supplying coach finishes to the motor industry for something like 20 years, one automatically couples the name " Cellon" with the aircraft industry, by reason of the fact that dope of this name is extensively employed on aircraft fabric.
A cellulose finish that may give every satisfaction when used on a car is not necessarily good enough for a commercial vehicle, in that its durability, under the more arduous operating conditions imposed, may be unsatisfactory. This problem, Cellon, Ltd., has tackled and solved, with the result that a complete range of cellulose,-synthetic commercial-vehicle finishes is now available.
The outstanding feature of these finishes is that five coats can be sprayed in a day and, moreover, no final polishing is necessary. Another important feature is that the finish is non-thermo-plastic, even in the hottest weather.
Apart from the obvious advantages of cellulose-synthetic finishes when used on new vehicles, there is a big field for their adoption in repair work, where good results must not be sacrificed for speed.
Cellon, Ltd., has also introduced a new method of dealing with body joints, whether the foundation be wood or metal. Primarily introduced for use on aircraft, the system is, at once, applicable to all forms of coachwork. The sealing, or covering agent, consists of aluminium strip, about .004 in. thick, one side of which is coated with a thermoplastic adhesive. The method of application is by heat, the light pressure and heat necessary being obtained from hot -rollers or irons. Such strips are invisible in the finished job and there is no chance of them stripping off, owing to the tenacious nature of the adhesive. It will be of interest to deal briefly with some of the equipment used by Cellon, Ltd., in its efforts to maintain the high standard of quality and uniformity which characterizes its products.
Surface hardness, for instance, is an important feattire and this is tested by a simple piece of apparatus in which a coated plate is drawn beneath a loaded " needle." In circuit with the plate and the needle is a flash-lamp, and should the needle pierce the coating and make contact with the plate, the lamp circuit is completed, indicating, of course, that the coating is insufficiently bard. Another interesting piece of appafatus is known as a gloss-testing machine. It consists of two tubes arranged at 90 degrees to each other. In one tube is a light, the illuminating power of which is controllable, and in the other a light-sensitive cell. The coated plates to be tested are placed at the apex made by these tubes, the reflected light passing through the cell and operating a mirror galvanometer. Thus a definite reading of the gloss value of any particular finish is obtained. To be able to repeat a colour or to match an existing tint is, naturally, very necessary, and this is done by arranging the coated plate against a standard white background. Pieces of tinted glass are then moved into the range of a viewing tube and when the desired result is obtained, the respective numbers of the pieces of tinted glass giving this result form the colour record. A portable machine is used where it is inconvenient, or impossible, to send a sample of the colour required. About the size of a box camera, this ingenious apparatus comprises a small electric motor which is used to whirl a series of coloured discs or sections of discs. The apparatus is " sighted " on the colour it is desired to match, the discs set in motion and adjustments made until they become virtually invisible against the background. From this disc a numbered record is obtained from the larger machine.
Then there are the ultra-violet-ray machine, known as the Fadometer, the Drying Meter, a centrifuge revolving at about 10,000 r.p.m., and the Bend Crack tester—and other apparatus athiost unique to this comparatively new-found industry.