DEMOUNTABLE DISTRIBUTION-15
Page 72
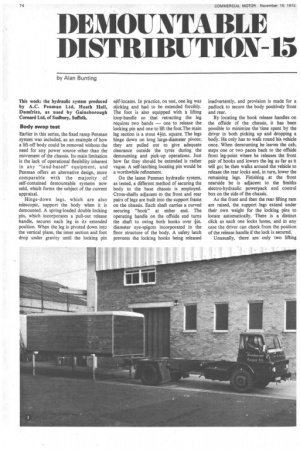
Page 73
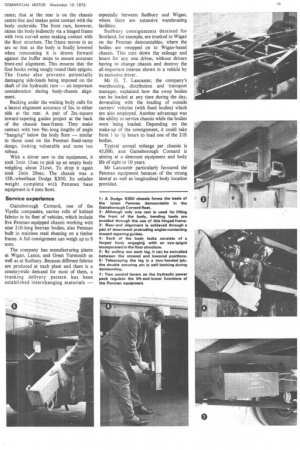
If you've noticed an error in this article please click here to report it so we can fix it.
by Alan Bunting This week: the hydraulic system produced by A.C. Penman Ltd, Heath Hall, Dumfries, as used by Gainsborough Cornard Ltd, of Sudbury, Suffolk.
Body swap test Earlier in this series, the fixed ramp Penman system was included, as an example of how a lift-off body could be removed without the need for any power source other than the movement of the chassis. Its main limitation is the lack of operational flexibility inherent in any "land-based" equipment, and Penman offers an alternative design, more comparable with the majority of self-contained demountable systems now sold, which forms the subject of the current appraisal.
Hinge-down legs, which are also telescopic, support the body when it is demounted. A spring-loaded double locking pin, which incorporates a pull-out release handle, secures each leg in its extended position. When the leg is pivoted down into the vertical plane, the inner section and foot drop under gravity until the locking pin self-locates. In practice, on test, one leg was sicking and had to be extended forcibly. The foot is also equipped with a lifting loop-handle so that retracting the leg requires two hands — one to release the locking pin and one to lift the foot.The main leg section is a stout elfin. square. The legs hinge down on long large-diameter pivots; they are pulled out to give adequate clearance outside the tyres during the demounting and pick-up operations. Just how far they should be extended is rather vague. A self-latching locating pin would be a worthwhile refinement.
On the latest Penman hydraulic system, as tested, a different method of securing the body to the base chassis is employed. Cross-shafts adjacent to the front and rear pairs of legs are built into the support frame on the chassis. Each shaft carries a curved securing "hook" at either end. The operating handle on the offside end turns the shaft to swing both hooks over fin. diameter eye-spigots incorporated in the floor structure of the body. A safety latch prevents the locking hooks being released inadvertently, and provision is made for a padlock to secure the body positively front and rear.
By locating the hook release handles on the offside of the chassis, it has been possible to minimize the time spent by the driver in both picking up and dropping a bod,y. He only has to walk round his vehicle once. When demounting he leaves the cab, steps one or two paces back to the offside front leg-point where he releases the front pair of hooks and lowers the leg as far as it will go; he then walks around the vehicle to release the rear locks and, in turn, lower the remaining legs. Finishing at the front nearside he is adjacent to the Smiths electro-hydraulic powerpack and control box on the side of the chassis.
As the front and then the rear lifting ram are raised, the support legs extend under their own weight for the locking pins to locate automatically. There is a distinct click as each one locks home, and in any case the driver can check from the position of the release handle if the lock is secured.
Unusually, there are only two lifting
rams; that at the rear is on the chassis centre-line and makes point contact with the body underside. The front ram, however, raises the body indirectly via a hinged frame with twin curved arms making contact with the floor structure. The frame moves in an arc so that as the body is finally lowered when remounting it is drawn forward against the buffer stops to ensure accurate front-end alignment. This ensures that the four hooks swing snugly round their spigots. The frame also prevents potentially damaging side-loads being imposed on the shaft of the hydraulic ram — an important consideration during body-chassis alignment.
Backing under the waiting body calls for a lateral alignment accuracy of 3in. to either side at the rear. A pair of 2in.-square inward-tapering guides project at the back of the chassis base-frame. They make contact with two 9in.-long lengths of angle "hanging" below the body floor — similar to those used on the Penman fixed-ramp design, looking vulnerable and none too robust.
With a driver new to the equipment, it took 3min 15sec to pick up an empty body weighing about 2 lewt. To drop it again took 2min 20sec. The chassis was a 15ft.-wheelbase Dodge IC850. Its unladen weight complete with Penman base equipment is 4 tons 8cwt.
Service experience
Gainsborough Cornard, one of the Viyella companies, carries rolls of knitted fabrics in its fleet of vehicles, which include five Penman-equipped chassis working with nine 21ft-long boxvan bodies, also Penman built in stainless steel sheeting on a timber frame. A full consignment can weigh up to 8 tons.
The company has manufacturing plants at Wigan, Lanes, and Great Yarmouth as well as at Sudbury. Because different fabrics are produced at each plant and there is a countrywide demand for most of them, a trunking delivery pattern has been established interchanging materials — especially between Sudbury and Wigan, where there are extensive warehousing facilities.
Sudbury consignments destined for Seotland, for example, are trunked to Wigan on the Penman demountables, where the bodies are swopped on to Wigan-based chassis. This cuts down the mileage and hours for any one driver, without drivers having to change chassis and destroy the all-important interest shown in a vehicle by its exclusive driver.
Mr G. T. Lancaster, the company's warehousing, distribution and transport manager, explained how the swop bodies can be loaded at any time during the day, dovetailing with the loading of outside carriers' vehicles (with fixed bodies) which are also employed. Another advantage was the ability to service chassis while the bodies were being loaded. Depending on the make-up of the consignment, it could take from 1 to I!T hours to load one of the 21ft bodies.
Typical annual mileage per chassis is 45,000, and Gainsborough Cornard is aiming at a demount equipment and body life of eight to 10 years.
Mr Lancaster particularly favoured thi Penman equipment because of the strong lateral as well as longitudinal body location provided.