Piston defects main cause of liesel failures
Page 45
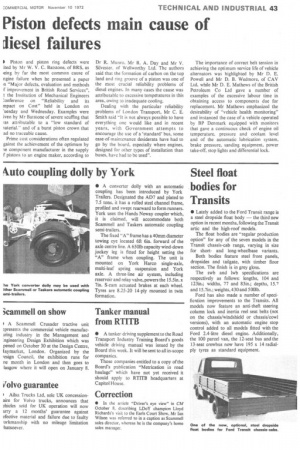
If you've noticed an error in this article please click here to report it so we can fix it.
I Piston and piston ring defects were ited by Mr W. V. C. Batstone, of BRS, as ieing by far the most common cause of ngine failure when he presented a paper n "Major defects, evaluation and methods f improvement in British Road Services", t the Institution of Mechanical Engineers ;onference on "Reliability and its mpact on Cost" held in London on 'uesday and Wednesday. Examples were iven by Mr Batstone of severe scuffing that ,as attributable to a "low standard of taterial." and of a burst piston crown that ad no traceable cause.
Prime cost considerations often regulated gainst the achievement of the optimum by le component manufacturer in the supply f pistons to an engine maker, according to
Dr R. Munro, Mr R. A. Day and Mr V. Silvester, of Wellworthy Ltd. The authors said that the formation of carbon on the top land and ring groove of a piston was one of the most crucial reliability problems of diesel engines. In many cases the cause was attributable to excessive temperatures in this area, owing to inadequate cooling.
Dealing with the particular reliability problems of London Transport, Mr C. E. Smith said -It is not always possible to have everything one would like and in recent years, with Government attempts to encourage the use of a 'standard' bus, some ease-of-maintenance desiderata have had to go by the board, especially where engines, designed for other types of installation than buses, have had to be used".
The importance of correct belt tension in achieving the optimum service life of vehicle alternators was highlighted by Mr D. E. Powell and Mr D. B. Wedmore, of CAV Ltd, while Mr D. E. Mathews of the British Petroleum Co Ltd gave a number of examples of the excessive labour time in obtaining access to components due for replacement. Mr Mathews emphasized the desirability of "vehicle health monitoring" and instanced the case of a vehicle operated by BP Denmark equipped with monitors that gave a continuous check of engine oil temperature, pressure and coolant level and of the automatic lubrication system, brake pressure, sanding equipment, power take-off, stop lights and differential lock.