The men who never
Page 71
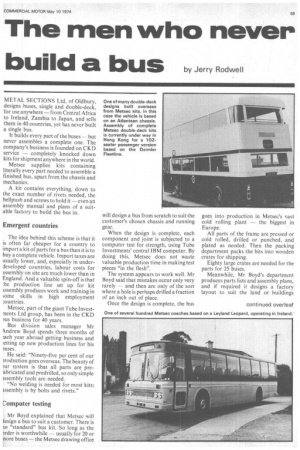
Page 72
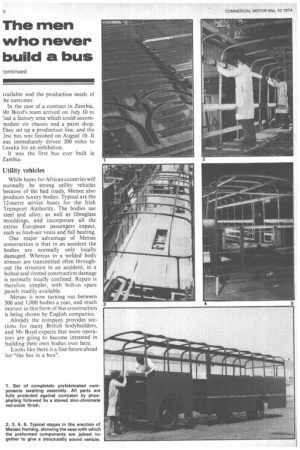
If you've noticed an error in this article please click here to report it so we can fix it.
build a bus by Jerry Rodwell
METAL SECTIONS Ltd, of Oldbury, designs buses, single and double-deck, for use anywhere — from Central Africa to Ireland, Zambia to Japan, and sells them in 40 countries, yet has never built a single bus.
It builds every part of the buses but never assembles a complete one. The company's business is founded on CK D service — completely knocked down kits for shipment anywhere in the world.
Metsec supplies kits containing literally every part needed to assemble a finished bus, apart from the chassis and mechanics.
A kit contains everything, down to the exact number of rivets needed, the bellpush and screws to hold it — even an assembly manual and plans of a suitable factory to build the bus in.
Emergent countries
The idea behind this scheme is that it is often far cheaper for a country to import a kit of parts fora bus than it is to buy a complete vehicle. Import taxes are usually lower, and, especially in underdeveloped countries, labour costs for issembly on site are much lower than in England. And a valuable spin-off is that :he production line set up for kit issembly produces work and training in ;ome skills in high employment ountries.
Metsec, part of the giant Tube Investnents Ltd group, has been in the CKD ms business for 40 years.
Bus division sales manager Mr kndrew Boyd spends three months of !ach year abroad getting business and ;etting up new production lines for his mses.
He said: "Ninety-five per cent of our n-oduction goes overseas. The beauty of mr system is that all parts are preabricated and predrilled, so only simple issembly tools are needed.
"No welding is needed for most kits; issembly is by bolts and rivets."
Computer testing
Mr Boyd explained that Metsec will iesign a bus to suit a customer. There is lo "standard" bus kit. So long as the )rder is worthwhile -usually for 20 or nore buses — the Metsec drawing office will design a bus from scratch to suit the customer's chosen chassis and running gear.
When the design is complete, each component and joint is subjected to a computer test for strength, using Tube Investments' central IBM computer. By doing this, Metsec does not waste valuable production time in making test pieces "in the flesh".
The system appears to work well. Mr Boyd said that mistakes occur only very rarely — and then are only of the sort where a hole is perhaps drilled a fraction of an inch out of place.
Once the design is complete, the bus goes into production in Metsec's vast cold rolling plant — the biggest in Europe.
All parts of the frame are pressed or cold rolled, drilled or punched, and plated as needed. Then the packing department packs the bits into wooden crates for shipping.
Eighty large crates are needed for the parts for 25 buses.
Meanwhile, Mr Boyd's department produces parts lists and assembly plans, and if required it designs a factory layout to suit the land or buildings ivailable and the production needs of :he customer.
In the case of a contract in Zambia, VIr Boyd's team arrived on July 10 to 'ind a factory area which could accommodate six chassis and a paint shop. They set up a production line, and the first bus was finished on August 10. It xas immediately driven 200 miles to Lusaka for an exhibition.
It was the first bus ever built in Zambia.
Utility vehicles
While buses for African countries will normally be strong utility vehicles because of the bad roads, Metsec also produces luxury bodies. Typical are the 12-metre service buses for the Irish Transport Authority. The bodies use steel and alloy, as well as fibreglass mouldings, and incorporate all the extras European passengers expect, such as fresh-air vents and full heating.
One major advantage of Metsec construction is that in an accident the bodies are normally only locally damaged. Whereas in a welded body stresses are transmitted often throughout the structure in an accident, in a bolted and riveted construction damage is normally locally confined. Repair is therefore simpler, with bolt-in spare panels readily available.
Metsec is now turning out between 500 and 1,000 bodies a year, and much interest in this form of bus construction is being shown by English companies.
Already the company provides sections for many British bodybuilders, and Mr Boyd expects that more operators are going to become intrested in building their own bodies over here.
Looks like there is a fine future ahead for "the bus in a box".